Braking operation – Lenze 8400 protec Manual User Manual
Page 157
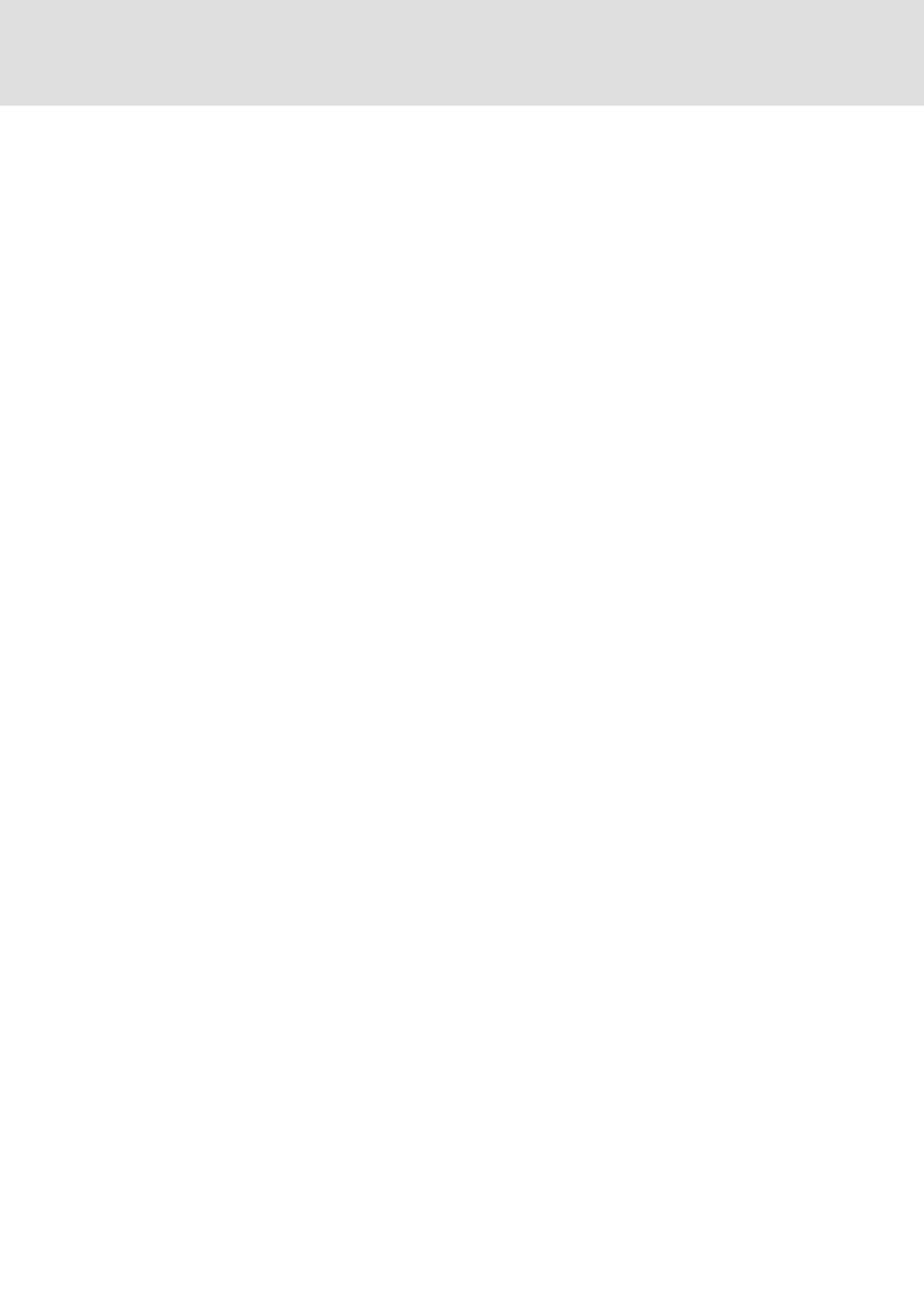
Braking operation
Operation with spring−applied brake
Introduction
l
157
EDS84DPS424 EN 5.0
Switching the brake
Switching of the brake can be controlled:
ƒ
Fast switch design
An external motor brake control module is required for the switching operations and
the DC supply of the spring−applied brake. The suitable motor brake control module
must be selected according to the rated data of the spring−applied brake.
The fast switch option also offers the possibility of a quick switch−off. Here, a relay
contact is controlled in the supply circuit of the coil via the controller.
Wiring: See motor connection for type Modular
ƒ
"Integrated brake rectifier" version
The voltage required for controlling the motor brake is generated in the controller,
dependent on the mains voltage value. The following motor brakes can be connected:
– to the 400−V mains: Coil voltage 180 V DC, max. 50 W
– to the 500−V mains: Coil voltage 225 V DC, max. 50 W
The rated coil voltage is neither increased nor reduced.
Wiring: See motor connection for type Q8/0
ƒ
"24 V DC" version
The voltage required for controlling the motor brake is supplied to the controller by an
external voltage source. The following motor brakes can be connected:
– Coil voltage 24 V DC
Wiring: See motor connection for type Q8/0
ƒ
Cold brake design
The voltage required for controlling the motor brake is generated in the controller
proportionally to the mains voltage value. The following motor brakes can be
connected:
– to the 400 V mains: coil voltage 180 V DC
– to the 500 V mains: coil voltage 225 V DC
To ensure a safe release of the brake, 130 % of the rated coil voltage is connected to the
coil for 0.3 s. Then, this voltage is reduced to 65 % of the rated coil voltage.
Wiring: See motor connection for type Q8/0
Optionally, the switching of the brake can be controlled in addition:
ƒ
Via an external control contact (e.g. PLC)
ƒ
Via a brake switch which is connected to one of the digital outputs of the controller.
The digital output must be parameterised accordingly.
The software manual provides further information on the parameterisation and
integrated brake management.