Magnum Venus Plastech Megaject RTM Pro Revison 7_0 User Manual
Page 47
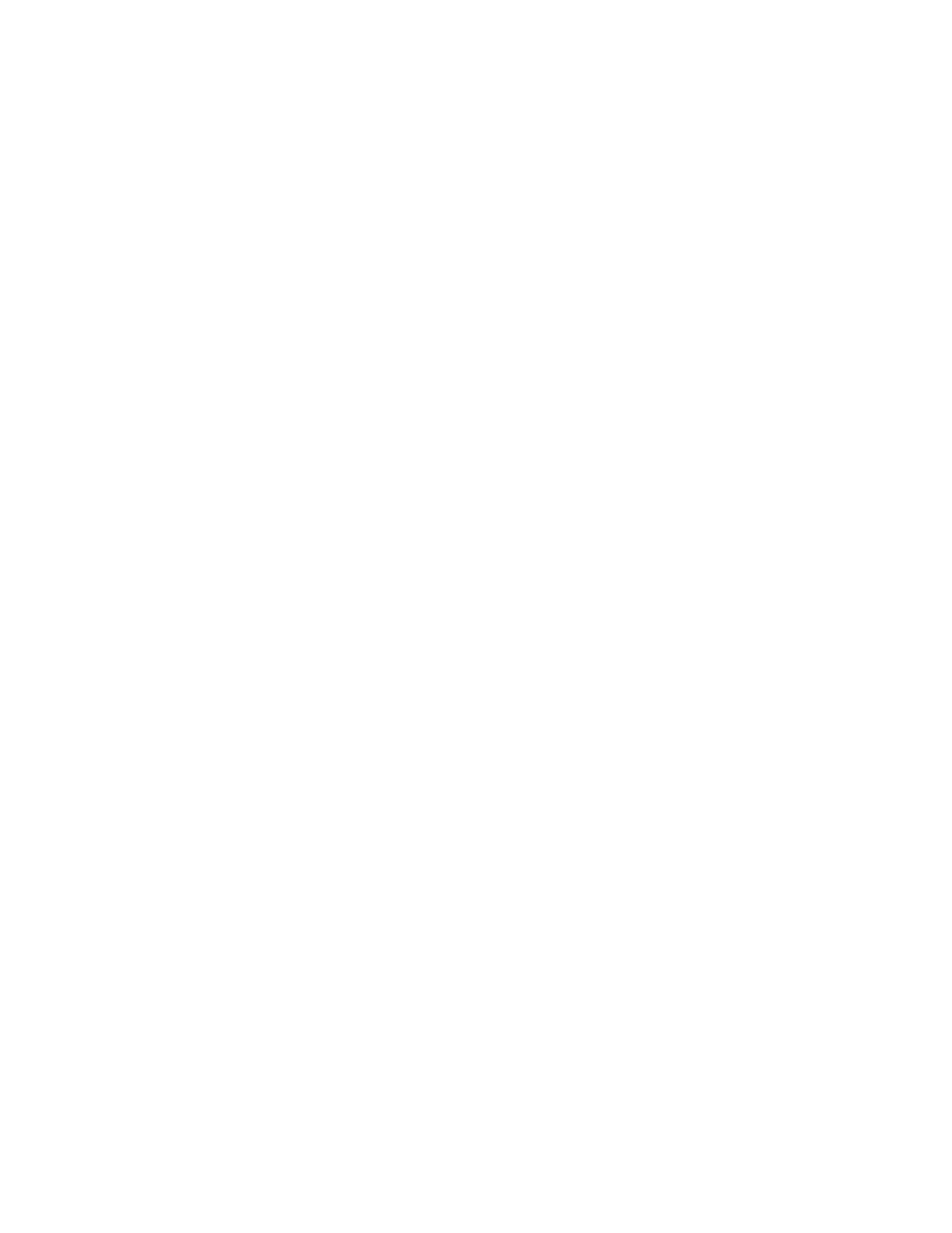
Megaject RTM Pro Manual – Revision 7.00 – 13
th
APRIL 2006
6.2.4. Solvent Pump System
The Solvent tank requires no routine maintenance. However, if dirt particles and
sediment accumulate within the solvent tank base, remove the solvent pump and clean
the solvent container before refilling the tank with fresh solvent.
The remaining solvent system should only be routinely maintained by weekly checks
to locate any leaks or damaged pipes which should be rectified immediately.
6.3. Resin System Re-priming
This procedure is to be carried out when the operator wishes to change the resin in a
machine that has already been commissioned.
To re-prime the system, perform the following steps:
1.
Remove the resin pick-up pipe from the resin and then recirculate the machine
to empty the fluid lines.
2.
In order to clean the lines and pump, place the pick pipe into a solvent
container and recirculate until clean solvent is observed at the recirculation
pipe. This step may be skipped, if the new resin is used to chase through and
purge the older resin from the lines.
3.
Place the recirculation pipe into a waste container and then put the pick-up
pipe into the new fluid. Recirculate the machine until all the solvent is
discharged for the system and new fluid is observed at the recirculation pipe.
4.
Place the recirculation pipe into the fluid container with pick up pipe.
5.
Continue recirculating until material is free of all air bubbles.
NOTE: If the new material is of a similar chemical type to the existing material, then
it may not be necessary to clean the system with solvent before loading the new
material.
NOTE: DO NOT leave the machine empty OR full of solvent for extended periods.
6.4. Preparing the Machine for a Period of Inactivity
If the RTM Megaject Pro is likely to be unused for a long period of time, such as
during a factory shutdown, care must be taken to prepare the machine against
accelerated resin gelling inside the entrance to the mixing head. The fittings from the
resin recirculate valve to the first NRV are always static and not recirculated. It is
important therefore to flush this forward with unaccelerated resin when setting the
machine for close down.
This is achieved by firstly purging the machine of accelerated resin and the refilling
the machine with un-accelerated resin by using the recirculate mode. The operator
should then use the manual injection mode to inject a small quantity (1-2 strokes) of
unaccelerated resin into a suitable container. The machine should then be flushed
normally, taking care to direct the mixing head outlet into a suitable receptacle.
This will ensure that resin that remains in the mixing head at NRV 1 (see section 4.3),
is unaccelerated and therefore will not react with surrounding materials and catalyse.