Orbital Antares User Manual
Page 78
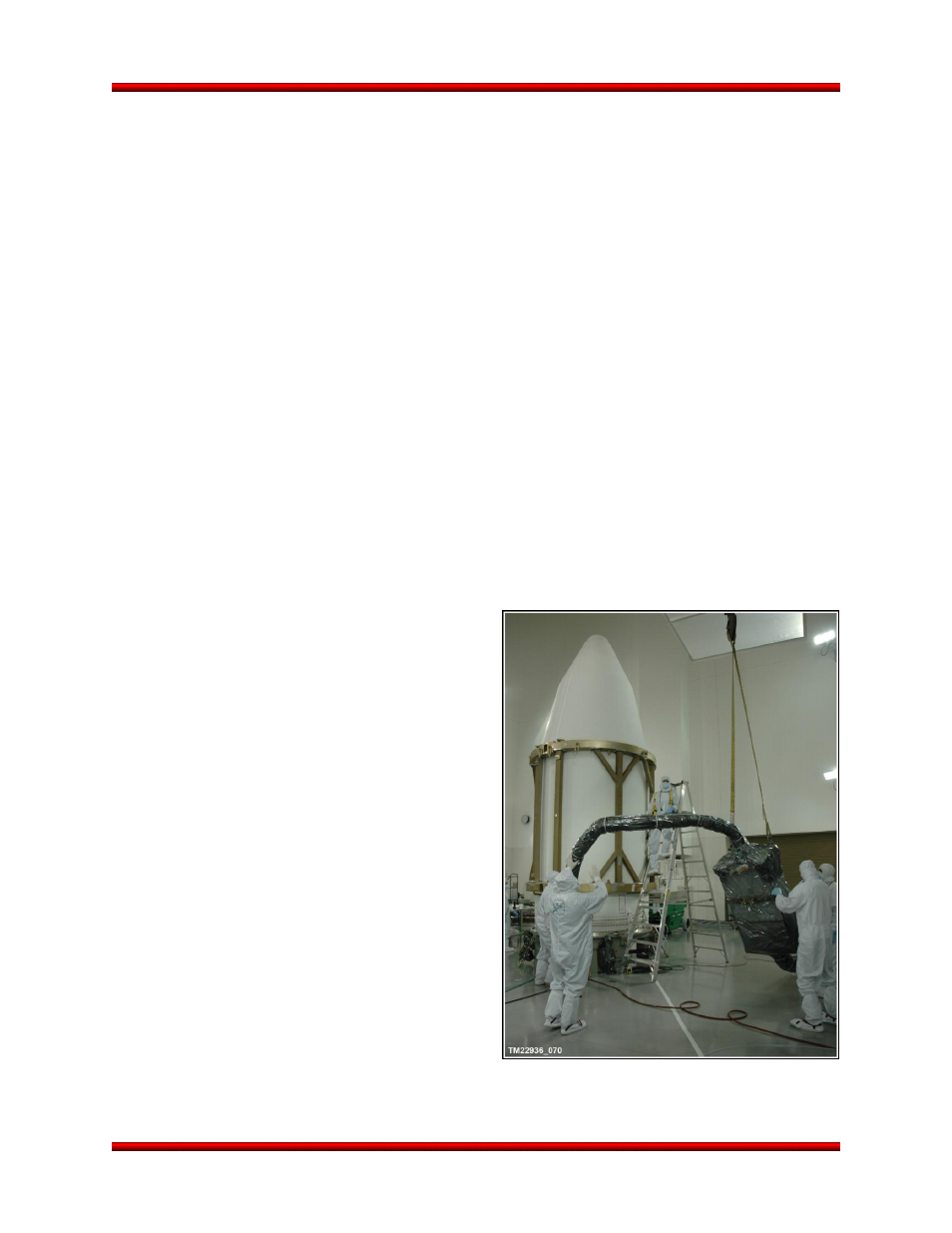
Antares
®
OSP-3
User’s Guide
Section 8.0
– Non-Standard Services
Release 1.1
July 2013
67
8.6. Enhanced Contamination Control
To meet the requirement for a low contamination environment, Orbital uses existing processes developed
and demonstrated on the Minotaur, Taurus, and Pegasus programs. These processes are designed to
minimize outgassing, supply a Class 10,000 (ISO 7) clean room environment, assure a high cleanliness
payload envelope, and provide a HEPA-filtered, controlled humidity environment after fairing encapsula-
tion. Orbital leverages extensive payload processing experience to provide flexible, responsive solutions
to mission-specific payload requirements (Figure 8.6-1).
Orbital provides an Enhanced Contamination Control service, employing additional measures to increase
fairing volume cleanliness and further protect the payload from potential contaminants. Orbital selects
materials used within the fairing volume based largely on their designation as non-outgassing. Specifical-
ly, to the maximum extent possible, Orbital selects materials having a Total Mass Loss (TML) of less than
1.0 % and a Collected Volatile Condensable Materials (CVCM) of less than 0.1 % when tested in accor-
dance with ASTM E595. Orbital tracks all materials used within the fairing volume in a formal Material
Outgassing Data Report, which identifies the TML and CVCM parameters of each material used within
the fairing. For any materials that exceed the TML and CVCM requirements, Orbital identifies their specif-
ic mass and usage location. Passive and active measures are implemented to eliminate or mitigate the
potential for outgassing. For example, encapsulation of a material within a non-outgassing material was
shown to be an effective method of outgassing mitigation for some materials.
With this Enhanced Contamination service, the integration of the payload takes place in a Class 10,000
(ISO 7) environment or better as defined by ISO Standard 14644-1. Orbital implements charcoal filtration
in the ECS and other active integration measures to minimize the presence of hydrocarbons in the inte-
gration area. Hydrocarbon content is monitored to
ensure that hydrocarbon concentrations remain less
that 15 ppm. Relative Humidity is also actively con-
trolled in the integration space to ensure that it re-
mains within a range of 30 to 60%. These same
conditions are maintained whether the payload is in
the integration area or encapsulated within the payl-
oad fairing. The facility ECS, the mobile ECS used
during transportation, and the pad ECS all employ
temperature control, relative humidity control, HEPA
filtration, and charcoal filtration to maintain the payl-
oad in the required environment.
Launch vehicle surfaces within the fairing volume
with a view angle to the payload are cleaned to a
Visibly Clean Plus Ultraviolet (UV) light cleanliness
criteria. Orbital removes particles on these surfaces
visible under normal vision from a distance of 6 to 18
inches with a lighting environment of 100 foot can-
dles. Additionally, particles that are visible under UV
light (3200
– 3800 angstroms) are removed. Orbital
technicians don clean garments and use various me-
thods (e.g., lint free wipes with appropriate grade Iso-
Figure 8.6-1. The Orbital Team Has Extensive
Experience in a Payload Processing Clean
Room Environment