YSI 5500D-1 User Manual
Page 73
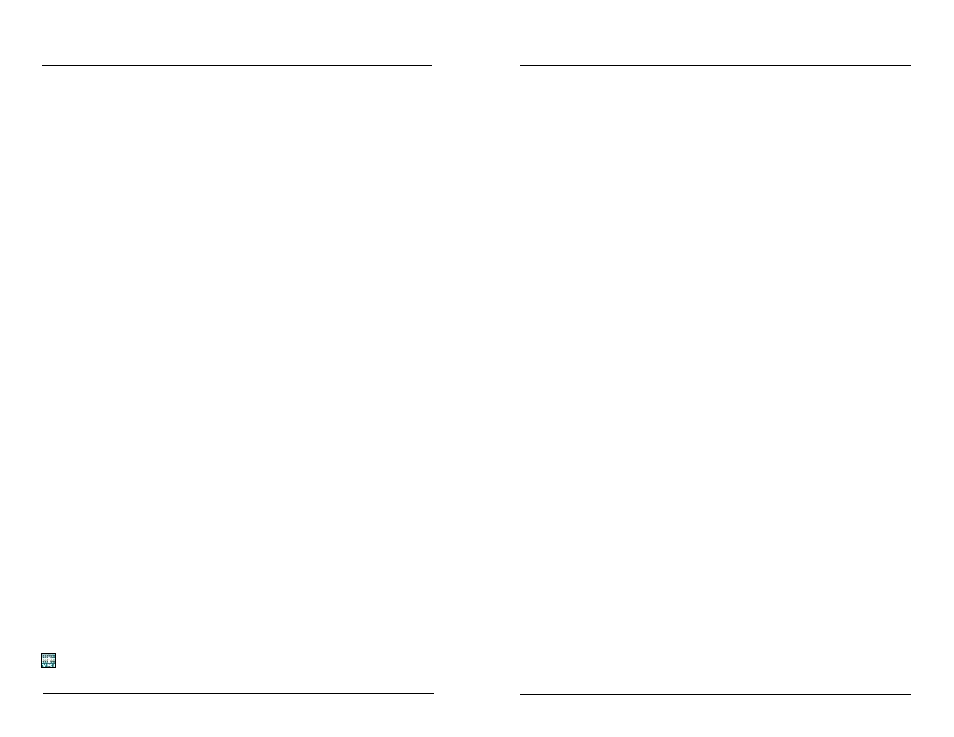
YSI 5X00
145
YSI 5X00
144
PID/PDW Tuning
Each and every water system responds very differently to peripheral control de-
vices due to many factors. Factors that can influence the ability of a control device
to maintain a certain set point include size of system, peripheral equipment such
as pumps, lighting, system location and the like. While PID/PWM tuning is an
important and necessary requirement to properly configure the control system
it is outside the scope of this document to describe the tuning process. There is a
wealth of information available on the www as well as in print. Please familiarize
yourself with additional information in order to further your understanding of the
PID/PWM control method.
Set Point
Configure the set point to be the value at which you’d like the system to ideally
operate at. DO set point can be configured in either mg/L or %Sat at the. Configure
at PID mode menu.
Control Up/Down
Configure the PID/PDW control system to either control up (Falling, to create a
control action to reduce down the system water parameter value) or control down
(Rising, to create a control action to increase up the system water parameter value).
A PID/PDW control can be used only to control the system by either driving the
system value up or down. A PID control cannot be used to drive the system value
both up and down.
PID/PWM Control Actions
Interval, Gain, Reset Interval
Configuration of three control actions allows for greater control and stablity of
a particular environment. The control actions are Gain (page 145), Reset/Inteval
(page 145) and Interval (page 145). These three controls actions are closely inter-
related in terms of how the PID/PWM algothrium works. The objective is to tune
and configure these control actions in order that the corrective action (output con-
trol on time) performed by the 5X00 results in system stability. That is, the system
will hold the set point without oscillating wildly (overshooting or undershooting
by significant amounts) over and under the set point. A large amount of ocillation
could cause irreparable damage to the system by dosing too large an amount, or too
small an amount, of a control dosing additive to the system stream.
AquaManager includes a PID Tuning tool which allows simulation of various control
action values and functions. The PID tuning tool should be helpful in mimicking
your system through simulation. The AquaManager PID Tuning tool is explained
in detail in the AquaManager Help System.
PID/PWM Interval control action
Range 1.00 to 999 (seconds)
Configure the interval control action to be the length of time a complete PID/PDW
control cycle takes. The control cycle includes both the control relay output on time
and the control relay output off time. Example: A 10 second control relay on time and
a 10 second control relay off time would represent a 20 second interval time. The 10
second control relay on time would be expected to decrease as the value reaches set
point. Interval, Reset interval and Gain control configurations are all interrelated in
the calculation of the control relay on time as the algothrium calculates the proper
corrective action.
PID/PWM Reset Interval control action
Range 0.00 to 100 (seconds)
Configure the Reset control action to be the rate at which the PID/PWM cycle re-
sets. In other words at what interval the past errors are erased and the PID/PWM
process begins a new cycle using new errors, and not past errors, in the PID/PWM
formula in calculating corrective action. Interval, Reset interval and Gain control
configurations are all interrelated in the calculation of the control relay on time as
the algothrium calculates the proper corrective action.
PID/PWM Gain control action
Range 0.01 to 10 %.
Gain is used to control the percentage of change in the output. Output increases with
greater gain. A high gain results in a large change in the output for a given change
in the error. A gain of “5” results in an additional 5% output relay on time for each
1% increase/decrease of the measurement. Tuning theory and industrial practice
indicate that gain should contribute the bulk of the output change. Interval, Reset
interval and Gain control configurations are all interrelated in the calculation of
the control relay on time as the algothrium calculates the proper corrective action.
Note:
- Once a PID/PDW control relay energizes the relay completes the interval cycle
based on the latest ratio error and does not automatically deenergize when
the set point is reached. The PID/PWM formula resets all values to 0 once
set point value is achieved and the formula is discontinued. This only occurs
after the interval time expires.
Configuring the 5X00
Configuring the 5X00