Magnum Venus Plastech Megaject RTM Pro Revison 7_0 User Manual
Page 62
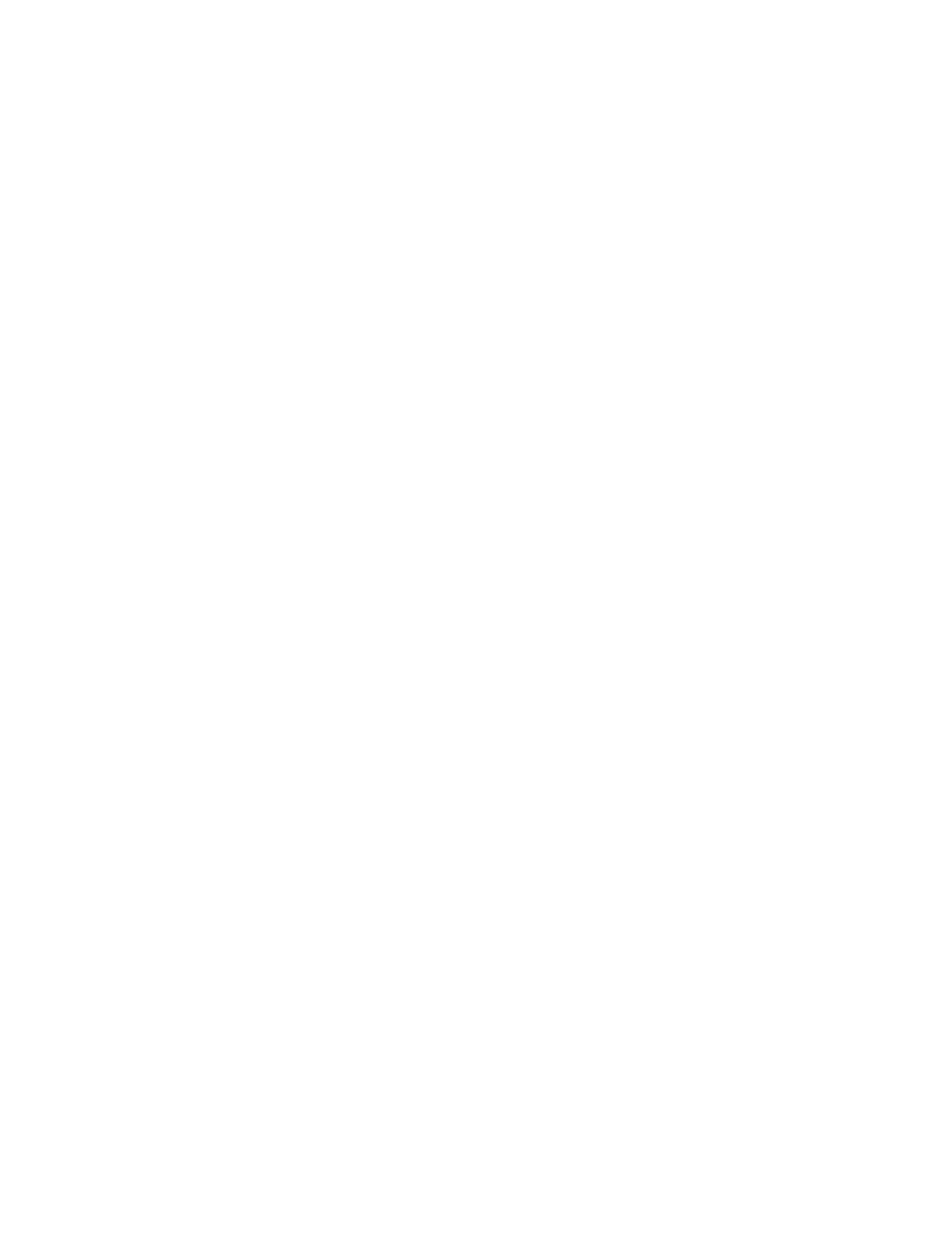
Megaject RTM Pro Manual – Revision 7.00 – 13
th
APRIL 2006
Other signal fault conditions can be first traced by checking for correct inputs signal
conditions during machine activity.
7.3. Common Problems – Non-electrical
This section describes a series of problems that have been encountered while using the
Megaject RTM Pro, and suggests possible solutions.
1. Machine will not inject, when all sensors are correct.
Possible causes:
a. Injection pressure incorrectly set
b. Gelled resin in static mixer or Resin valve head inlet
c. Autosprue blockage
d. Resin pump top seal dry and un-maintained
2. Autosprue is blocked.
Possible causes:
a. Insufficient air pressure available for efficient flushing
b. Autosprue feed and or drain pipe too long or restricted
c. High resin filler loading prevents efficient single flush cleaning.
3. Machine pumps run unexpectedly slowly.
Possible causes:
a. Resin injection pressure set too low
b. Pump Power (%) set too low
c. Excessive use of recirculation has led to ice build up on air motor and caused air
starvation to motor
4. Poor catalysation resulting in wet patches in part.
Possible causes:
a. Catalyst system not primed sufficiently
b. External head non return valve O ring not seating due to dirt or worn seal
c. Catalyst system “gassing” in system
d. Worn piston seal in catalyst pump
6. Small air bubbles in resin mix.
Possible causes:
a. Loose or poor sealing on pump inlet pipes or fittings
7. Short volume resin mix from head.
Possible causes:
a. Resin filter requires cleaning
b. Resin filler loading too high or mix flow rate set too high for viscosity of mix.
c. Worn piston seal in resin pump.
d. Machine incorrectly calibrated.
NOTE: If the pumps do not run when signalled to do so, and all the checks made
above have been carried out, one final check can be made to observe what pressure is
being fed to the air motor which drives pumps. At the top and bottom of the main air
cylinder in bay 2, a quick fit chrome connector can be located. This accepts a pressure
gauge supplied with the machine. The pressure gauge is used in these circumstances