Verify the correct direction of motor rotation, Determination of tachometer output polarity, Adjusting minimum speed – Rockwell Automation MinPak Plus DC Drive User Manual User Manual
Page 28: Set zero speed
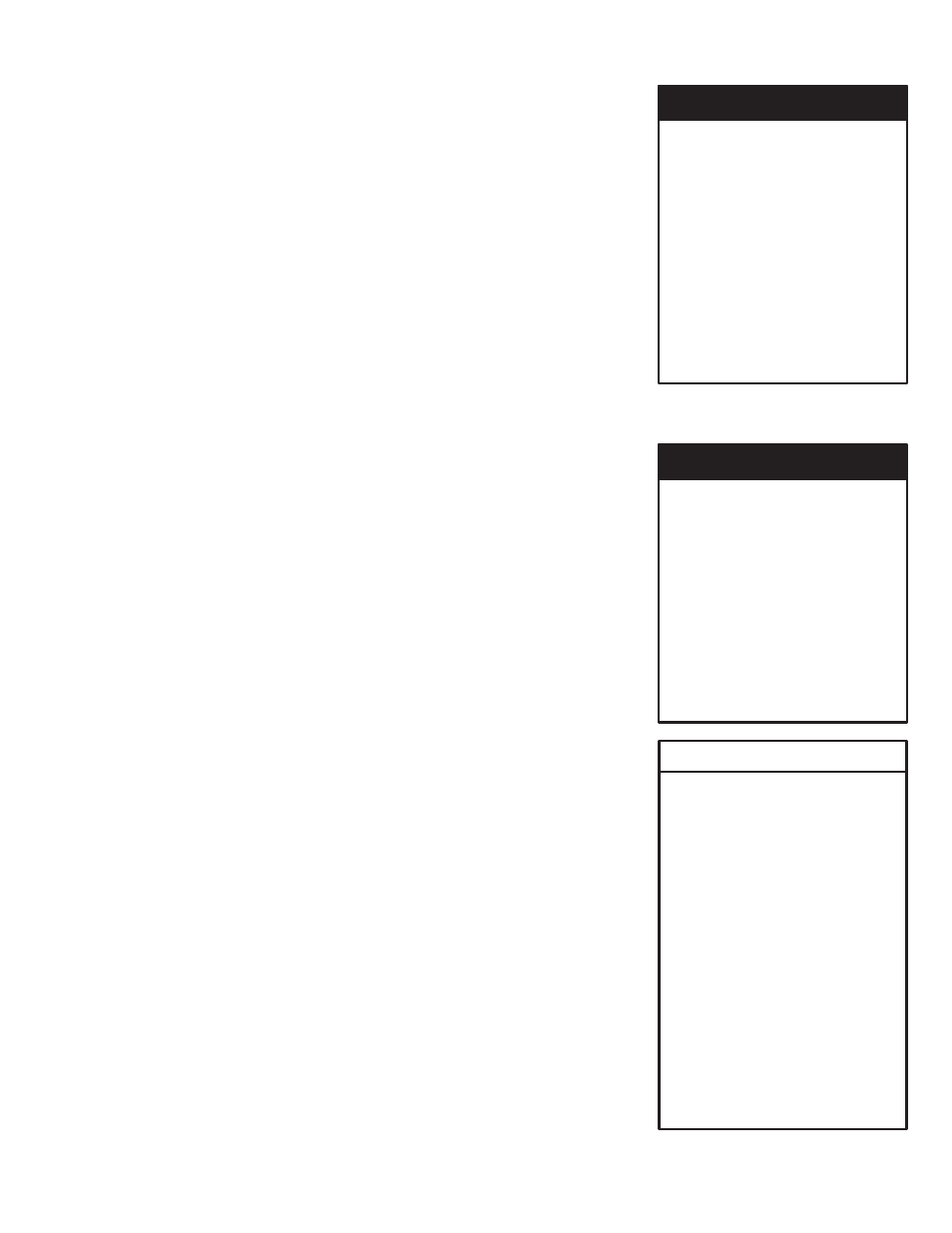
4:5
Verify the Correct
Direction of Motor
Rotation
Connect the regulator mode jumper
to the A" position. (This initially sets
up the drive as a voltage regulator
for purposes of start up. Later on
you may need to move the jumper
to the T" position if your drive is to
be speed regulated.) Set the IR
COMP" rheostat to zero (fully CCW).
Assuming that the drive is using an
operator's station similar to the one
shown in figure 3Ć3:
Set the operators speed pot to
zero".
If a torque pot is used, set it fully
CW.
If an auto/manual" switch is
used, set it to manual".
If a run/jog" switch is used, set
it to run".
If a fwd/rev" switch is used, set
it to fwd".
Now initiate a start". If no motor
rotation is observed, slowly advance
the operator's speed pot until
rotation occurs. Verify that the motor
is rotating in the proper direction for
forward".
If the direction of rotation is wrong,
stop the drive. To change the
direction of rotation, remove all
power, and then switch the A1" and
A2" connections to the motor
armature.
Determination of
Tachometer Output
Polarity
If your system does not employ a
tachometer, this step should be
ignored.
If your system does employ a
tachometer feedback for speed
regulation, the tachometer feedback
kit (Model # 14C221) will need to
be installed. Refer to instruction
manual DĆ3969 for further
information on the setup for the
tachometer feedback kit.
If you are going to use a DĆC
tachometer, and have the feedback
kit installed, it will be necessary to
verify that you have the correct
polarity of tachometer output. To
check the polarity of the tachometer
leads, start the motor and run it in a
forward direction. While the
tachometer is rotating, use a
voltmeter to determine the forward
polarity. Mark the leads accordingly,
(+) and (-).
Adjusting Minimum
Speed
Set the operator's speed pot at zero
and initiate a drive start. Measure
the motor or machine speed with a
hand tachometer to determine when
the desired minimum speed is
reached. Adjust the minimum speed
pot to attain the desired minimum
speed of the machine. Using a
small screwdriver, turn the rheostat
CW to increase the minimum speed,
or CCW to decrease the minimum
speed.
If no tachometer is available, motor
speed can be approximated by
measuring the armature voltage.
Speed is proportional to voltage if
the IR drop is disregarded.
Therefore, if we adjust the minimum
speed rheostat for the right
percentage of armature voltage (as
the minimum speed is a percentage
of designed maximum speed) the
machine speed will be fairly close to
the desired value.
DANGER
ALTHOUGH THE MINIMUM
SPEED ADJUSTMENT ON THIS
DRIVE MAY ALLOW FOR ADĆ
JUSTMENT TO ZERO SPEED.
THIS ZERO SPEED SETTING
MUST NOT BE USED WHERE
THE OPERATOR MAY RELY ON
A MAINTAINED ZERO AS AN
OFF OR STOP CONDITION.
FAILURE TO OBSERVE THIS
PRECAUTION COULD RESULT
IN SEVERE BODILY INJURY OR
LOSS OF LIFE.
Set Zero Speed
DANGER
EQUIPMENT IS AT LINE VOLTĆ
AGE WHEN POWER IS CONĆ
NECTED. LOCKOUT ALL UNĆ
GROUNDED CONDUCTORS
OF THE AĆC POWER LINE
WHEN ALTERING THE MINIĆ
MUM SPEED CIRCUIT FOR
ZERO SPEED APPLICATIONS.
FAILURE TO OBSERVE THIS
PRECAUTION COULD REĆ
SULT IN SEVERE BODILY
INJURY OR LOSS OF LIFE.
WARNING
THE DRIVE IS INTENDED TO
OPERATE AT A PREDETERĆ
MINED MINIMUM SPEED UNĆ
LESS DISCONNECTED FROM
THE POWER SOURCE. IF THE
APPLICATION
REQUIRES
ZERO
SPEED
WITHOUT
SUCH DISCONNECTION, THE
USER IS RESPONSIBLE FOR
ASSURING SAFE CONDIĆ
TIONS FOR OPERATING PERĆ
SONNEL
BY
PROVIDING
SUITABLE GUARDS, AUDIBLE
OR VISUAL ALARMS, OR
OTHER DEVICES. FAILURE
TO OBSERVE THIS PRECAUĆ
TION COULD RESULT IN
BODILY INJURY.