Bell & Gossett S14334B Technologic 5500 Series Variable Primary Pump and Valve Controller User Manual
Page 9
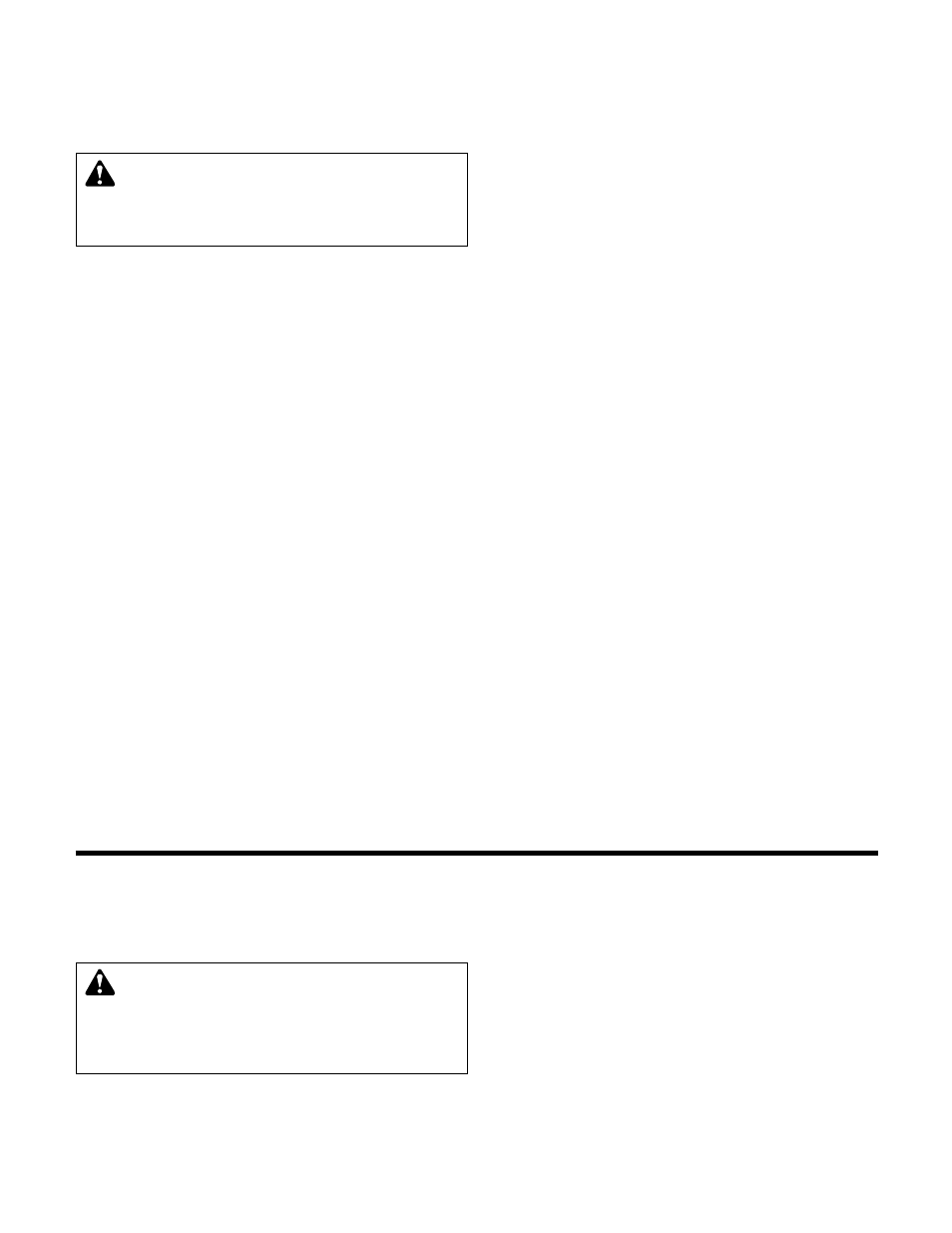
9
1.12.4
Analog Inputs with External Power
The following steps describe the general procedure
for rewiring an analog input sensor when the sensor's
power source is not the Technologic 5500 controller.
1) Turn off all power to the Technologic 5500 controller.
2) Refer to the appropriate controller wiring diagram
that was shipped with unit. Locate the analog
input sensors on the wiring diagram that will be
rewired. They are labeled AI X.
3) Remove the 24 VDC positive (+) wire from TB 40
for the respective analog input sensor connection.
This wire needs to be removed completely or ter-
minated if used as a jumper. This will prevent any
accidental contact with a negative (-) voltage
source (i.e. control panel) and avoid becoming a
short circuit. Care should be taken to ensure that
24 VDC positive (+) voltage is still provided to any
remaining sensors that will be powered by the
Technologic 5500 controller.
4) Remove the 24 VDC negative (-) wire from TB 41
for the respective analog input sensor connection.
This wire needs to be removed completely or ter-
minated if used as a jumper. This will prevent any
accidental contact with a positive (+) voltage
source and avoid becoming a short circuit. Care
should be taken to ensure that 24 VDC (-) negative
voltage is still provided to any remaining sensors
that will still be powered by the Technologic 5500
controller.
5) Terminate the negative (-) wire of the sensor to TB
41 of the respective analog input sensor connec-
tion. Terminate the positive (+) wire of the sensor
to the terminal block which is connected to the
positive (+) terminal shown on the Analog input
card.
NOTE: Be certain that the power supplied to other
terminal blocks has not been interrupted! The wires
that were removed in the preceding steps may have
been used as jumpers.
1.12.5
Drive Speed Signals
Drive speed (follower) signals must be wired from the
Technologic 5500 Controller to each of the adjustable
frequency drives. The AFDs must be configured to
accept a 0-10 VDC speed signal with the minimum
speed set for 30% (0 VDC) and maximum speed set
for 100% (10 VDC). All shields must be grounded,
only in the Technologic 5500, to prevent ground
loops and improper signals.
1.12.6
Valve
The Valve must be configured to accept a 4 - 20mA
signal with the closed position set for 4 mA and the
open position set for 20 mA. All shields must be
grounded, only in the Technologic 5500, to prevent
ground loops and improper signals.
1.12.7
Hardwire Communications
Hardwire communications refers to the capability of
the Technologic 5500 Controller to communicate with
an energy management system. Standard communi-
cation features such as remote start/stop and remote
alarm indications are listed below.
1.12.7.1
Remote Start/Stop
Install a switch as indicated on the wiring diagram.
With the LOCAL-REMOTE-OFF switch in the
REMOTE position, this contact closure will provide
the start signal.
1.12.7.2
Remote Alarm Indication
A digital output rated 8 amps at 115V is supplied.
This output closes to indicate an alarm condition
exists.
1.12.8
User Configurable I/O
The Technologic 5500 Controller comes equipped
with the capability to define the operation of any
unused input or output signal. Refer to Section 4.3.9
for detailed information on the I/O Setup Menu.
WARNING: Prevent electrical shocks. Disconnect
the power supply before beginning installation.
FAIL
-
URE TO FOLLOW THESE INSTRUCTIONS COULD
RESULT IN SERIOUS PERSONAL INJURY, DEATH,
AND/OR PROPERTY DAMAGE.
Section 2 - Installation and Startup
2.1
Location
Install the pumping unit appropriately for ease of
inspection, maintenance and service. Observe local
electrical codes concerning control panel spacing.
2.2
Installation of Skid Mounted Systems with
Factory Supplied Pumps
This unit is built to give you years of service if it is
installed properly with a suitable foundation.
2.2.1
Foundation
A base of concrete weighing 2-1/2 times the weight
of the unit is recommended. Check the shipping
ticket for unit weight. Tie the concrete pad in with
the finished floor. Use foundation bolts and larger
pipe sleeves to give room for final bolt location.
Place the unit on its concrete foundation, supporting
it with steel wedges or shims totaling 1" in thickness.
These wedges or shims should be put on both sides
of each anchor-bolt to provide a means of leveling
the base.
DANGER: Heavy load, may drop if not lifted properly.
Do not lift the entire unit by the motor eyebolts. Lift
the unit with slings placed under the unit base rails.
FAIL
-
URE TO FOLLOW THESE INSTRUCTIONS COULD
RESULT IN SERIOUS PERSONAL INJURY, DEATH,
AND/OR PROPERTY DAMAGE.