2 communication connection guidelines – Micromod MOD: 30ML Installation User Manual
Page 83
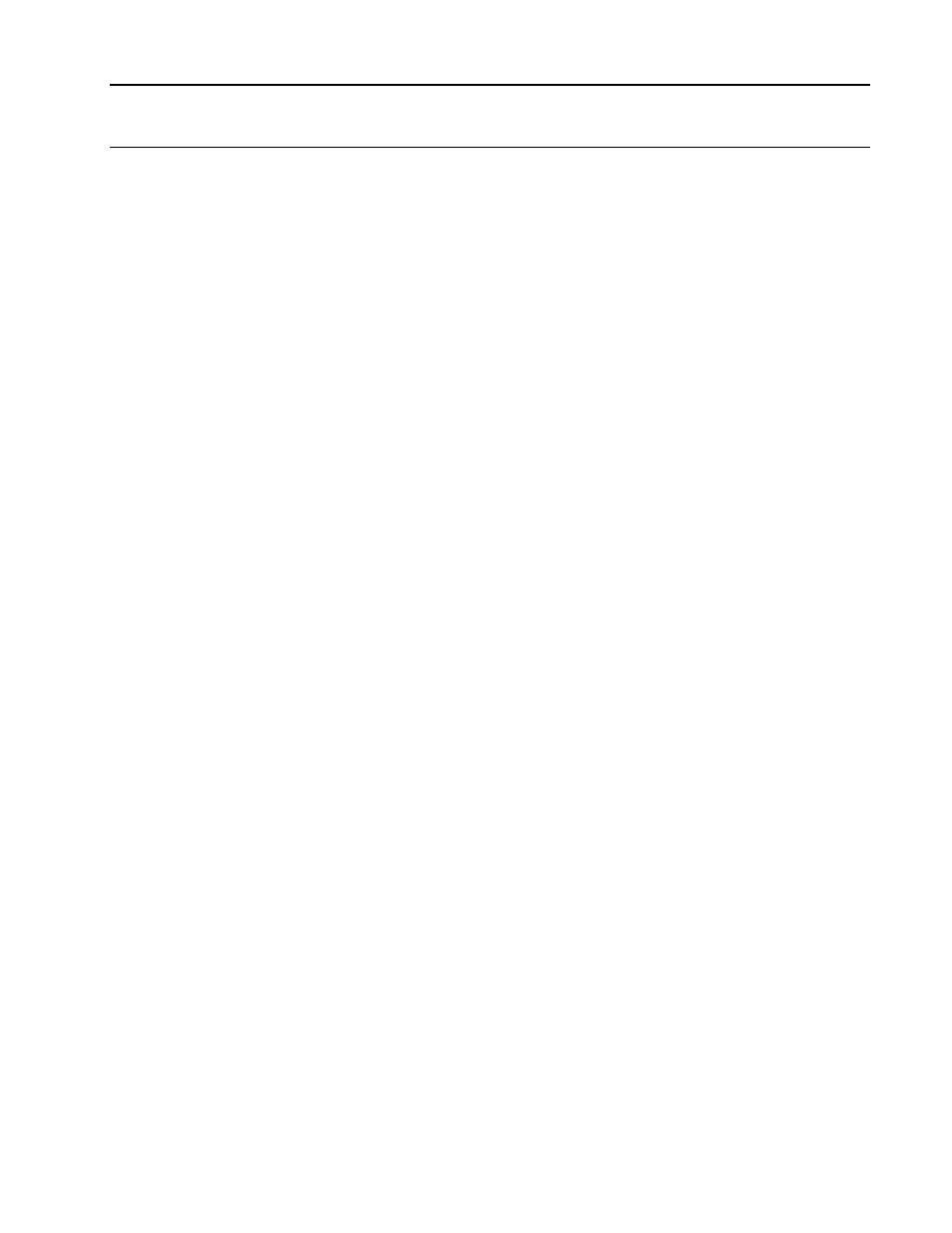
MOD 30ML Multiloop Controller
COMMUNICATIONS CONNECTIONS
5.2
COMMUNICATION CONNECTION GUIDELINES
The wiring connections described in this section are made with the controller installed in its
operating location and with the power off. All connection terminals are located under a cover
on the back of the Model A & B instrument housing. Model C instruments do not have a
cover over the terminals. Figure 5-1b shows the Model A & B communication connection
terminals with the cover removed.
The recommended procedure for making communications connections is as follows:
1. Communications port 1 serves either the built-in communications circuits or I/O module
location S10 (S10 and S9 if module is double wide). It is recommended that the built-in
communication circuit be used for port 1. This leaves the module locations available for
other purposes.
2. Communications port 2 serves I/O module location S8 (S8 and S7 if module is double
wide). If required, a second communication network can be supported via this modular
connection.
3. When using communication port 1, a communications jumper on the carrier board, Figure
5-2, must be positioned to select the communication type for the built-in circuits, or to
deselect the built-in circuit if a module is used.
4. The built-in communications circuits are isolated from all other circuits. Terminal 1 (TX &
RX common) is the communications circuit common for these built in circuits. When built-
in communication is used, connect terminal 1 of each instrument on the communication
bus together. This common line must be connected to ground at some point in the
system to prevent the possible build up of a static charge, reduce noise pick up, and
comply with EU EMC requirements.
5. Communications wiring should be shielded twisted pairs. Detailed cable requirements
are provided in Sections 5.4 and 5.5.
6. The cable shields must be connected to a good noise free ground. Normally this should
be one of the terminals identified as chassis in Figure 3-1. Alternatively, it is acceptable
to use the shield to connect the commons among the instruments. If this arrangement is
used, noise rejection may not be optimal.
7. Route communications wiring from the top left hand side of the housing and distribute to
appropriate terminals.
8. Use a small, flat-head screwdriver to loosen appropriate connection screws and clamps
on terminal blocks.
9. Strip approximately 5/16 inch (8 mm) of insulation from the end of each wire, insert wires
at assigned terminals, and secure terminal screws and clamps.
10. Make wiring connections using the following procedures:
a. Front Panel RS-232 Communications Connections - Section 5.3.
b. Instrument Communications Network (ICN) Connections - Section 5.4.
c. Modbus Network Connections - Section 5.5.
11. After all connections are completed and checked, the ac power wiring can be connected
at the distribution panel (ac source).
* NOTE:
Before putting the controller into operation, it must be configured using
either the front panel keys or the PC Configuration Software. See
Section 1.1.2 for related documents.
77