Enerpac ST-202 User Manual
Page 6
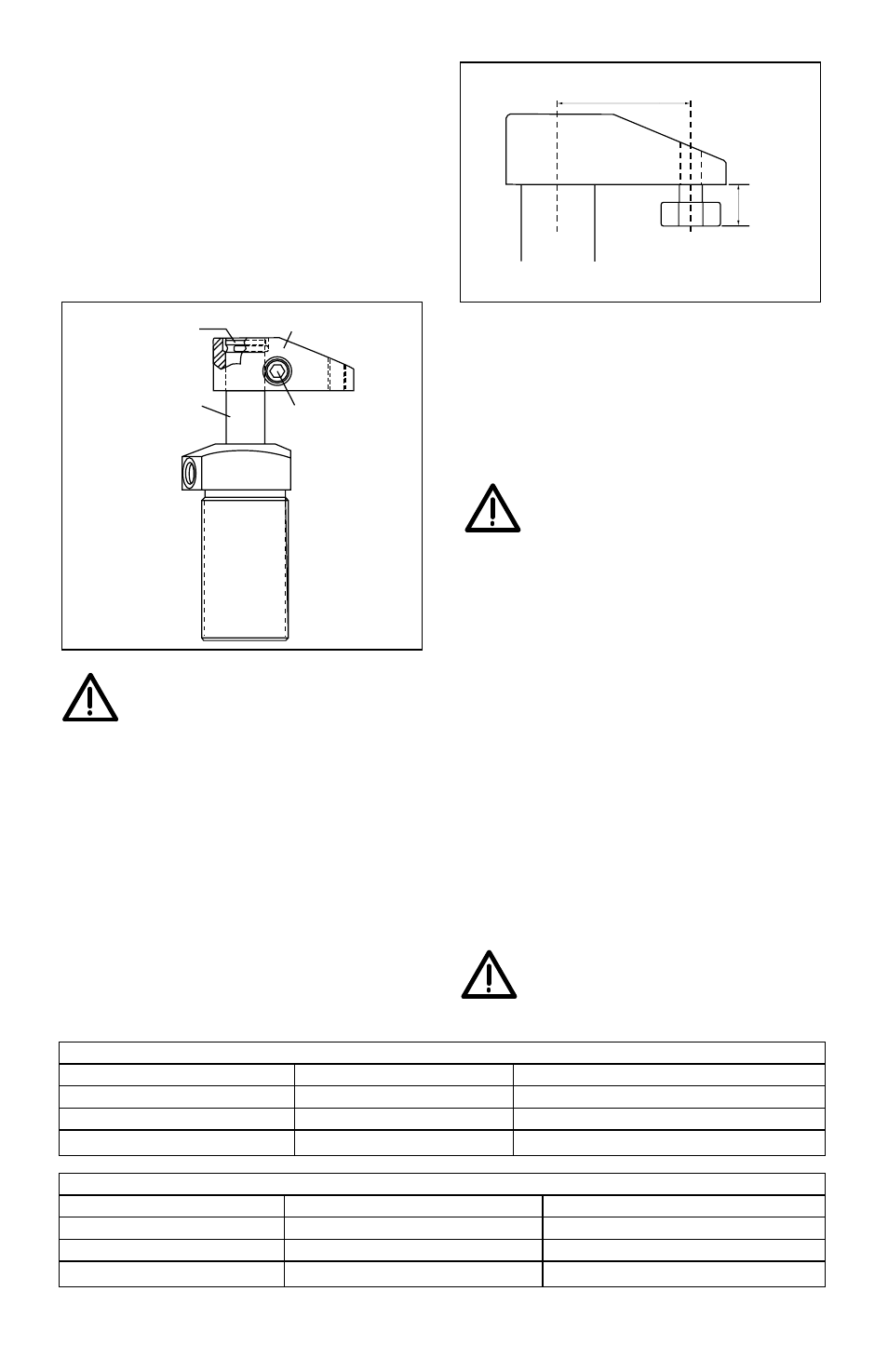
6.4 Attaching Clamp Arm
1. Remove the retaining ring from the top of the plunger.
2. Slide the clamp arm down over the plunger and use
a pliers to push the retaining ring back onto the
plunger groove. Orient the retaining ring so the
retaining ring gap will face the back of the clamp arm.
See illustration.
3. Move the clamp arm up until it is firmly against the
retaining ring and in the desired position. While
maintaining this position, torque the clamp arm bolt
to specification listed below.
CAUTION:
Inadequate torquing of the
clamp arm bolt could cause the arm to slip
during operation. BE SURE TO USE QUALITY
12.9 DIN 912 (GRADE 8) SOCKET HEAD CAP SCREWS
(supplied with standard clamp arms).
6.5 Arms for Upper Flange Body Style
To use the upper flange body style cylinders, you have to
be sure that the contact bolt head will clear the upper
flange during operation. The clamp arm must be long
enough for the bolt head to clear the upper flange as the
arm swings down. Clearance problems are most
common when using the CAS series standard length
arm, with the final clamping position at the side of the
cylinder. You may need to use the longer CAL Series
clamp arm for these applications. You can cut CAL series
arms to meet your own requirements, or make your own
custom arms according to the dimensions on page 8.
7.0 OPERATION
Swing cylinders rotate 90° during the first portion of
the stroke, continuing without rotation for the final
clamping stroke. The straight downward stroke is the
clamping stroke of the cylinder. Clamping force must
be applied only during the vertical travel, not during
the swing motion.
CAUTION:
— If clamping force is applied
during the rotation portion of the stroke,
internal plunger damage may result.
— To ensure maximum cylinder performance and
safety, be sure all hydraulic connections, hoses,
and fittings are properly sealed and fully
tightened.
— Be sure all items are rated to withstand system
pressures. Under-rated components will not
withstand higher pressure. Using under-rated
components will lead to equipment damage and
possible personal injury.
7.1 Turning Mechanism Protection
The kick-out turning mechanism protection is
designed to help prevent internal cylinder parts from
damage caused by obstructed plunger movement,
workpiece-clamp arm collision, and excessive oil
flow. If the kick-out mechanism activates, release
system pressure, check for the cause of the
activation and correct the problem. Return the
cylinder to its original position by hand or by using a
wrench.
CAUTION: After the kick-out mechanism
has been activated, always release the
hydraulic pressure in your system before
returning the mechanism to its original position.
6
Clamp Arm Bolt Torque
Cylinder Capacity
Bolt Type
Torque
9,0 kN (2024 lbs)
M10 x 1.25 x 35
81-95 Nm (60-70 ft-lbs)
18,8 kN (3900 lbs)
M12 x 1.25 x 40
95-108 Nm (70-80 ft-lbs)
35,0 kN (7600 lbs)
M16 x 1.50 x 55
217-244 Nm (160-180 ft-lbs)
Maximum Contact Bolt Length
Cylinder Capacity
Maximum Bolt Length
CAS Series Arm
9,0 kN (2024 lbs)
18 mm (0.71”)
L - 45 mm (1.77”)
18,8 kN (3900 lbs)
22 mm (0.875”)
L - 55 mm (2.17”)
35,0 kN (7600 lbs)
24 mm (1.00”)
L - 68 mm (2.68”)
Retaining ring
Clamping arm
(Opening toward
back of clamp arm)
Plunger
Clamp arm bolt
L
Contact bolt
(with head dia.
larger than 16mm [.63])
Max.
length