Operation, Thrust and side load characteristics, Thrust loads – MTS Series 215 Rotary Actuator User Manual
Page 39: Operation 39, Thrust and side load characteristics 39
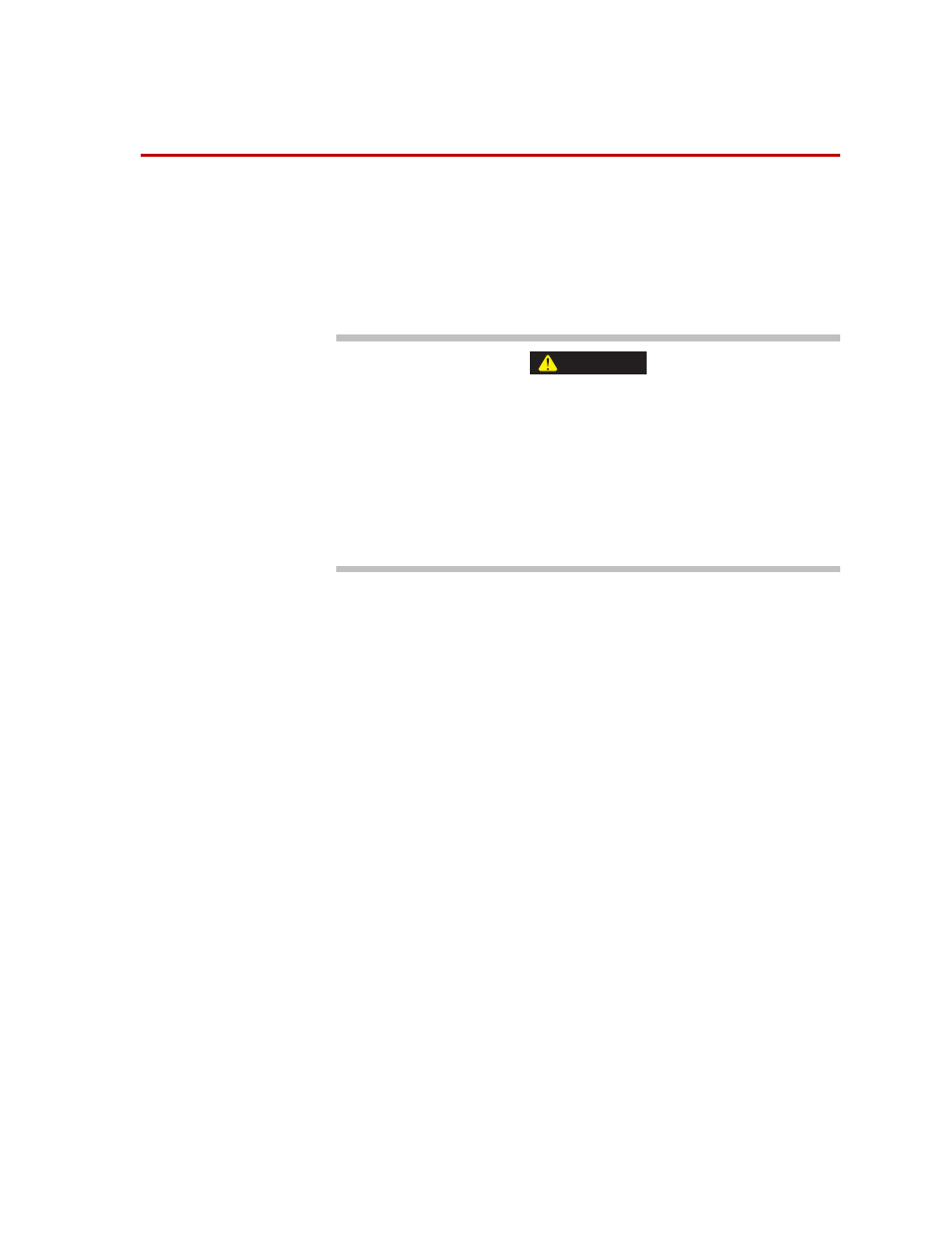
Thrust and Side Load Characteristics
Series 215 Rotary Actuator Product Manual
Operation
39
Operation
This section discusses the calculations and precautions that must be considered in
order to produce accurate test results and help protect equipment and personnel.
Though some of the calculations included in this section may not be required by
specific test situations, it is recommended that you read each section and ensure
that the actuator will be operated within the limits of its thrust load, side load, and
rotational inertia ratings.
Do not exceed the thrust load, side load, or rotational inertia ratings of the
actuator.
Exceeding the thrust load, side load, or rotational inertia ratings of the
actuator can damage equipment, injure personnel, and void any warranty in
effect on the Series 215 Rotary Actuator.
Ensure that the thrust load, side load, and rotational inertia ratings for the actuator
exceed the anticipated test forces. This section contains calculations for deriving
the anticipated test forces.
Thrust and Side Load Characteristics
The thrust and side loads that may be encountered during testing are generally
the result of the following factors:
•
Specimen shortening or lengthening due to torsional force
•
Specimen shortening or lengthening due to temperature
•
Misalignment of the test specimen when initially mounted
•
Base plate or T-slot table twisting
•
Permanent deformation of the specimen due to torsional force
Thrust loads
The following table lists the maximum allowable thrust load (Q) that can be
applied to the actuator rotor shaft. Because thrust loads can be induced by a wide
variety of experimental conditions, this manual will not attempt to define or
predict the forces that can result from specific testing situations. If there is a
possibility that the maximum thrust load rating of the actuator will be exceeded
during testing, steps should be taken to minimize the load. One way of reducing
the effect of thrust loads on the actuator bearings is to install diaphragm flexures.
Thrust loads can have a significant effect on actuator bearings. These effects are a
function of specimen geometry, material, and temperature as shown in the
following example:
Increase the temperature of a steel shaft 25.4 mm (1 in.) in diameter and 1,270
mm (50 in.) in length by 22˚C (40˚F). The increase in specimen temperature
causes the shaft to expand by approximately 0.305 mm (0.012 in.). If the shaft is
CAUTION