Carrier AQUASNAP MPW015-045 User Manual
Page 36
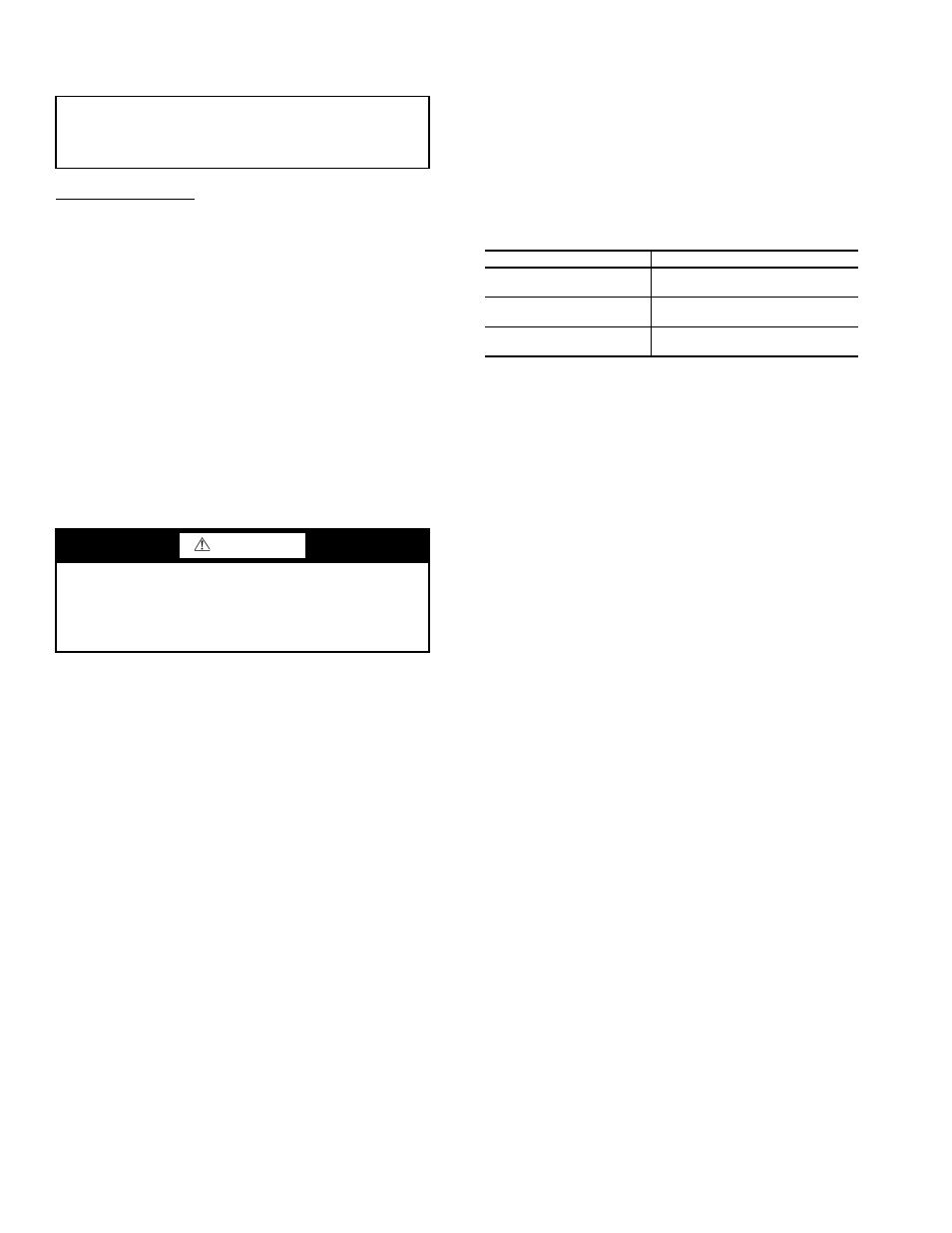
36
This voltage imbalance is satisfactory as it is below the
maximum allowable of 2%.
Control Circuit Power — Power for the control circuit is
supplied from the main incoming power through a factory-
installed control power transformer (TRAN1) for all models.
Field wiring connections are made to the LVT.
OPERATION SEQUENCE
The unit is started by putting the ENABLE/OFF/REMOTE
CONTACT switch in the ENABLE or REMOTE CONTACT
position. When the unit receives a call for cooling (either from
the internal control or CCN network command or remote con-
tact closure), the unit stages up in capacity to maintain the leav-
ing fluid set point. The first compressor starts 1
1
/
2
to 3 minutes
after the call for cooling.
For all units, if temperature reset is being used, the unit con-
trols to a higher leaving-fluid temperature as the building load
reduces. If demand limit is used, the unit may temporarily be
unable to maintain the desired leaving-fluid temperature be-
cause of imposed power limitations.
SERVICE
Electronic Components
CONTROL COMPONENTS — Unit uses an advanced elec-
tronic control system that normally does not require service.
For details on controls refer to Operating Data section.
Access to the controls is through a hinged panel. Inner pan-
els are secured in place and should not be removed unless all
power to the chiller is off.
Compressor Replacement —
All models contain
scroll compressors and have two or three compressors. A com-
pressor is most easily removed from the side of the unit or
above, depending on where clearance space was allowed dur-
ing unit installation. See Fig. 21.
Remove the junction box cover bolts and disconnect the
compressor power and crankcase heater connections (30MPA
only). Remove the cable from the compressor junction box.
Remove the connections from the high-pressure switch. Re-
move the crankcase heater. Knock the same holes out of the
new compressor junction box and install the cable connectors
from the old compressor.
The compressors are bolted to rails, which are in turn bolted
to the unit basepan for all sizes. Remove the 4 bolts holding the
compressor to the rail on the basepan. Save the mounting hard-
ware for use with the new compressor. Carefully cut the com-
pressor suction and discharge lines with a tubing cutter as close
to the compressor as feasible. Remove high-pressure switch
and pressure transducer(s) if required for compressor removal.
Lift one corner of the compressor at a time and remove all the
steel spacers. Remove the old compressor from the unit.
Slide the new compressor in place on the rails. Lifting one
side of the compressor at a time, replace all of the compressor
mounting hardware. Using new tubing as required, reconnect
compressor suction and discharge lines. Using hardware saved,
reinstall the mounting bolts and washers through the compres-
sor feet. Using proper techniques, braze suction and discharge
lines and check for leaks. Reconnect oil equalization line.
Re-install the crankcase heater (30MPA units). Reconnect
the compressor power connections and high-pressure switch
wiring as on the old compressor. Refer to Fig. 21. Following
the installation of the new compressor, tighten all hardware to
the following specifications. (See Table 30.)
Table 30 — Unit Torque Specification
30MPW Condenser and 30MP Cooler
BRAZED-PLATE COOLER AND CONDENSER HEAT
EXCHANGER REPLACEMENT — Brazed-plate heat ex-
changers cannot be repaired if they develop a leak. If a leak
(refrigerant or water) develops, the heat exchanger must be
replaced. To replace a brazed plate heat exchanger:
1. Disconnect the liquid-in and liquid-out connections at the
heat exchanger.
2. Check that the replacement heat exchanger is the same as
the original heat exchanger. For the condensers, compare
part numbers on the heat exchangers. For the coolers, in-
sulation covers the manufacturer’s part number. Make
sure the depths of the replacement and original cooler
heat exchangers are the same.
3. Recover the refrigerant from the system, and unsolder the
refrigerant-in and refrigerant-out connections.
4. Remove the four nuts holding the heat exchanger to the
brackets. Save the nuts.
5. Install the replacement heat exchanger in the unit and at-
tach to the bracket using the four nuts removed in Step 4.
For sizes 015 and 020, torque is 7-10 ft-lb. For sizes 030-
045, torque is 35 to 50 ft-lb.
6. Carefully braze the refrigerant lines to the connections on
the heat exchanger. Lines should be soldered using silver
as the soldering material with a minimum of 45% silver.
Keep the temperature below 1472 F (800 C) under nor-
mal soldering conditions (no vacuum) to prevent the cop-
per solder of the brazed plate heat exchanger from chang-
ing its structure. Failure to do so can result in internal
or external leakage at the connections which cannot be
repaired.
7. For coolers, ensure that the original size tubing is used
(
1
/
2
-in. for sizes 015 and 020 and
5
/
8
-in. for sizes 030-045)
between the TXV and the cooler. The TXV must be lo-
cated within 1 ft of the heat exchanger, with no bends be-
tween the TXV outlet and the cooler inlet.
8. Reconnect the water/brine lines.
9. Dehydrate and recharge the unit. Check for leaks.
BRAZED-PLATE COOLER AND CONDENSER HEAT
EXCHANGER CLEANING — Brazed-plate heat exchang-
ers must be cleaned chemically. A professional cleaning ser-
vice skilled in chemical cleaning should be used. Use a weak
acid (5% phosphoric acid, or if the heat exchanger is cleaned
frequently, 5% oxalic acid). Pump the cleaning solution
through the exchanger, preferably in a backflush mode. After
cleaning, rinse with large amounts of fresh water to dispose of
all the acid. Cleaning materials must be disposed of properly.
IMPORTANT: If the supply voltage phase imbalance is
more than 2%, contact your local electric utility company
immediately. Do not operate unit until imbalance condition
is corrected.
WARNING
Electrical shock can cause personal injury and death. Shut
off all power to this equipment during service. There may
be more than one disconnect switch. Tag all disconnect
locations to alert others not to restore power until work is
completed.
FASTENER
RECOMMENDED TORQUE
Compressor Mounting
Bolts
7 to 10 ft-lb (9.5 to 13.5 N-m)
Compressor Power
Connections
24 to 28 in.-lb (2.7- to 3.2 N-m)
Compressor Ground
Terminal Connections
14 to 18 in.-lb (1.6 to 2.0 N-m)