Commissioning – Magnum Venus Plastech Megaject RTM Pro Revison 7_0 User Manual
Page 10
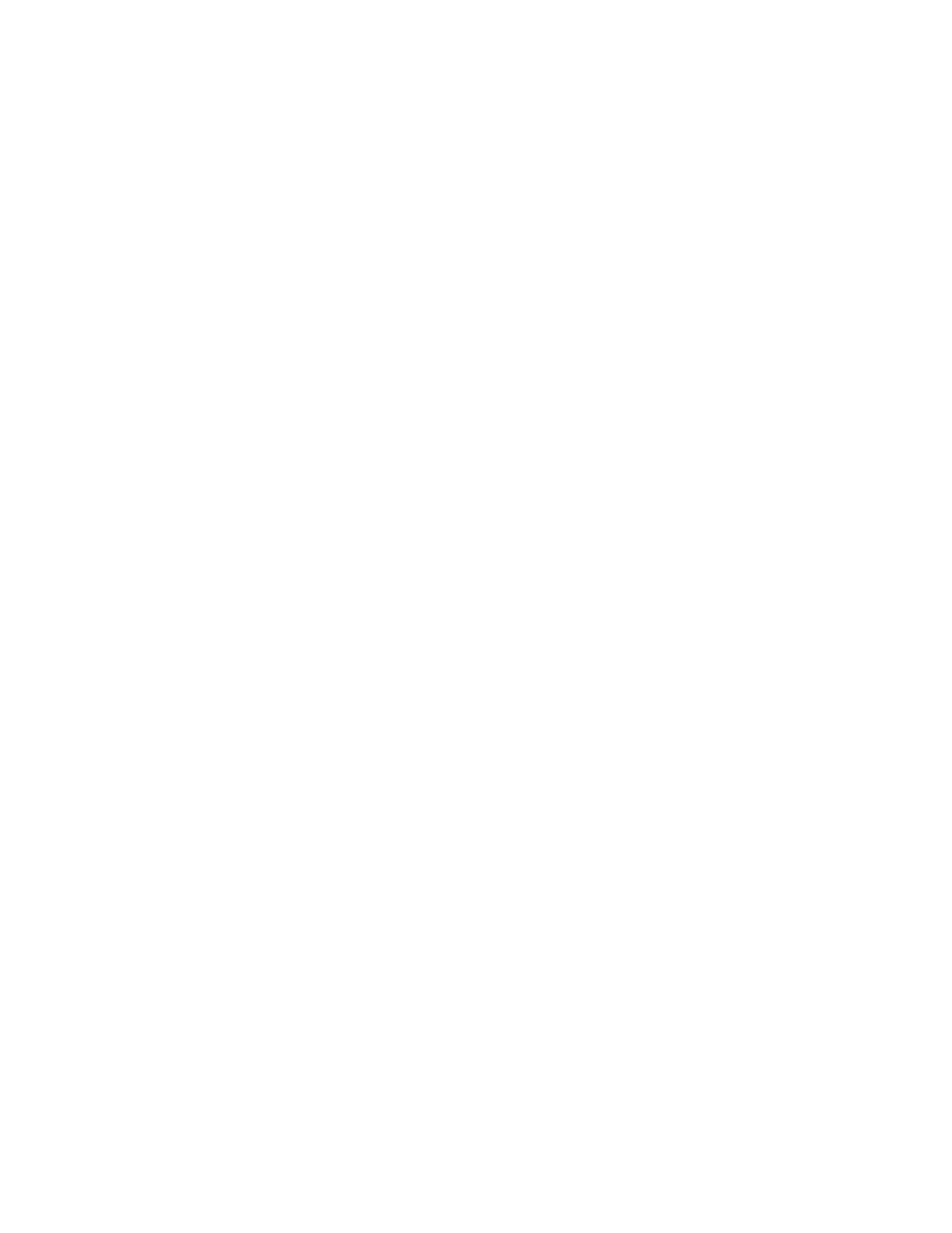
Megaject RTM Pro Manual – Revision 7.00 – 13
th
APRIL 2006
2. Commissioning
CAUTION
Overalls and eye protection must be worn at all times during operation of the
machine. Suitable gloves must be worn when carrying out operations which may
result in contact with fluids.
The Megaject RTM Pro is tested and secured against leaks prior to dispatch. It is
essential that all pipes and fittings remain tight and sealed at all times to prevent
air ingress into or leakage from the system.
2.1. Connecting to services
Air and electrical connections must be made by a suitably qualified person.
2.1.1. Electrical Supply
The machine should be connected to either a 110VAC 60Hz or 220VAC 50Hz
0.8kVA single phase supply, depending on the voltage specified on the machine. This
machine must be correctly earthed.
2.1.2. Air Supply
The supply must be dry filtered clean air. A lubricator must NOT be used in the air
supply to the machine. When the machine is powered up and the safety circuit has
been reset, the regulator in bay 2 should be set to approximately 6 bar. This value can
also be read on the touch screen human machine interface (HMI) in the VALUES
screen.
Connection of the air supply should be made to the fitting on the side of bay 1. Supply
pressure should be between 6 - 9 bar and capable of supplying a flow of between 350
l/min to 1200 l/min for maximum injection flow rate.
2.2. Loading materials
Resin Pump Lubricant (Bay 2)
Half fill resin pump upper collar (item 0546) with Plastech Pump Lubricant (supplied)
to maintain pump shaft and top seal in a clean and lubricated condition.
Acetone (Bay 3 – Rear of Machine – White polypropylene tank)
NOTE: Solvents are flammable; follow all applicable health and safety
regulations when using solvents.
Remove small white filler cap from solvent tank. Fill tank to approximately 4/5 full.
Solvent level must always be high enough to cover the top of the internal pump
chamber inside the tank. Replace cap.
Sufficient solvent levels are essential for the correct flushing of the machine. The
solvent level must not be allowed to fall below 5 litres as this may cause inefficient
flushing. Level is monitored by a non-intrusive proximity level sensor.