Actuator specifications, Actuator specifications 16 – MTS Series 215 Rotary Actuator User Manual
Page 16
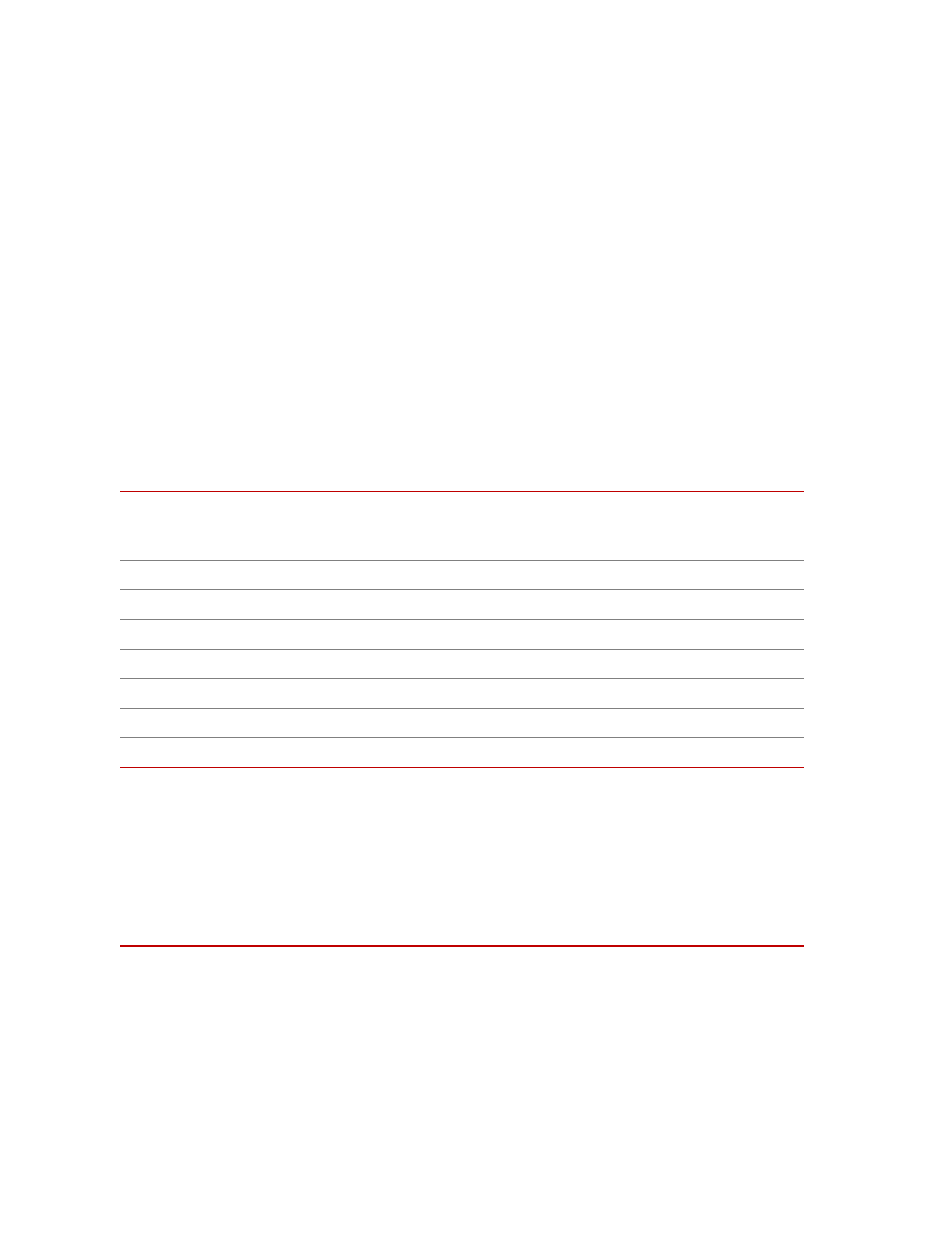
Series 215 Rotary Actuator Product Manual
16
Actuator Specifications
Introduction
As the block diagram shows, a program command signal is input to the
controller. The command signal is compared to the feedback signal from one of
the actuator transducers. If the command signal equals the feedback signal from
the transducer conditioner, no DC error is present and the valve driver circuit
produces little or no servovalve control signal. If the command signal does not
equal the feedback signal, a DC error signal is sent to the valve driver circuit.
The valve driver circuit uses this signal to generate a servovalve control signal.
The servovalve control signal causes the servovalve spool to open in a direction
and by an amount necessary to direct a regulated flow of hydraulic fluid to the
actuator’s pressure or return ports. The actuator moves in response to the flow of
hydraulic fluid. The constant feedback of the closed-loop system enables the
controller to maintain precise control of actuator torque or movement.
Actuator Specifications
Series 215 Rotary Actuators are available in six models. This section lists
specifications for both the Series 215 Actuator and its options.
Series 215 Rotary Actuator Ratings by Model
M
ODEL
R
ATED
T
ORQUE
*
D
ISPLACEMENT
T
HRUST
L
OAD
Q (M
AXIMUM
)
S
IDE
L
OAD
†
P (M
AXIMUM
)
B
ENDING
M
OMENT
M (M
AXIMUM
)
lbf·in.
N·m
in.
3
/rad
cm
3
/rad
lbf
kN
lbf
kN
lbf·in.
N·m
215.32
2000
226
0.80
13.1
750
3.3
1500
6.67
3600
405
215.35
5000
565
1.9
31.1
750
3.3
3500
15.57
15,400
1732
215.41
10,000
1130
3.7
60.6
750
3.3
3500
15.57
15,400
1732
215.42
20,000
2260
7.2
117.9
750
3.3
3500
15.57
17,300
1946
215.45
50,000
5650
19.0
311.3
1200
5.3
5700
25.36
43,000
4837
215.51
100,000 11,300
38.0
622.7
1200
5.3
6500
28.92
50,000
5625
* Actuator is designed for cyclic use at rated torque: rated at maximum differential pressure at 21 MPa
(3000 psi).
† P and M are interdependent: if P is at maximum, M must be zero; if P = 75% of maximum, M may
be up to 25% of its maximum value.
‡ If these values are to be exceeded, additional internal or external cushions are required; contact
MTS.
§ w = rotational velocity in rad/sec and J or I = rotational inertia in lbm-in.
2
or kg-m
2
including inertias
from rotary actuator, flange, flexure, and 1/2 of test specimen (lbm = pounds mass).
¶ Does not include flange adapter.