3 self-tuning 43, 1 preparation for self-tuning 43, 2 self-tuning sequence 43 – West Control Solutions KS 45 User Manual
Page 43
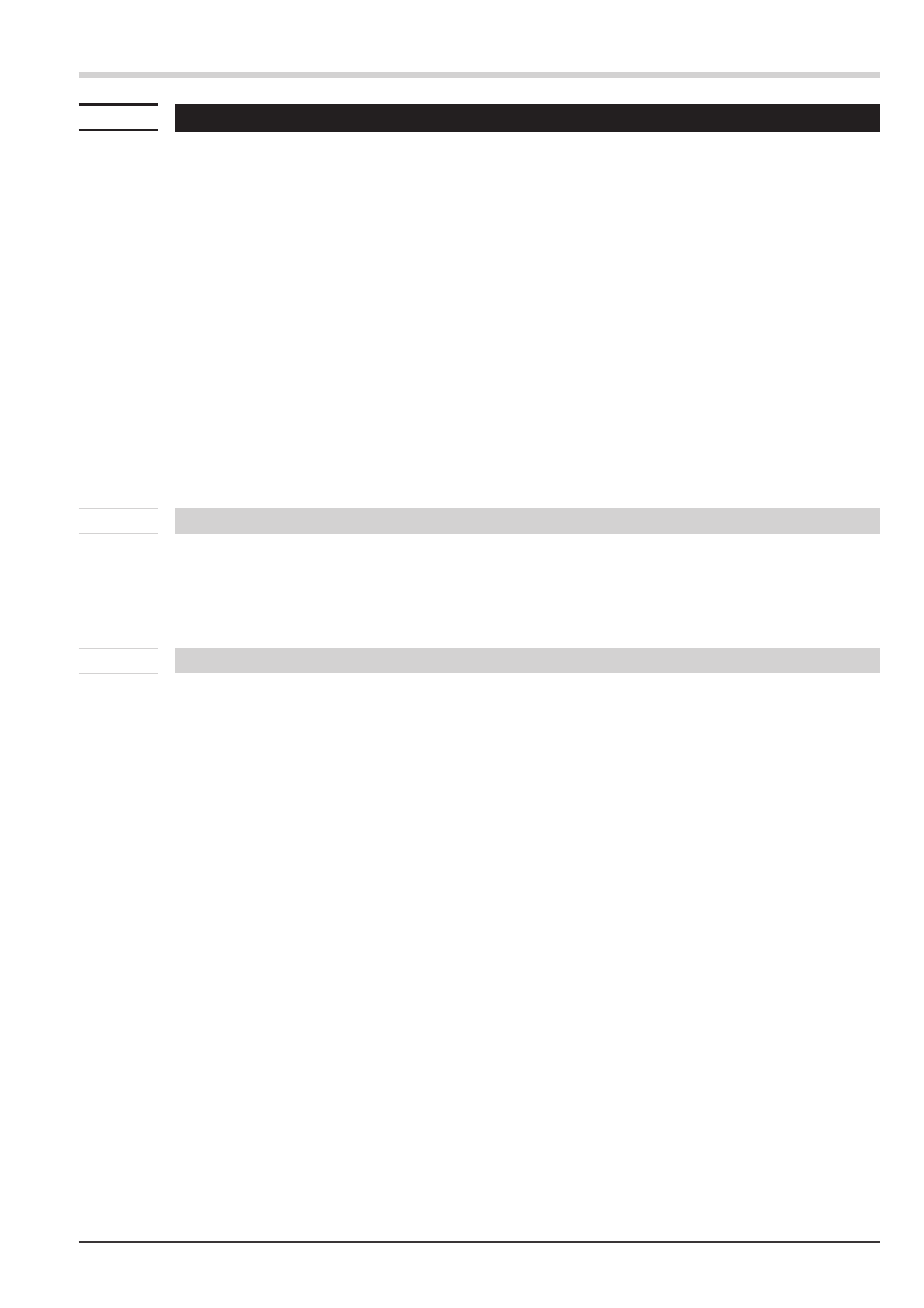
7.3
Self-tuning
For determination of optimum process parameters, self-tuning is possible.
After starting by the operator, the controller makes an adaptation attempt, whereby the process characteristics are
used to calculate the parameters for fast line-out to the setpoint without overshoot.
The following parameters are optimized when self-tuning:
Pb1 - Proportional band 1 (heating) in engineering units [e.g. °C]
ti1 - Integral time 1 (heating) in [s]
r only, unless set to OFF
td1 - Derivative time 1 (heating) in [s] r only, unless set to OFF
t1 - Minimum cycle time 1 (heating) in [s] r only, unless Adt0 was set to
“no self-tuning” during configuration by means of BlueControl
®.
Pb2 - Proportional band 2 (cooling) in engineering units [e.g. °C]
ti2 - Integral time 2 (cooling) in [s] r only, unless set to OFF
td2 - Derivative time 2 (cooling) in [s] r only, unless set to OFF
t2 - Minimum cycle time 2 (cooling) in [s] r only, unless Adt0 was set to
“no self-tuning” during configuration by means of BlueControl
®
7.3.1
Preparation for self-tuning
•
Adjust the controller measuring range as control range limits. Set values
rnG.L and rnG.H to the
limits of subsequent control. (Configuration
rControllerrlower and upper control range limits)
ConFrCntrr rnG.L and rnG.H
•
Determine which parameter set shall be optimized (see tables above).
7.3.2
Self-tuning sequence
The controller outputs 0% correcting variable or
Y.Lo and waits, until the process is at rest (see start-conditions
below).
Subsequently, a correcting variable step change to 100% is output.
The controller attempts to calculate the optimum control parameters from the process response. If this is done
successfully, the optimized parameters are taken over and used for line-out to the setpoint .
With a 3-point controller, this is followed by “cooling”.
After completing the 1st step as described, a correcting variable of -100% (100% cooling energy) is output from the
setpoint.
After successfull determination of the “cooling parameters”, line-out to the setpoint is using the optimized parameters.
Start condition:
w
Rest condition
For process evaluation, a stable condition is required. Therefore, the controller waits until the process has
reached a stable condition after self-tuning start. The rest condition is considered being reached, when the
process value oscillation is smaller than
± 0,5% of (rnG.H - rnG.L).
w
setpoint reserve
After having come to rest with 0% correcting variable or with
Y.Lo, the controller requires a sufficient
setpoint reserve for its self-tuning attempt, in order to avoid overshoot.
w
Sufficient setpoint reserve: SP.Hi - SP.LO) direct controller: (with process value >setpoint+ (10% of SP.Hi - SP.LO) Controlling KS 45 43 Self-tuning
inverse controller:(with process value