Operational overview – Rockwell Automation 1771-PD PID MODULE (+DU) User Manual
Page 45
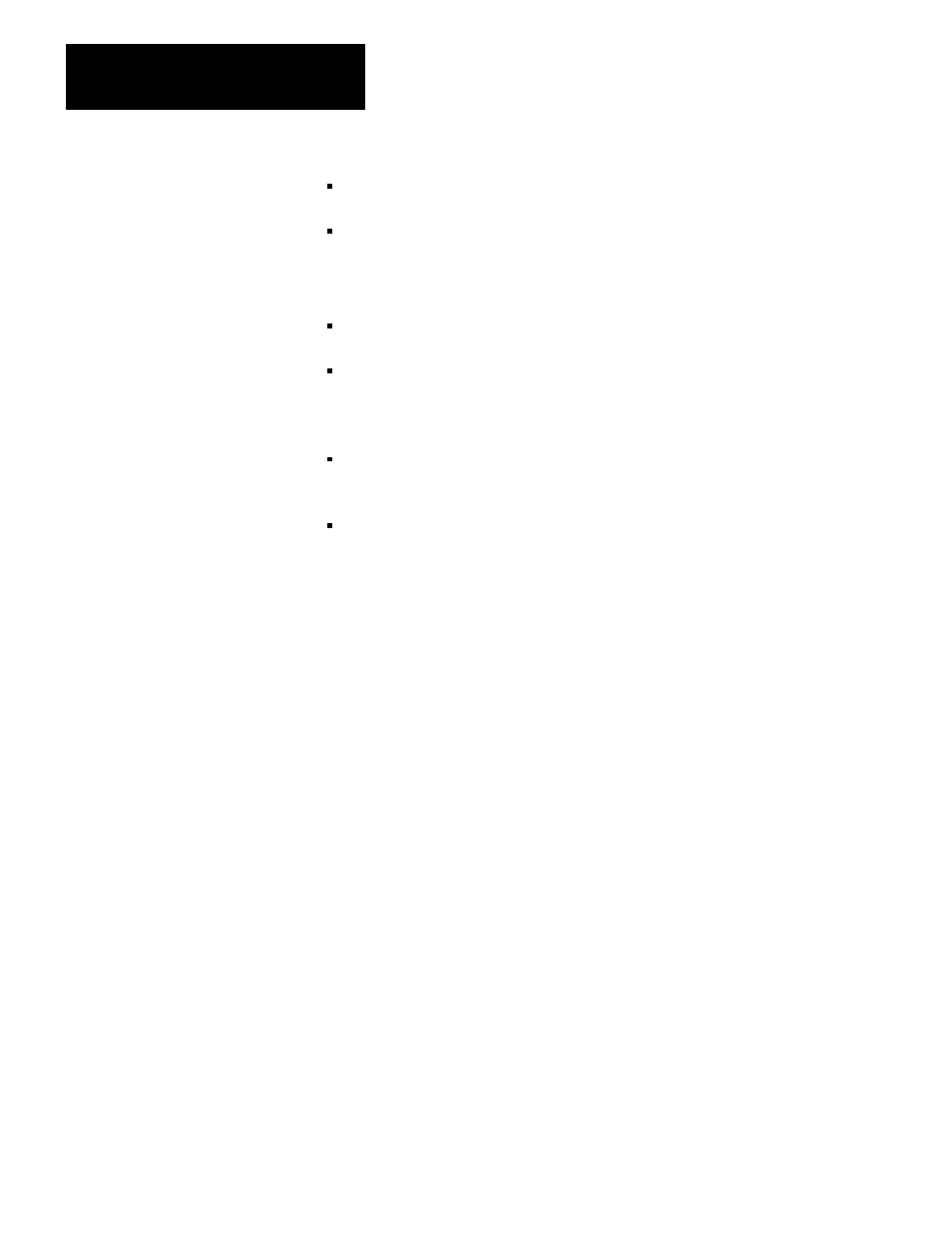
Programming
Chapter 3
3Ć2
Section titled Programming Consideration explains the application of
block transfer instructions.
Section titled Expanded Features describes the expanded features of the
PID module and how they can be applied.
Additionally, four appendices contain helpful programming information:
Appendix A contains the worksheets which are used to record data that
is entered into the PC processor and transferred to the PID module.
Appendix B describes a program that performs continuous block
transfers to the PID module. This program may be used when
continuous parameter adjustment or continuous reporting of module
status is required for a critical application.
Appendix C describes a program that performs periodic block transfers
to the PID module. This program may be used when less frequent
parameter adjustment is required.
Appendix D contains summary word and bit tables and a word/bit
reference.
The PID module is a closed loop process controller with proportional,
integral, and derivative control action. Control algorithm features are user
determined and loaded in the PID module by block transfer from the PC
processor. The PID module is equipped to control up to two process
control loops using its internal microprocessor. Because the features of
the two loops are similar, the description will be general to both loops
except where otherwise stated. Each loop is individually configured with
its own parameter values.
PID Algorithm
The PID module contains features which are user-selected to perform the
desired control. Figure 3.1 is a simplified diagram of the PID module
features. Basically, the PID module reads the process variable, compares
it to the set point, and adjusts the analog output to make the process
variable equal the set point. The process variable PV is the analog input
from the process. The setpoint SP is the equilibrium value of the process,
and the analog output is the control variable to the process. The
difference between the set point and the process variable is the error
signal, E=SP-PV.
The PID module can perform a combination of proportional, integral and
derivative control. Integral control is also known as reset action.
Derivative control is also known as rate action. The PID module can
perform relatively simple or very complex control based on selected
Operational Overview