Checkline TI-MVX User Manual
Page 26
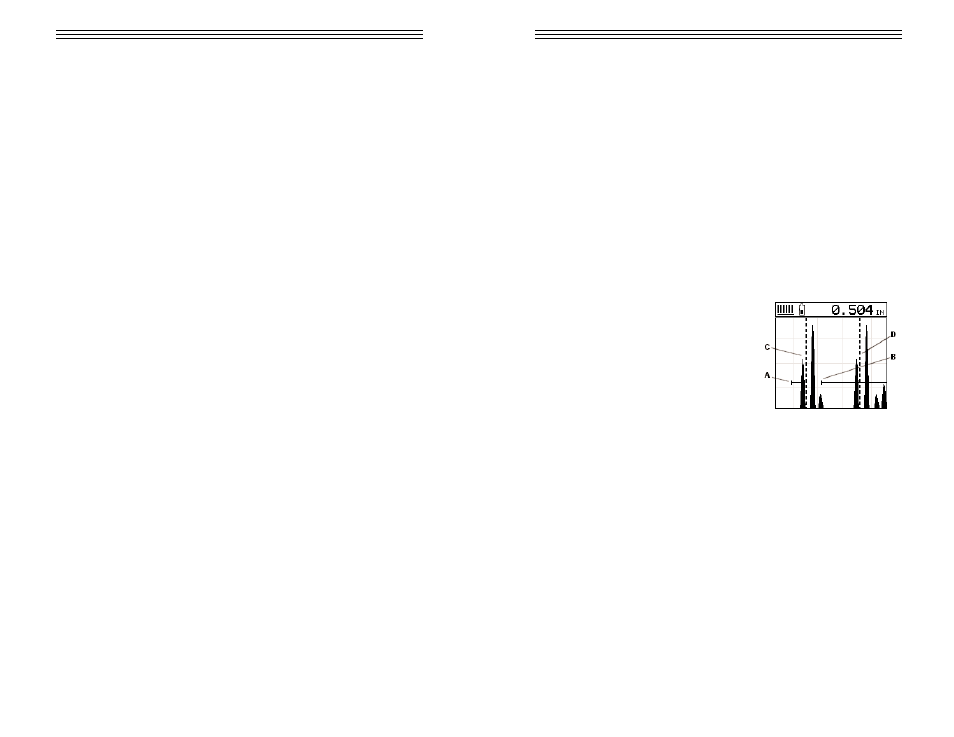
CHAPTER FIVE: SELECTING THE MEASUREMENT MODE
5.1
The setup library
The TI-MVX contains 64 user configurable preset locations to store custom
setups for easy recall. These setups can be optimized for the user’s specific
application needs and can also be stored on a PC and transferred bi-directional-
ly using Dakota’s PC interface software included with the instrument.
The setups supplied with the instrument cover some of the more typical applica-
tions commonly used with this type of instrument. These setups can be recalled,
modified, and overwritten to one of 64 setup locations. Therefore, these factory
setups can also be considered a good starting point to be modified for custom
applications. The PC software includes a default setup file that can be uploaded
to the gauge at any time to restore factory settings. However, it is recommended
that the user consider saving modified setups to an empty location rather than
overwriting the factory setups in the TI-MVX. Once again, these factory settings
are excellent starting points for custom setups.
5.2
Which mode & transducer do I use for my application?
High penetration plastics and castings
The most common mode for these types of applications is pulse-echo. Select a
low frequency transducer. Depending on the thickness of the material, use a
2.25MHz or lower frequency transducer. Larger diameters offer greater penetra-
tion power because of the crystal size, for difficult to measure materials.
Corrosion & Pit Detection in steel
Use pulse-echo mode whenever attempting to locate pits and flaws. Typically a
5MHz transducer, or higher, will be used for these types of applications. Use low
frequencies for greater penetration and use higher frequencies for better resolu-
tion.
Thru Paint & Coatings
Often times users will be faced with applications where the material will be coat-
ed with paint or some other type of epoxy material. Since the velocity of the
coating is approximately 2.5 times slower than that of steel, pulse-echo mode
will induce error if the coating or paint is not completely removed. By using echo-
echo mode, the user is able to successfully measure through both, the coating
and steel, and completely eliminate the thickness of the paint or coating.
Therefore, the steel can be measured without having to remove the coating prior
-26-
CHAPTER EIGHT: THRU PAINT MEASUREMENT TECHNIQUE
8.1 I
Introduction to Thru Paint Measurement
The principle behind thru paint measurement is by measuring the time between
two backwall echoes returning from the test material. Since both of these back-
wall echoes travel the same path through the paint or coating, the thickness of
the coating is subtracted out of the measurement so that only the actual material
thickness can be measured. This feature saves the user a great deal of time
scraping and removing the coating from tanks and pipes during the inspection
process.
The primary purpose of thru paint measurement is to determine actual or overall
material thickness by eliminating the coating thickness. Thru paint mode cannot
be used for flaw or pit detection. Therefore, inspectors will use this echo-echo
thru paint mode in conjunction with a standard pulse-echo flaw detection mode.
The combination of using both modes is ideal for the advanced inspectors
needs.
ECHO – ECHO MODE (THRU PAINT ) – TWO GATES
Refer to the diagram above. This is a typical
example of an echo-echo mode setup com-
monly used for a through paint or coatings
application. Once again, the definition of an
echo-echo measurement, is a measurement
taken between to return echoes, rather than
from the initial pulse to a single echo.
Therefore, the measurement is taken
between the first and second echo reflec-
tions. Point (C) represents the detection on
the back wall of the first reflection. Notice that
GATE1 has been has been set up so that the TI-MVX can only see the first back
wall reflection (C), and cannot see anything before the first reflection. Remember
that the TI-MVX can only see those signals inside the dimensions of the gate.
GATE2 (hold-off) has been set at point (B), so that the transducer ring down
noise following the first detection (C) can’t interfere with the second back wall
reflection (D). The distance from point (C), which is the end of the first gate (A),
to the start of GATE2 (B), is the hold-off time or delay. This type of setup allows
the user to eliminate the paint or coating, and measure only metal the thickness
of the metal.
-55-