Algorithm flow chart, Block transfer programming, 3ć51 – Rockwell Automation 1771-PD PID MODULE (+DU) User Manual
Page 94
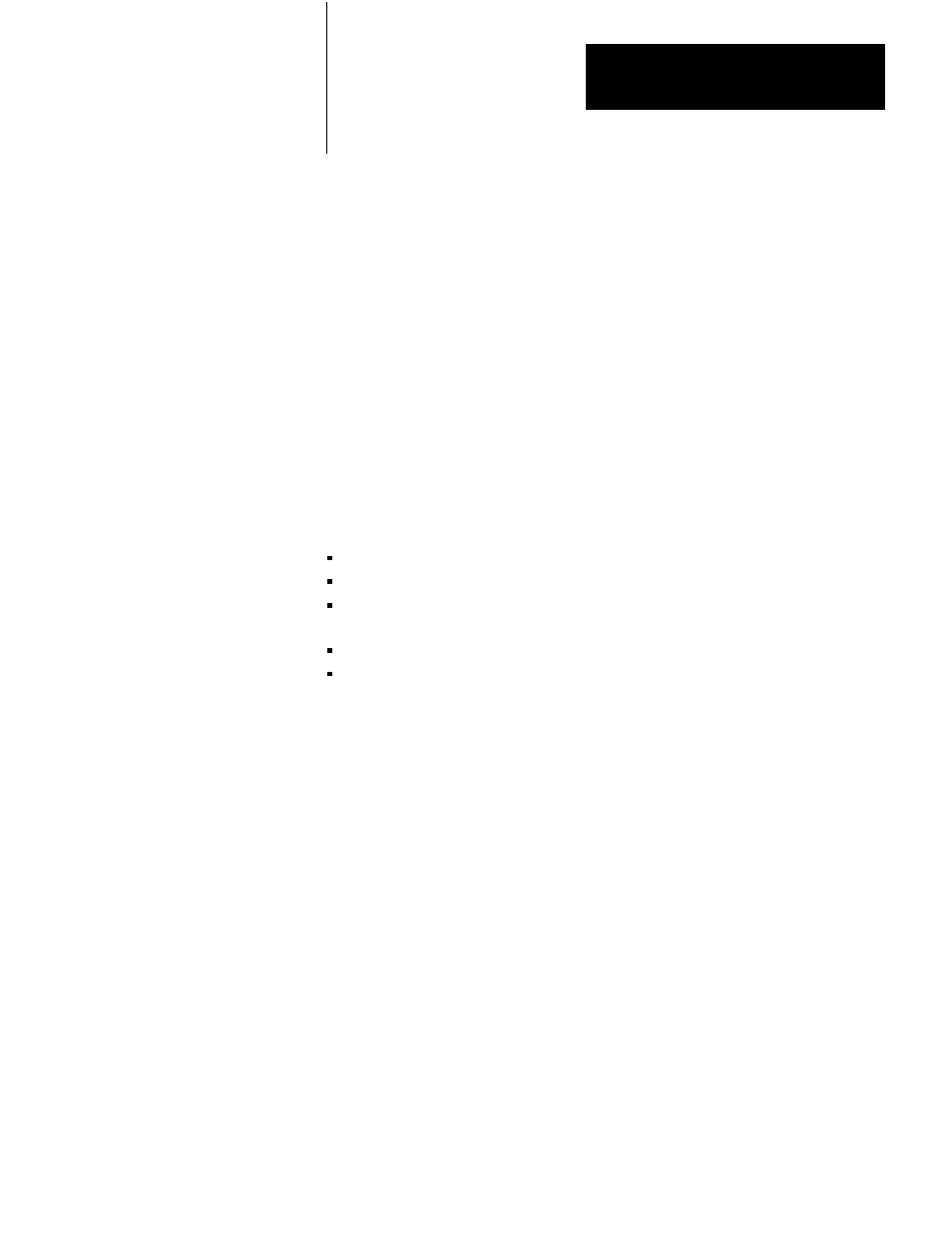
Programming
Chapter 3
3Ć51
The algorithm flow chart shows the selectable features of the PID
module’s control algorithms and indicates how selected features effect the
entire algorithm.
The algorithm flow chart can be used as a road map when programming
the PID module. Begin at the analog input. Select the needed features.
Record their word and bit values on copies of the worksheet found in
appendix A. When all needed features have been selected and the flow
chart has been followed to completion, the selections can be entered into
appropriate files in the PC processor. Data entry can be done after data
table addresses have been assigned to the data block and the ladder
diagram program has been entered into memory.
Prior to following the flow chart, there are five decisions concerning
module features which must be made. These decisions and their
corresponding control bits are not on the chart.
1-loop or 2-loop operation, W01 B15
standard or expanded features, W01 B14
4-digit BCD or 12-bit binary data format for most analog terms, W01
B12
4-digit BCD or 12-bit binary data format for the set point, W01 B11
soft fault response for each loop W38(W59) B15,14,13
The algorithm flow chart is shown in Figure 3.15. Sheet 1 shows,
callouts, abbreviations, and how to interpret the flow chart. See Appendix
E for an enlarged fold-out of the flow chart.
This section describes how the PID module is programmed. It also
describes how the status of the PID module can be continuously read by
the PC processor without performing read block transfers. Programming
techniques and strategies are explained in this section. Example
program/applications are presented in appendicies B and C. The
programming explanations pertain to the PLC-2/30 processor. Programs
can be modified for other processors capable of block transfer (refer to
chapter 1).
Algorithm Flow Chart
Block Transfer Programming