Rockwell Automation 1771-QA Stepper Positioning Assembly User Manual User Manual
Page 20
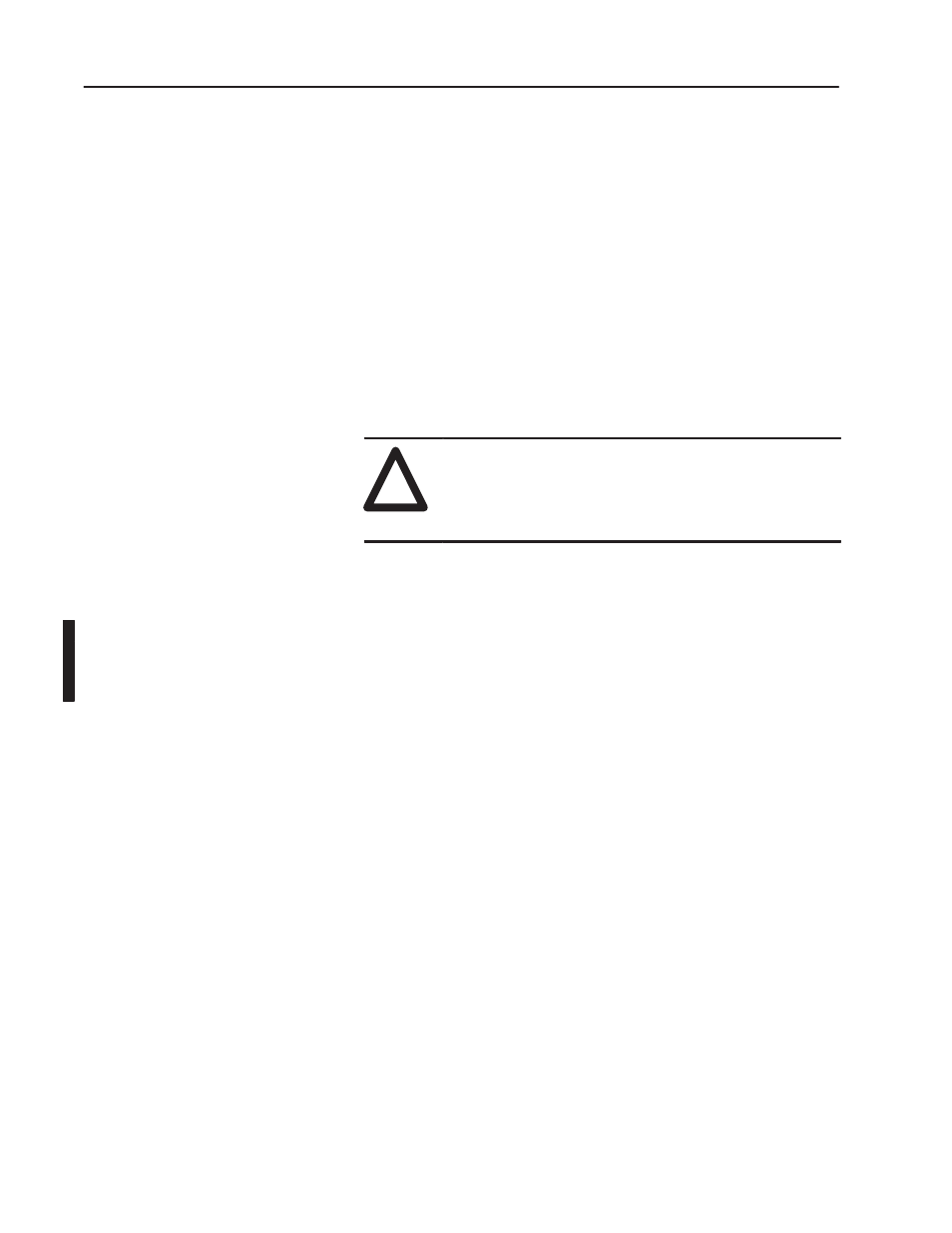
2–10
Assembly and Installation
Publication 1771-UM002A–EN–P – May 2000
System Grounding Considerations
The following should be connected to earth ground:
•
Ground prong of all AC line cords
•
Negative (-) or common terminal of the I/O power supply(ies)
•
One I/O chassis mounting stud
Ground the drain wire of the cable connecting the pulse output
expander module to the stepper translator. This cable should be
grounded either at the translator or at the I/O chassis, but not both.
See Shield Connection below.
The stepper translator, power supply and motor should be grounded
in accordance with the manufacturer’s instructions.
!
ATTENTION: Improper system grounding can result
in additional unwanted pulses occurring at the stepper
translator and/or stepper motor. Unpredictable
machine motion could occur with possible damage to
equipment and/or injury to personnel.
Cable Considerations
The stepper translator should be wired to the field wiring arm using a
twisted 3-conductor shielded cable (Belden 8771). The cable
distance between the pulse output expander module and the stepper
translator generally should not exceed 40 feet.
Shield Connection
Belden 8771 cable has a foil shield with a bare drain wire. The
shield should be connected to earth ground at one end of the cable
only. This can be at the customer end of the cable or at an I/O
chassis mounting bolt or stud. At the other end of the cable, the
shield should be cut short, bent back and taped to insulate it from any
electrical contact. This practice helps to guard against unwanted
radiated electrical noise and ground current loops.
Module Keying
Plastic keying bands shipped with each I/O chassis provide an easy
method for keying an I/O slot to accept only one type of module. Use
of the keying bands is strongly recommended.