Orbital Antares User Manual
Page 68
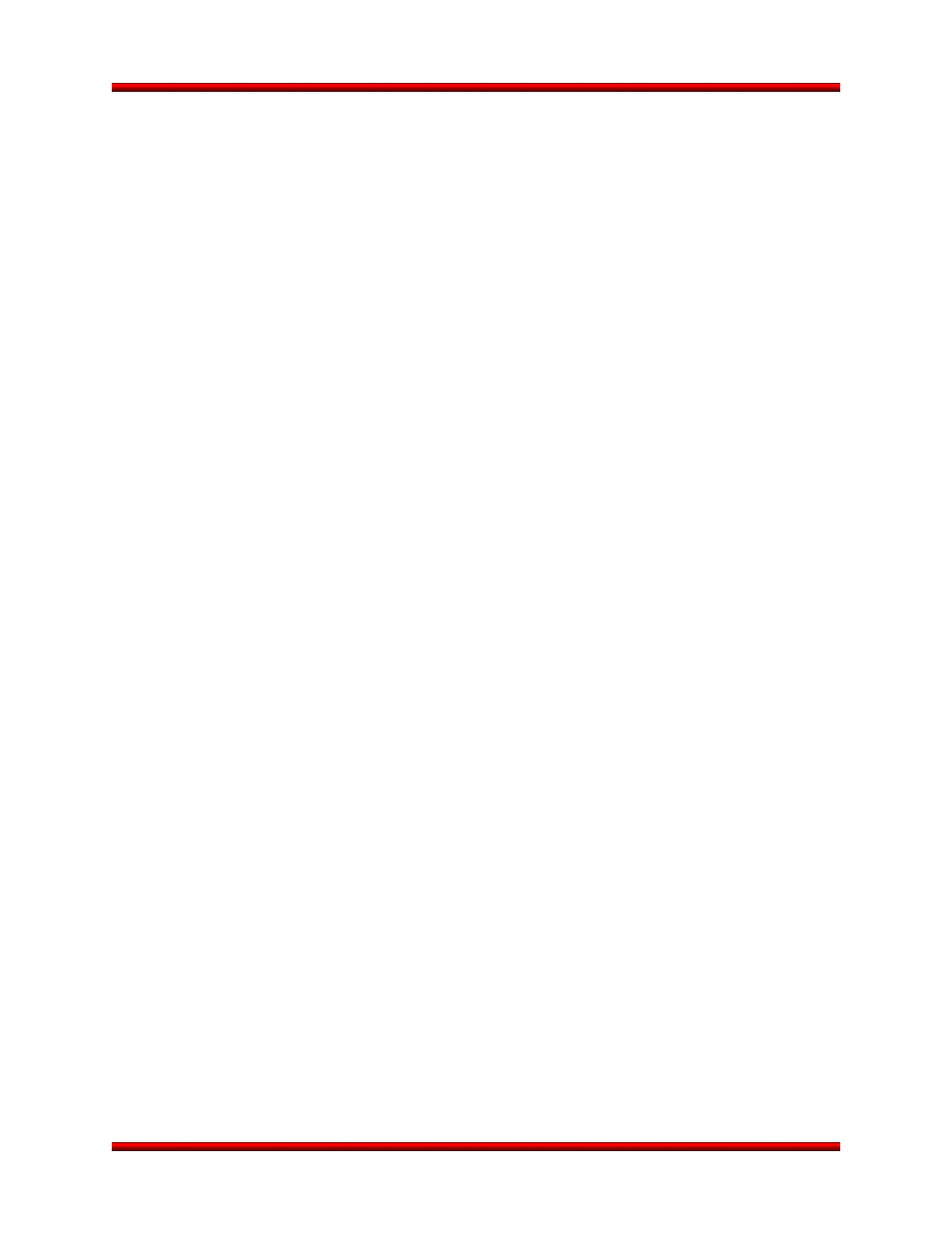
Antares
®
OSP-3
User’s Guide
Section 7.0
– Ground and Launch Operations
Release 1.1
July 2013
57
7.3.2. Stage 2 Motor
The Stage 2 solid rocket motor is received via overland transporter and transferred to its MGSE dolly in
the HIF using the HIF cranes. Mechanical, electrical, and ordnance installation is performed followed by
Thrust Vector Actuator (TVA) performance testing. The avionics section, which is shipped as an assem-
bly from Orbital, is attached to the forward ring of the Stage 2 motor. This assembly, referred to as the
―upper stack‖, completes a series of tests to verify power buses, software, communications, telemetry, RF
systems, and ordnance circuits.
7.3.3. Stage Integration
After both stage subassemblies are completed, the Stage 2 motor is horizontally mated to the Stage 1
core.
The first flight simulation test, which is a ―fly to orbit‖ test exercising the avionics and control sys-
tems of the vehicle, is then performed. The LV is then readied for transport to the launch pad for the Wet
Dress Rehearsal (WDR).
7.3.4. Wet Dress Rehearsal
The WDR is a specialized system-level test that is conducted with the LV in a pre-launch configuration,
minus the payload, at the pad. The WDR includes loading cryogenic propellants to evaluate system per-
formance at cryogenic temperatures. In the WDR, the launch procedures are executed as planned
through L-0.5 sec. This test also validates ground systems, loading procedures, and crew training.
In preparation for the WDR, the integrated vehicle is lifted and installed onto the TEL inside the HIF. The
fairing halves are assembled together and then mated to the upper stack. Once in this configuration the
LV is transported from the HIF to Pad 0A where the WDR takes place. At the completion of the WDR, the
LV is returned to the HIF in preparation for payload mating operations.
7.4. Payload Processing/Integration
Orbital’s approach to payload processing places few requirements on the customer. Once the payload is
fully assembled, checked out, and fueled (if required), the payload is transported to the HIF 15 days be-
fore launch, and integrated to the launch vehicle.
Payload mate occurs with the Antares launch vehicle in a horizontal position in the HIF with the second
stage section cantilevered over the facility floor. Orbital uses the HIF’s overhead crane to lift the payload
off its transporter
using the payload’s lifting fixture and place the payload onto an Orbital-provided
Payload Mate Fixture (PMF). The PMF contains the payload adapter. Next, the electrical connections
between the payload and the Antares payload adapter are made and verified. Then the PMF, supporting
the integrated payload, is rotated to horizontal and placed on ground dollies. Once horizontal, this
payload adapter/payload structure is mated to the forward end of the launch vehicle using these dollies.
Following mate, the flight vehicle is ready for the final integrated systems test and Flight Simulation.
Once consumables are topped off and the final launch vehicle-to-payload closeout is complete, the
payload fairing is installed over the satellite and the second stage assembly. With fairing installation
complete, the environmental control system is then attached to ensure the required payload environments
are maintained inside the fairing until launch. Following payload encapsulation in the fairing, the
customer will coo
rdinate with Orbital’s Antares Mission Manager for any further access to the payload.
After integration of the payload to the Antares launch vehicle is complete, final vehicle preparations are
accomplished. These include end-to-end FTS testing, ACS and separation systems pressurization to