Operator's manual – Teledyne LeCroy CANbus TD and CANbus TDM - Operators Manual User Manual
Page 63
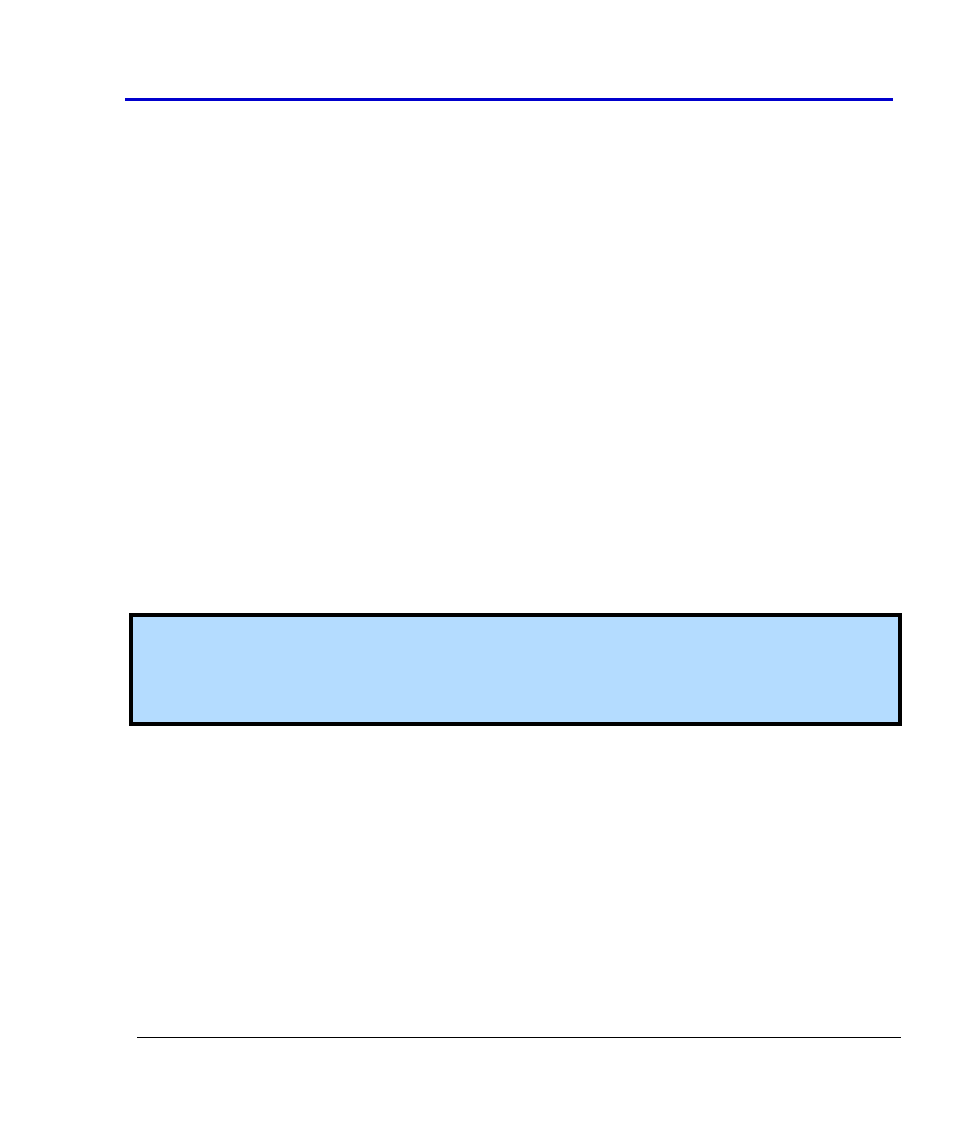
Operator's Manual
CANbus-TD-TDM-OM-E RevB
63
actually be anywhere from 61% to 69%), the CAN controller converts the physical layer signal
into protocol layer data. It is this protocol layer data that the Trigger Module is matching to the
downloaded trigger condition in order to determine whether to output a trigger pulse.
The USB2.0 Cable provides power to the Trigger Module. It also permits downloading of trigger
conditions from the instrument to the Trigger Module.
The Oscilloscope Interface Module (OIM) contains intelligence to identify the Trigger Module to
the instrument, and transmits the trigger edge to the instrument input. As part of its
“identification” function, the OIM does the following when it is plugged into a channel or the
EXT input on the instrument:
Automatically sets the instrument trigger to a negative-going Edge and a 3 V trigger level.
The trigger source is also automatically set to the channel or Ext input that the OIM is
connected to.
Automatically opens the instrument main dialog, so that it is quick and easy to set up the
CAN trigger.
Automatically applies a deskew (time shift of the signal) of 31 microseconds to any
channel that the OIM is not connected to. This makes it easy to time correlate CAN
signals with other analog signals, and sets the instrument trigger point indicator to the
End of Frame (EOF) of the CAN message that is being triggered on. When the OIM is
disconnected, the deskew is set back to zero seconds.
Reads attributes of the Trigger Module, such as the types of installed Trigger Couplers.
Note: The Trigger Module only provides triggering capability. In order to “view” the actual CAN
physical layer signal on the instrument display, you must also probe the CANH and CANL
signals with the single-ended probes, or a differential probe (such as the LeCroy ADP305 or
AP033) and input the probe signals to an instrument channel.