8 programming and debugging the dvc5/7/10, Programming and debugging the dvc5/7/10 – High Country Tek DVC80 User Manual
Page 16
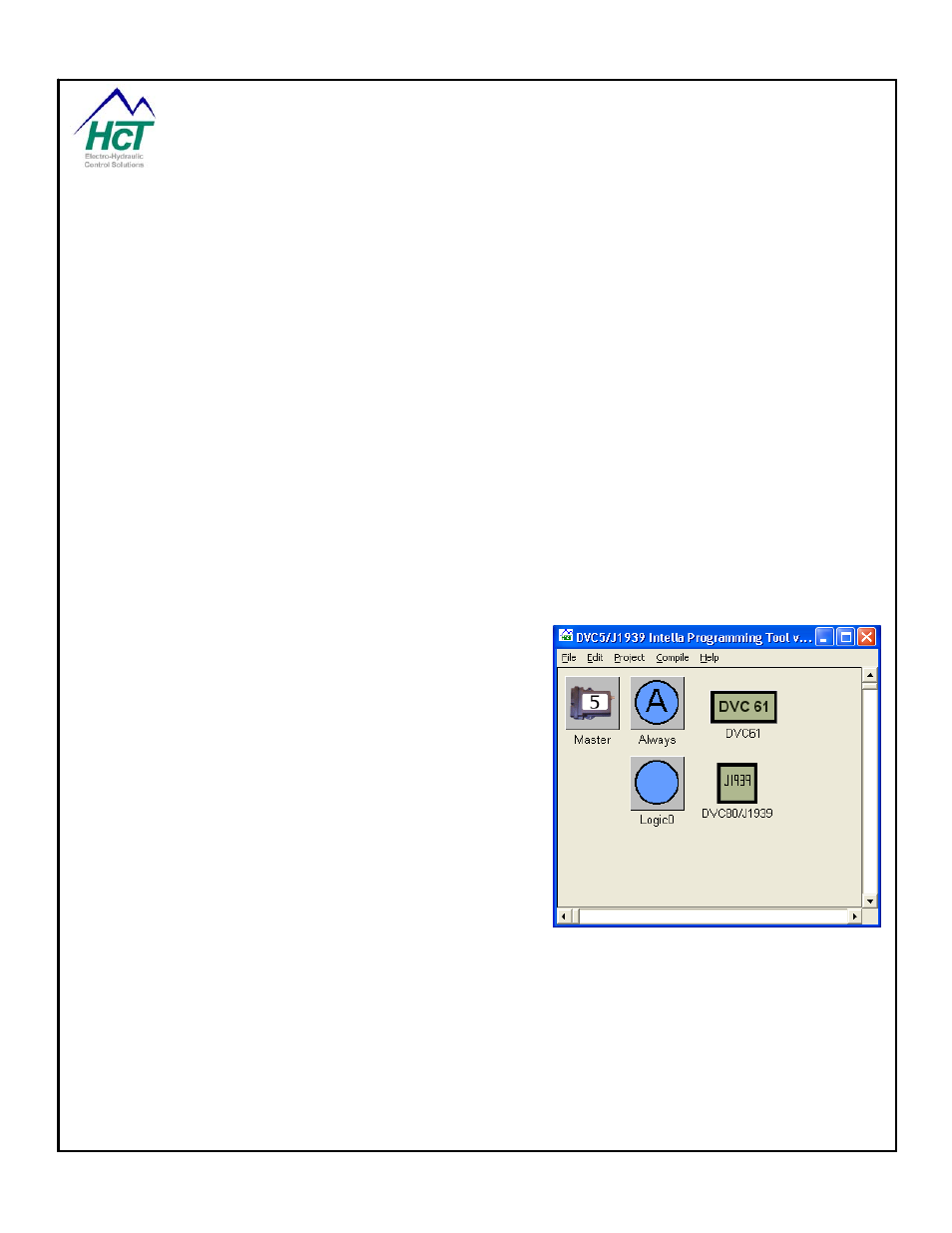
P/N: 021-00154, Rev. A.6 - updated for V4.7 Tools
Page | 16
to fast can cause over correction (i.e. overshoot) depending on the latency experienced by the feedback signal
changing given the adjustment. Most systems require the P and I terms to be tuned based on how your system
behaves.
It should be noted that when you desire a valve’s current to be set to 1 ampere for instance from 0 amperes the
PID system works as if the error at time zero is 1 ampere and the adjustment mechanism then sets the actual
PWM% to begin to correct the error. By plotting a particular PWM variable using the Program Loader Monitor’s
graph facility you can see how the correction is accomplished as a function of time for tuning purposes.
The DVC5/7/10 controllers provide for 3 distinct and different closed loop control mechanisms. They are:
1. Automatic proportional valve current regulation
2. Software controlled closed loop proportional valve current based on a sensor’s feedback signal indicating
pressure, position, temperature or RPM.
3. Software only closed loop control used typically for long latency systems.
In the first case, the PID technique is employed by the DVC hardware and BIOS to set and maintain the valve
coil current to the desired value.
In the second case, your application software calculates the feedback value and the set point and the DVC
hardware and BIOS adjusts the valve current (PWM %) based on the difference between the
setpoint (or target) and the calculated feedback.
In the third case, you control the PWM % setting through a repeatedly executed piece of software that reads
sensor input and does its own form of a PID adjustment.
1.8
Programming and Debugging the DVC5/7/10
The Windows PC based DVC5/7/10 Programming Tool gives
you the ability to program the DVC modules to work in a
variety of applications without large development costs.
Some knowledge of Windows, computer programming
and electro-hydraulics is beneficial.
The Programming Tool's main screen shown here is called
the Project screen. Every project consists of components. A
component can be a physical DVC5/7/10 module and a
number of DVC expansion modules. Additionally, software
components such as the Always code icon wherein you
program critical system functions and several logic sequence
icons wherein you program the normal operations of your
system. At a minimum, a DVC5/7/10 (Master) module and an
“Always” bubble icon must be defined. As your system grows
you add additional physical and programming components by right clicking your mouse on the Project screen
and selecting the component type you wish to add. Once selected from the pop menu, the component will be
added to the project as another icon. As a result, the Project screen contains all of the components, in the form
of movable icons, for the creation of your system application. Double clicking a component icon will allow you to
program or configure it. The next section lists the component types.
Note: If you wish to have another DVC5/7/10 module be the master controller of a portion of your system them
another Project needs to be created wherein that DVC5/7/10 and the components it controls are programmed.
Adding a DVC5/7/10 to DVC5/7/10 module to each project and configuring the messages to be sent back and
forth can enable communication between multiple DVC5/7/10 projects.