Orbital Antares User Manual
Page 81
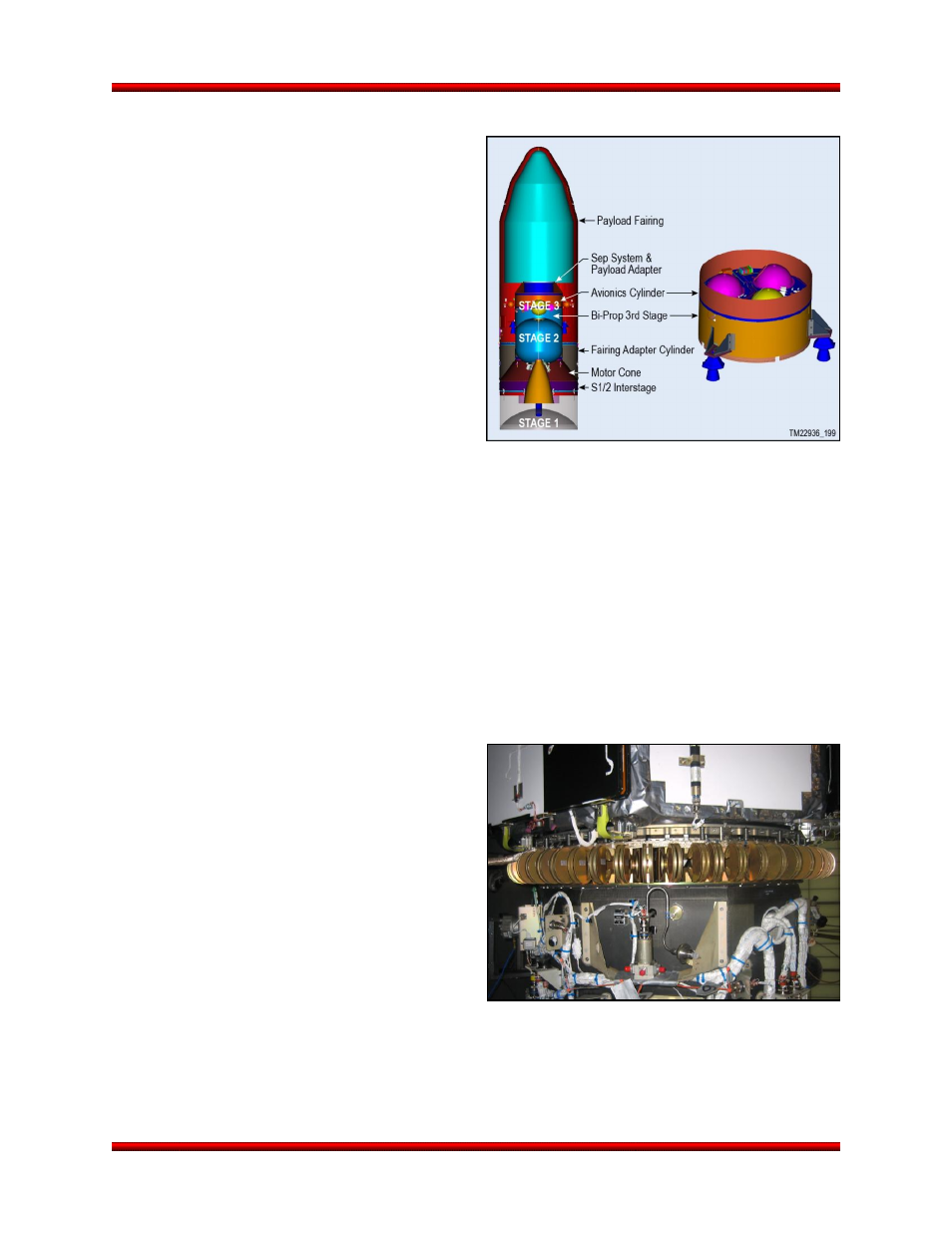
Antares
®
OSP-3
User’s Guide
Section 8.0
– Non-Standard Services
Release 1.1
July 2013
70
8.9. Increased Insertion Accuracy
Orbital offers the Antares Bi-Propellant Third Stage
(BTS), shown in Figure 8.9-1, as an enhancement
to improve insertion accuracy as well as to provide
increased orbital performance capability. The BTS
design is derived from the flight proven satellite kick
stage currently flown on Orbital’s STAR™ bus
Geosynchronous (GEO) satellites. The NTO/N2H4
bi-propellant system feeds three 450 N (100 lbf)
thrusters and provides multi-burn capability to
achieve higher orbit position and accuracy.
The BTS is attached between Stage 2 and the
payload cone, has a diameter of 2.3 m (92 in.) and
has an overall length of approximately 1 m (39 in.).
An additional separation joint is placed between the
BTS and the second stage to allow the BTS to be
separated after Stage 2 motor burnout.
Because the BTS is a liquid stage, the achievable accuracy is limited only by the accumulated navigation
errors during flight, which are dependent on the mission timeline and trajectory chosen. For typical direct
insertions into LEO, the BTS provides 3-sigma accuracies within ±15 km (8 nmi) for both the insertion and
non-insertion apse of the orbit. In addition to improving accuracy, the BTS also improves performance to
altitudes above 300 km (162 nmi), as detailed in Sections 3.3 and 3.4.
8.10. Payload Isolation System
Orbital offers an Antares payload isolation system as an enhancement to facilitate reductions in payload
dynamic environments. The passive Soft Ride isolation system, developed by CSA Engineering, Inc., in-
corporates a flight proven design and integration procedure. This system is comprised of a set of Soft
Ride ―Omniflex‖ mechanical spring/damper ele-
ments which are installed at the Antares’ 1575 mm
(62 in.) payload cone mechanical interface between
the payload cone and the base of the payload sepa-
ration system (See Figure 8.10-1). The Soft Ride
isolation system attenuates low frequency launch
vehicle environments as well as higher frequency
shock to minimize the resulting dynamic environ-
ment that the satellite experiences (see Figure 8.10-
2). Mission specific CLAs are used to tune the de-
sign of the system so as to attenuate critical payl-
oad responses. The Soft Ride system is test verified
in the same manner described above for Minotaur
6.
Figure 8.9-1. Antares Bi-Propellant Third Stage
Figure 8.10-1. Omni-Flex Isolators Are Easily
Integrated Between the Payload and the
Payload Separation System
(Minotaur I Installation Shown)