Antares, Osp-3 user’s guide – Orbital Antares User Manual
Page 43
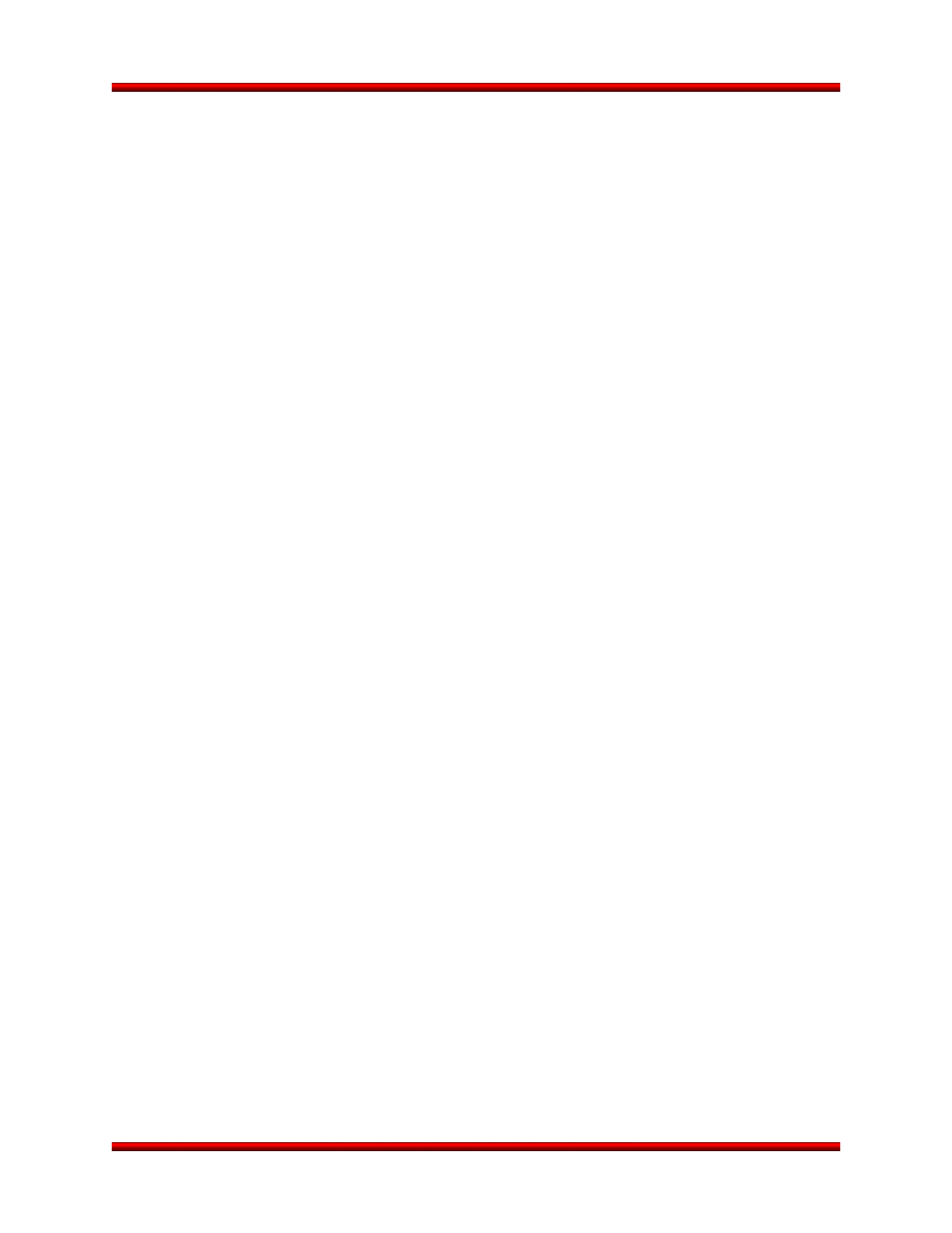
Antares
®
OSP-3
User’s Guide
Section 5.0
– Payload Interfaces
Release 1.1
July 2013
32
5. PAYLOAD INTERFACES
This section describes the available mechanical, electrical and GSE interfaces between the Antares
launch vehicle and the payload.
5.1. 3.9 Meter Payload Fairing
The Antares payload fairing encloses the payload and provides protection and contamination control dur-
ing ground handling, integration and flight. The Antares payload fairing is a 3.9 m (155 in.) diameter
structure consisting of two shells constructed of graphite-epoxy facesheets with an aluminum honeycomb
core and associated separation systems.
While protecting the payload from environments on the ground and during flight, this composite metal ma-
trix also provides a significant level of RF attenuation for the payload during periods of encapsulated
processing.
The two fairing halves are joined with a frangible rail joint along the bi-conic and cylinder sections, and the
base of the fairing is attached to Stage 2 using a ring-shaped frangible joint. The frangible rails and rings
are clean-separation systems employing sealed stainless steel tubes that fracture notched aluminum ex-
trusions. Severing the rail/ring frangible joints allow each half of the fairing to rotate on hinges mounted
on the Stage 2 fairing cylinder. A cold gas generation system is used to drive pistons that force the fairing
halves open. All fairing deployment systems are non-contaminating.
5.1.1. Payload Fairing Static and Dynamic Envelopes
The Antares payload envelopes were developed to ensure that static and dynamic clearances to the
payload assembly are fully maintained during ground operations and ascent. The Antares dynamic
envelope is provided in Figure 5.1.1-1. The dynamic envelope is designed to accommodate the dynamic
deflections and manufacturing tolerances of the fairing and the launch vehicle-to-payload interface struc-
ture. The payload dynamic envelope is dependent on payload deflections as well as the second stage
motor and avionics structure deflections. Fairing doors, cable routing, and nitrogen lines also affect the
dynamic envelope. The dynamic envelope is not a hard interface because the various factors affecting
this envelope must be evaluated in the coupled loads analysis to ensure positive clearance is maintained
between the fairing and payload. Assuming a fixed base reference at the launch vehicle interface, the
payload customer must verify that all elements of the payload remain within the dynamic envelope when
both payload manufacturing tolerances and payload dynamic deflections are taken into account. Payload
dynamic deflection predictions from the CLA are provided to the customer to aid in this verification. Payl-
oad protrusions beyond the dynamic envelope can be evaluated on a case-by-case basis.
5.1.2. Payload Access Door
Orbital provides a 610 mm x 610 mm (24 in. x 24 in.) rectangular RF-opaque graphite-aluminum compo-
site door in the Antares fairing for access to the payload. Orbital also provides an aluminum non-flight
fairing door that the payload may modify as required to support EGSE harness or nitrogen purge line
routing to the payload during ground operations. This door is removed and the flight door is installed 3
days prior to launch. The rectangular door is positioned according to payload requirements within the
zone defined in Figure 5.1.2-1. As a guideline, there should be a minimum axial distance between doors
of 422 mm (16.6 in.), a minimum of 305 mm (12 in.) between the access door edge and the fairing joint.
The payload fairing access door location will be documented in the Mission ICD. Additional access doors
can also be accommodated, as discussed in Section 8. Operationally, the customer has access through
the payload door from the point of fairing enclosure through final vehicle closeout just prior to transport to
pad.