Calibration procedure with five measurements, Calibration procedure for rogowski coil sensors, 2 calibration procedure with five measurements – Maxim Integrated 71M6533-DB User Manual
Page 40: 3 calibration procedure for rogowski coil sensors
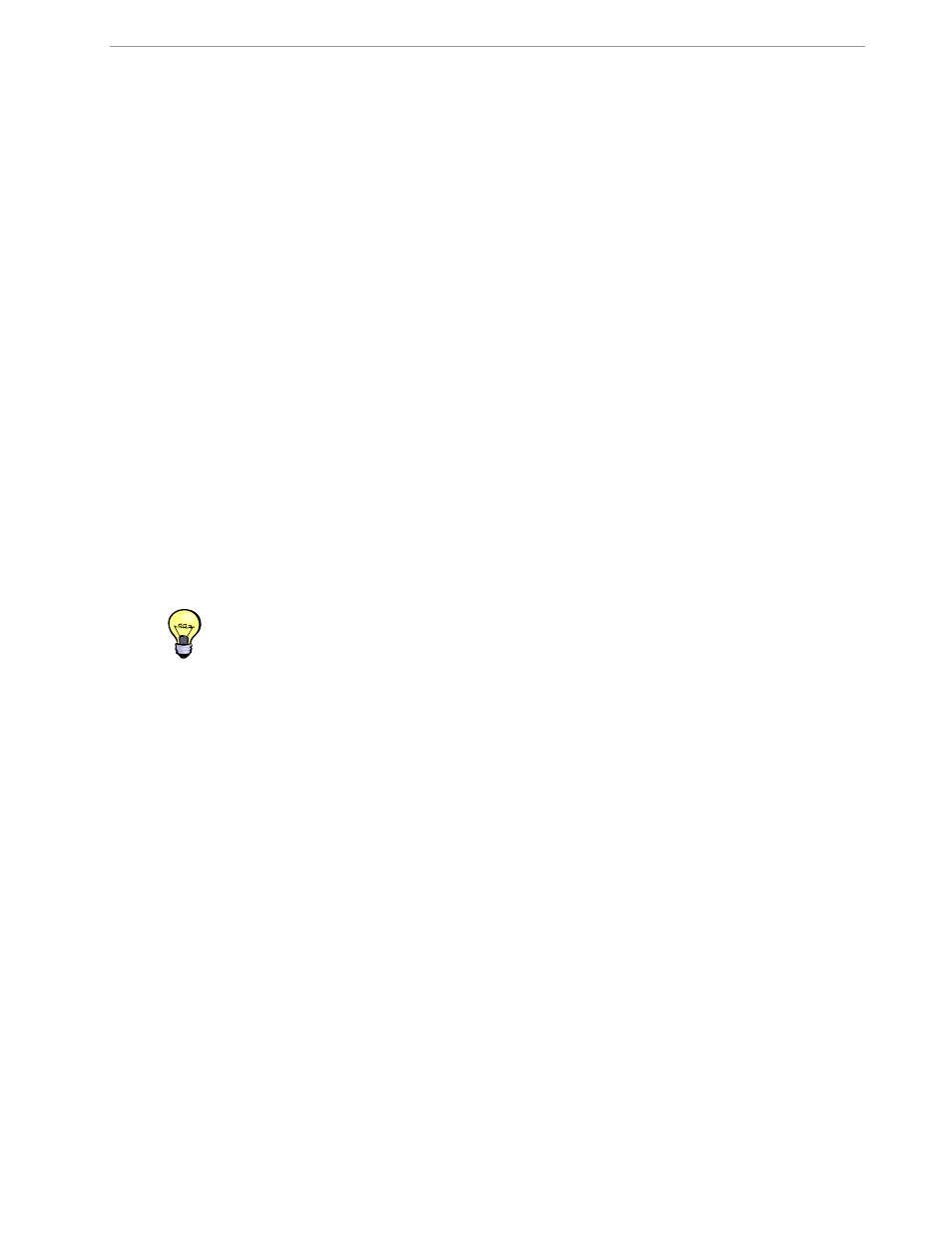
71M6533-
DB Demo Board User’s Manual
Page: 40 of 75
`
REV 3
2.2.2 CALIBRATION PROCEDURE WITH FIVE MEASUREMENTS
Each phase is calibrated individually. The calibration procedure is as follows:
1) The calibration factors for all phases are reset to their default values, i.e.
CAL_In
=
CAL_Vn
= 16384,
and
PHADJ_n
= 0.
2) An RMS voltage V
ideal
consistent with the meter’s nominal voltage is applied, and the RMS reading
V
actual
of the meter is recorded. The voltage reading error Axv is determined as
Axv = (V
actual -
V
ideal
) / V
ideal
3) Apply the nominal load current at phase angles 0°, 60°, 180° and
–60° (-300°). Measure the Wh
energy each time and record the errors E
0
, E
60
, E
180
, and E
300
.
4) Calculate the new calibration factors
CAL_In
,
CAL_Vn,
and
PHADJ_n
, using the formulae presented
in section 2.1.2 or using the spreadsheet presented in section 2.2.4.
5) Apply the new calibration factors
CAL_In
,
CAL_Vn
, and
PHADJ_n
to the meter. The memory
locations for these factors are given in section 1.9.1.
6) Test the meter at nominal current and, if desired, at lower and higher currents and various phase
angles to confirm the desired accuracy.
7) Store the new calibration factors
CAL_In
,
CAL_Vn
, and
PHADJ_n
in the EEPROM memory of the
meter. If a Demo Board is calibrated, the methods involving the command line interface shown in
sections 1.9.3 and 1.9.4 can be used.
8) Repeat the steps 1 through 7 for each phase.
9) For added temperature compensation, read the value
TEMP_RAW
(CE RAM) and write it to
TEMP_NOM
(CE RAM). If Demo Code 4.6n or later is used, this will automatically calculate the
correction coefficients PPMC and PPMC2 from the nominal temperature and from the characterization
data contained in the on-chip fuses.
Tip: Step 2 and the energy measurement at 0° of step 3 can be combined into one step.
2.2.3 CALIBRATION PROCEDURE FOR ROGOWSKI COIL SENSORS
Demo Code containing CE code that is compatible with Rogowski coils is available from MAXIM INTEGRADED
PRODUCTS.
Rogowski coils generate a signal that is the derivative of the current. The CE code implemented in the
Rogowski CE image digitally compensates for this effect and has the usual gain and phase calibration
adjustments. Additionally, calibration adjustments are provided to eliminate voltage coupling from the sensor
input.
Current sensors built from Rogowski coils have a relatively high output impedance that is susceptible to
capacitive coupling from the large voltages present in the meter. The most dominant coupling is usually
capa
citance between the primary of the coil and the coil’s output. This coupling adds a component proportional
to the derivative of voltage to the sensor output. This effect is compensated by the voltage coupling calibration
coefficients.
As with the CT proced
ure, the calibration procedure for Rogowski sensors uses the meter’s display to calibrate
the voltage path and the pulse outputs to perform the remaining energy calibrations. The calibration procedure
must be done to each phase separately, making sure that the pulse generator is driven by the accumulated real
energy for just that phase. In other words, the pulse generator input should be set to WhA, WhB, or WhC,
depending on the phase being calibrated.
In preparation of the calibration, all calibration parameters are set to their default values. VMAX and IMAX are
set to reflect the system design parameters. WRATE and PULSE_SLOW, PULSE_FAST are adjusted to obtain the
desired Kh.