MTS Series 215 Rotary Actuator User Manual
Page 37
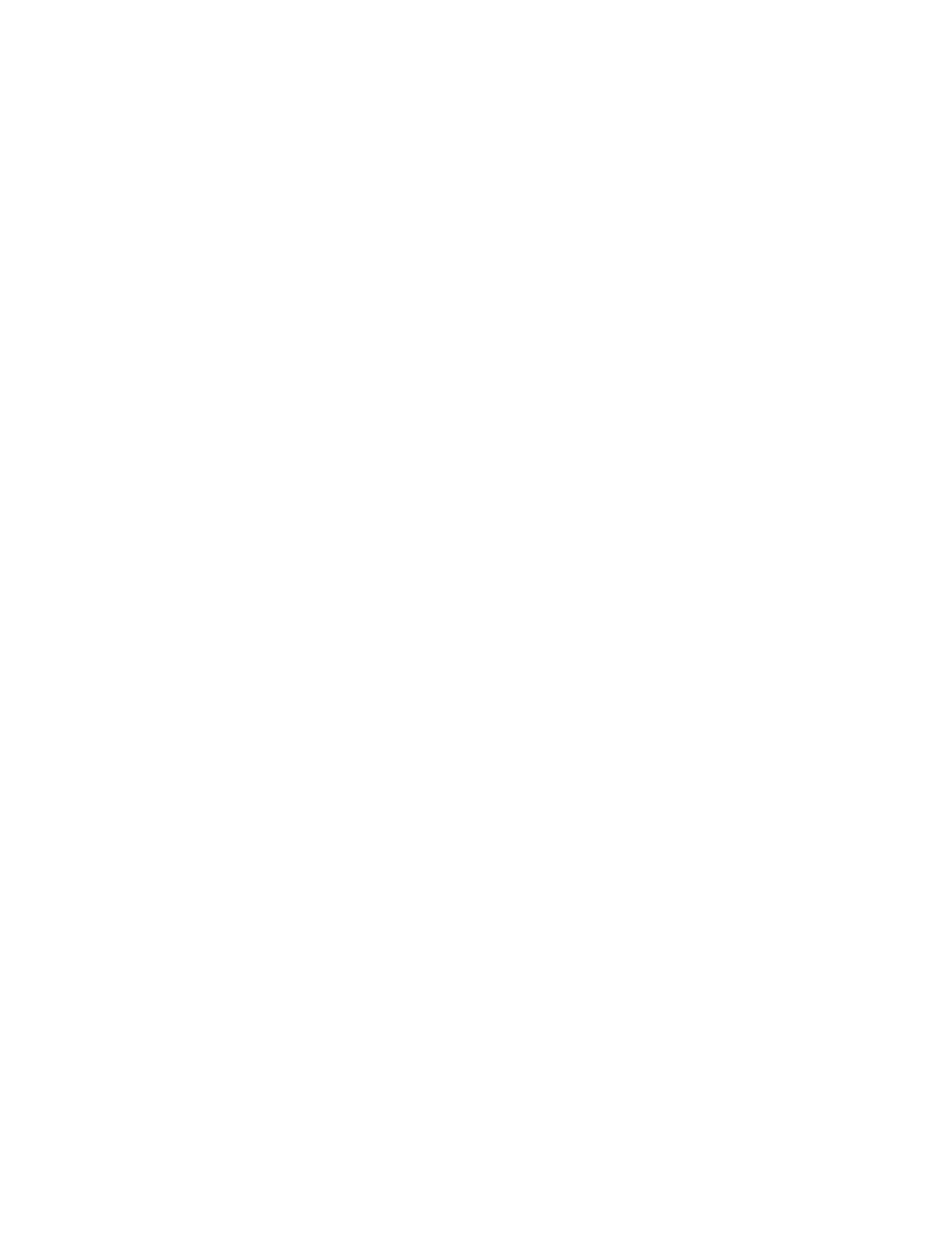
Adjusting Actuator and Torque Cell Centerline
Series 215 Rotary Actuator Product Manual
Installation
37
Adjusting Actuator and Torque Cell Centerline Angularity
The final alignment procedure adjusts for centerline angularity deviations
between the actuator rotor shaft and the torque cell flange face.
Do not apply hydraulic pressure to the system unless the servovalve command
(DC error) has been zeroed.
If the servovalve command (DC error) does not equal zero when hydraulic
pressure is applied to the system, equipment damage or personal injury can
result.
Always ensure that the DC error is zero before applying hydraulic pressure to the
system.
1. Adjust the system controller for zero DC error and apply system hydraulic
pressure according to applicable system procedures.
2. Attach a dial indicator to the actuator rotor shaft using a magnetic V-block
for the base. Set the dial indicator to read the runout of the torque cell flange
face, outside the bolt circle area.
3. Use the Set Point control on the controller to rotate the actuator rotor shaft
while simultaneously reading the indication from the face of the torque cell
flange.
4. To obtain a reading over a wider range of motion, reposition the V-block on
the opposite side of the actuator rotor shaft and repeat Step 3.
5. Adjust the torque cell position for an acceptable level of angularity by
loosening and moving the reaction bracket. The acceptable level of
angularity is determined by the test requirements.
6. After positioning the torque cell, re-tighten the reaction bracket mounting
bolts to the appropriate torque.
7. Turn off system hydraulic pressure.
8. Repeat the “Actuator and Torque Cell Centerline Height” and “Actuator and
Torque Cell Concentricity” procedures to ensure that all measurements
conform to the requirements of the test.