Orbital Antares User Manual
Page 48
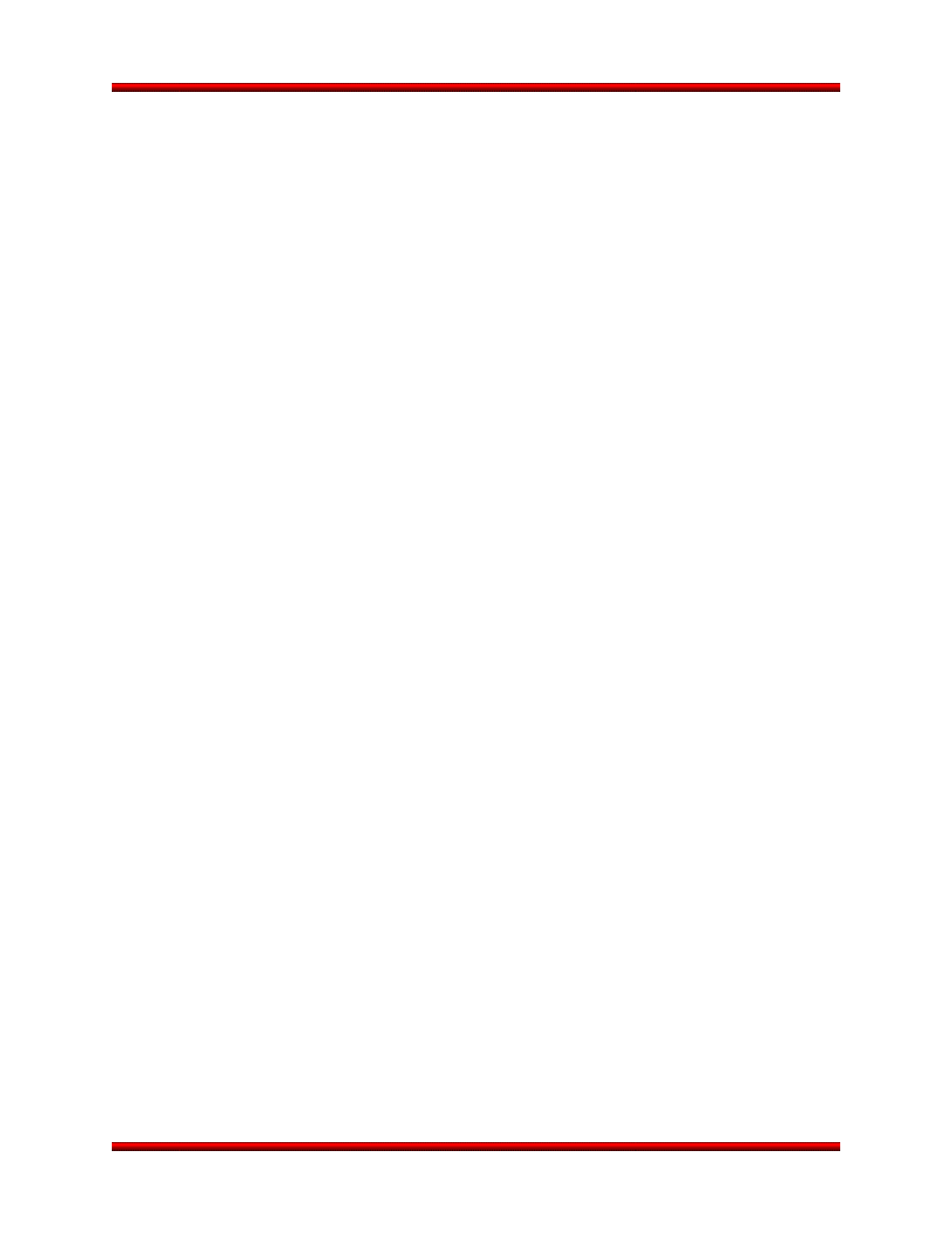
Antares
®
OSP-3
User’s Guide
Section 5.0
– Payload Interfaces
Release 1.1
July 2013
37
Payload Telemetry: The Antares telemetry subsystem provides dedicated payload discrete and analog
telemetry monitors through dedicated channels (up to 24) on the Avionics MACH encoder. In addition, the
Avionics MACH Controller Module has the capability to transmit payload data up to 10 kb/s. The MACH
Encoder serial interface uses an IRIG standard RS-422 driver interface providing a simple, configurable
payload interface definition. The payload serial and analog data is embedded in the baseline vehicle
telemetry format.
Orbital offers a number of non-standard telemetry services to the customer. These options, detailed in
Section 8, include over the horizon telemetry and enhanced telemetry capabilities.
Payload Separation Sensing: Orbital provides two breakwire circuits for the payload to sense separation
from the LV and two independent breakwire circuits for the Antares vehicle to sense separation of the
payload. If an Orbital-provided payload separation system is used (Enhancement A.1), the Antares sys-
tem issues redundant electrical signals to activate the redundant NASA standard initiators on the RUAG
separation system.
Payload Pass-Throughs: Orbital provides pass-through wires between the payload interface plane and
EGSE in-stalled in the LEV at the launch pad. Orbital provides three standard sized 19 in. racks within the
LEV for payload EGSE. Prior to liftoff, the payload is electrically connected to the payload EGSE in the
LEV via two umbilical harnesses. These two payload umbilical harnesses connect to the Antares vehicle
via two separating umbilical connectors (each with 61 pins). Payload electrical connections travel through
#20AWG twisted shielded copper wire from the vehicle, through the two umbilical harnesses, to the TEL
junction box and the payload junction box. To reduce round trip resistance, heavier gauge wiring con-
nects the TEL junction box to the payload junction box in the LEV. Two 61-pin connectors are provided at
the payload junction box to support connection to the payload EGSE. These interfaces can be configured
to support different combinations of conductors defined in the LV/SV ICD. The power conductors provide
minimal power loss to support battery charging, external power, and other current needs of less than 4
amps. The data conductors are typically used for discrete and analog signals and to support RS-422
communication with the payload.
Payload Electrical Harnesses: Orbital fabricates the harnesses on the launch vehicle side of the inter-
face. The payload is responsible for the harnesses forward of the interface plane. The payload side of
the Antares electrical interface may be two individual harnesses or a single Y harness that connects to
both the LV 45° the LV 225° connectors. Any payload flight or flight spare harnesses must meet all re-
quirements specified in the Electrical Interface Control Drawing (EICD). The length and routing of the
payload flight harnesses are specified in the mission-specific MICD.
5.4. Payload Design Constraints
The following sub-sections provide design constraints to ensure payload compatibility with the Antares
system.
5.4.1. Payload Center of Mass Constraints
The axial location of the payload center of mass is typically constrained by the structural capability of the
payload separation system. The 1575 mm (62 in.) non-separating interface structural capability is defined
as a function of payload mass and center of gravity and is limited to 2 m above the bolted interface plane.
Capabilities for the various separation systems enhancements are defined within Section 8.