Description -2, General -2, Power supply -2 – Hypertherm HD3070 Plasma Arc Cutting System w/ Automatic Gas Console User Manual
Page 37: Automatic gas console -2, Description
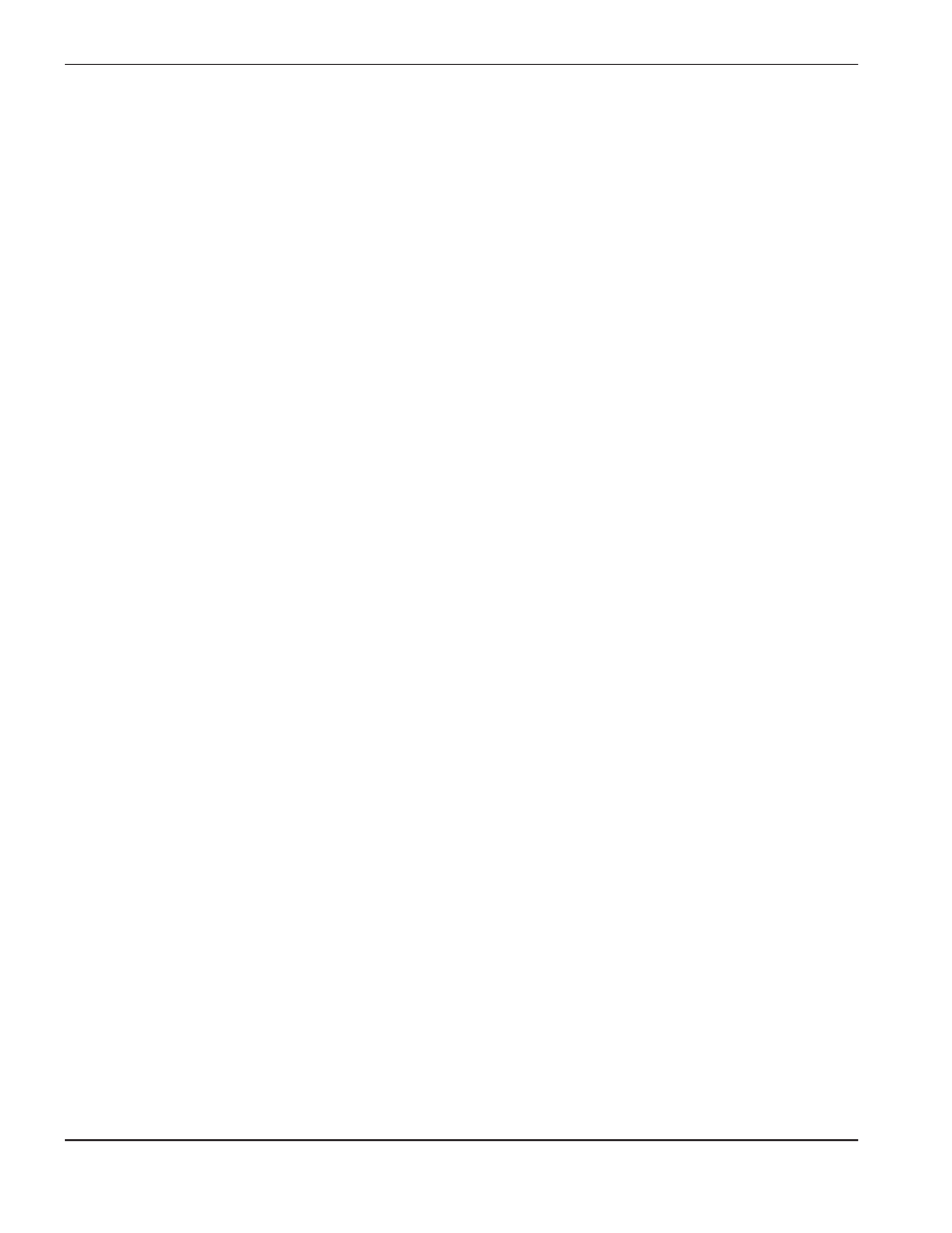
2-2
HD3070 with Automatic Gas Console
Instruction Manual
16
SPECIFICATIONS
Description
General
This manual provides the information needed to install, operate and maintain the HD3070 plasma cutting system
for either robotically controlled or x-y table cutting applications. This precision cutting, dual gas machine-torch
system consists of a power supply, RHF console, gas console, torch quick disconnect assembly, off-valve
assembly and machine torch assembly. Refer to Figures 2-1 and 2-2.
The HD3070 can be configured for different cutting applications by providing a selectable current output at 15, 30,
50, 70 or 100 amps for optimum performance on cutting most metals from gauge to 1/2-inch (12.7 mm) thick. This
allows the operator wide variations in cutting speeds on the same thickness of metal. The gas console provides five
inlets for the different plasma and shield gases required for different cutting applications. The HD3070 is designed
to cut mild steel, stainless steel, copper and aluminum with the appropriate gases and consumables selected.
Plasma gases required for cutting are either oxygen, air or an argon-hydrogen and nitrogen mixture depending on
the application. The shield gas aids in assisting cut quality by providing an atmosphere around the plasma arc on
the surface of the workpiece. The shield gas also cools the shield at the front end of the torch.
Under microprocessor control, the HD3070 provides extended life (LongLife) for the torch nozzle and electrode. To
get long life, all cuts must begin and end on the plate surface; this allows for the proper ramping up and down of
gases and DC current.
Power Supply
This unit houses a 100-amp, 15 kw chopper which produces a constant current DC output, variable from 15 to 100
amps. It contains a microprocessor control PCB which regulates all the plasma system functions: start sequence,
machine interface functions, gas and cut parameters, and off sequence. The power supply main on/off power is
controlled remotely by the CNC machine. The cutting current and pierce delay are also provided by the CNC
machine. The power supply also houses the cooling system required to cool the torch. The power supply
interconnects with the RHF console, machine interface, gas console, and workpiece.
An EMI filter, standard with all 220/380/415V power supplies (078074), meets the CE requirement for filtering
incoming power. Refer to Appendix F to connect incoming power to the filter and for part numbers.
Automatic Gas Console
The gas console is a computer controlled unit which is bolted to the top of the power supply. This unit contains all of
the plumbing and valve systems, computer controls for remote operation, and manual controls for local operation.
The sequencing of the gas valves is under control of the power supply microcomputer.
In remote mode, this unit allows gas flowrates to be set automatically by the CNC machine without an operator
present. The robotic controller interface provides the ability to adjust the metering control of the plasma and shield
gas flows to a high degree of accuracy and repeatability.
In local mode, the operator can control of the gas metering valve set-points, select the gas test modes and the gas
type to be used, and select the calibration modes.