Trigger setup, Canbus trigger, decode, and measure – Teledyne LeCroy CANbus TD and CANbus TDM - Operators Manual User Manual
Page 62
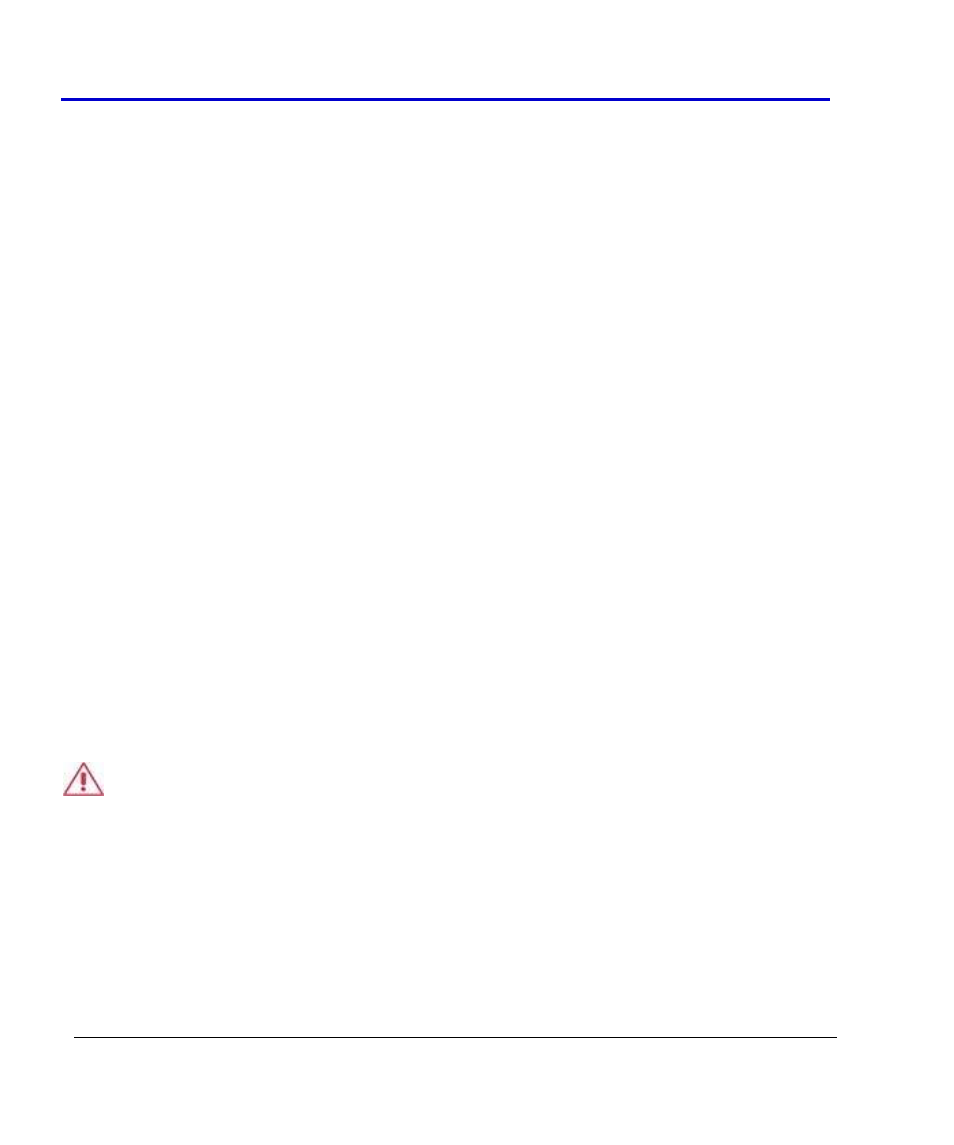
CANbus Trigger, Decode, and Measure
62
CANbus-TD-TDM-OM-E RevB
B
ASIC
I
NSTRUMENT
O
PERATION
For information on setting up the instrument to view CAN (or other) signals, reference your
instrument's on-line help system.
Trigger Setup
Overview
The instrument has a very powerful and flexible CAN trigger that is extremely easy to set up for
triggering, using a DBC file and the CAN Symbolic Trigger setup. In addition, Hexadecimal setup
is provided. Connecting the CANbus TD/TDM Series trigger hardware to your circuit is described
in the preceding chapters.
Some basic knowledge of CAN physical bus connections is helpful in order to ensure that you
can connect the trigger correctly. Proper care must be taken to ensure that CANH, CANL, GND,
etc. are connected and terminated correctly (just like any other node on the CAN Bus), or else
you may load the bus, fail to trigger, or generate error frames on the bus. Following the few
simple rules described previously should ensure success.
Trigger Hardware
The CANbus TD/TDM Series Trigger Module operates as a “node” on the CAN Bus. It contains a
Microcontroller, two CAN controllers, and up to two Transceivers (Trigger Couplers) that
interface to the CAN circuit just like any other node on the CAN bus. A trigger condition, set
from within the instrument, is downloaded to the Trigger Module, and the CAN controller within
the Trigger Module “filters” on the condition. When the trigger condition is met, the Trigger
Module outputs a pulse on Pin 2 of the three pin connector that connects to the Oscilloscope
Interface Module (OIM). This pulse occurs 31 microseconds after the trigger condition is met
(+/-1/8 bit time due to normal CAN controller operation). The pulse has a 5 V normal level, with
a minimum level of 0 V and decay back to 5 V. The Oscilloscope or Vehicle Bus Analyzer actually
triggers on this physical signal edge and not on the protocol CAN message.
CAUTION
The Trigger Module can contain enough circuitry for two complete nodes. Even though this
would theoretically provide the capability to both simulate and trigger on signals
simultaneously, this is not recommended. The processor could get overloaded if asked to both
simulate and trigger, and the result could be missed trigger conditions.
Like any other CAN node, the Trigger Module converts physical layer signal data into protocol
data. The trigger condition is downloaded to the Trigger Module in a protocol data format, with
the CAN transceiver (Trigger Coupler) interfacing to the CAN controller in the Trigger Module.
Using a sample point of approximately 65% (depending on the bit rate, the sampling rate could