Rockwell Automation 1771-QA Stepper Positioning Assembly User Manual User Manual
Page 64
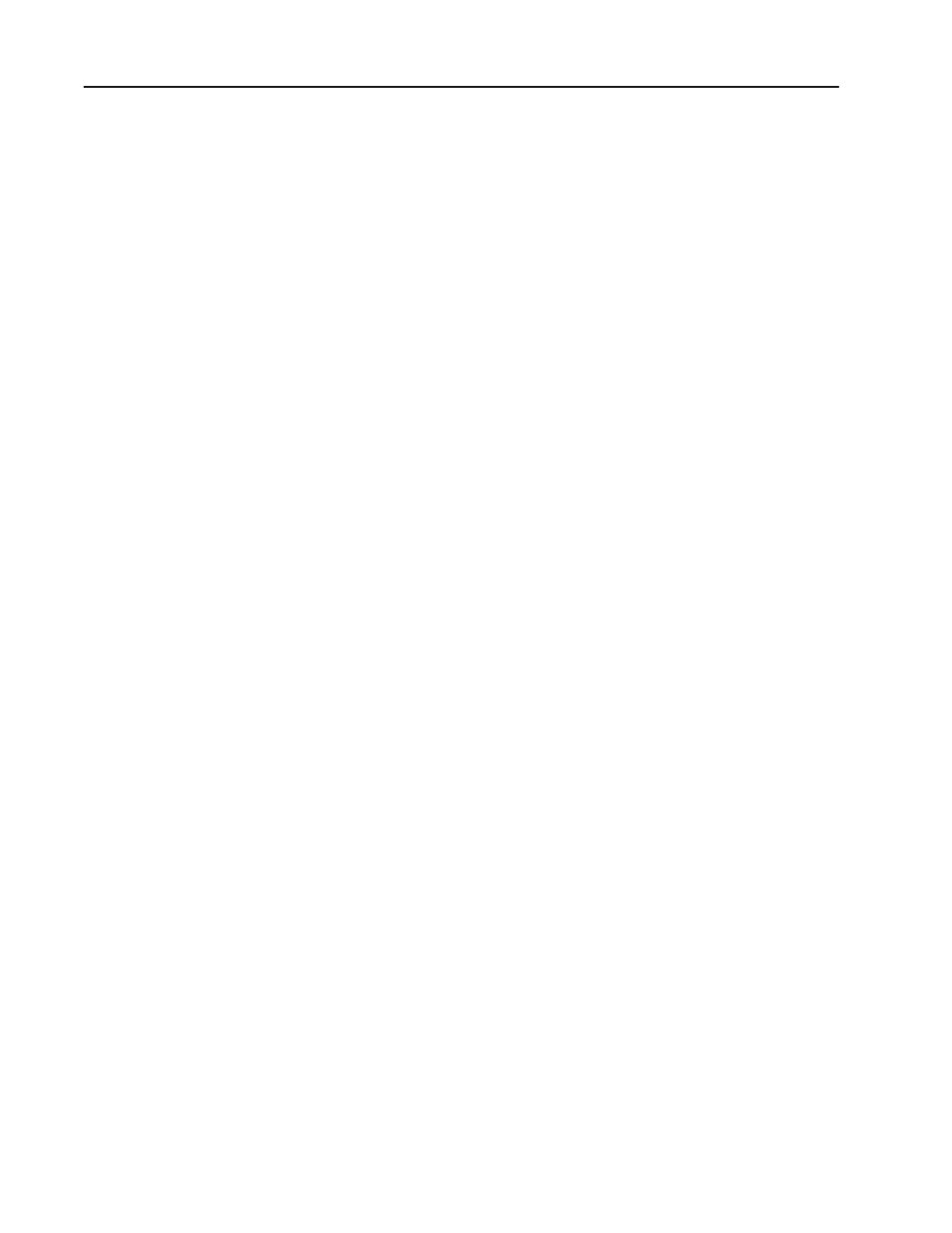
3–42
Programming and Operation
Publication 1771-UM002A–EN–P – May 2000
Processor Scan Time PS = (5ms/lK words) x (4K words) =
20ms.
Processor I/O Scan Time PIO = (0.5ms/rack number x (4
rack numbers) = 2ms
Number of Words Transferred = 64 (write) or 10 (read)
3. Calculate the block transfer times T for the write and read
operation.
T = 0.1 + (.075ms/word x 64 words)
= 0.1 + 4.8
= 4.9ms (write)
T = 0.1 + (.075ms/word x 10 words)
= 0.1 + .75
= .85ms (read)
4. Calculate the worst case system time ST between 2 consecutive
write block transfers.
The stepper controller module toggles to a read operation in the scan
following completion of the write operation.
ST = PS + PIO + T(1) + T(2) + T(3) + T(4) (writes)
PS + PIO + T(1) + T(2) + T(3) + T(4) (reads)
ST = 2PS + 2PIO + 4T (write) + 4T (read)
= 2(20) + 2(2) + 4(4.9) + 4(.85)
= 40 + 4 + 19.6 + 369
= 67 ms
This is the worst case time between two consecutive write block
transfers in the 4-chassis local configuration described in example
problem 2 (enabled stepper assembly in each chassis).
Mini-PLC-2/15 Controller
The program scan and I/O scan are consecutive and are considered as
a single processor scan. The Mini-PLC-2/15 scan time varies
typically from 18 to 24ms for a 1K program and one I/O rack. Each
block transfer module will be updated during a program scan.
The procedure for calculating the worst case time between transfers
can be done in three steps.
1. Write down the known facts and system values.
•
Processor Scan time PS = 24ms
•
Number of Words Transferred W default value of the module
2. Calculate the block transfer time T for the read and write
operation.