8 commissioning the canopen logic bus, 1 overview of the commissioning steps, Commissioning the canopen logic bus – Lenze CANopen control technology User Manual
Page 40: Overview of the commissioning steps, Control technology | canopen communication manual, 8commissioning the canopen logic bus
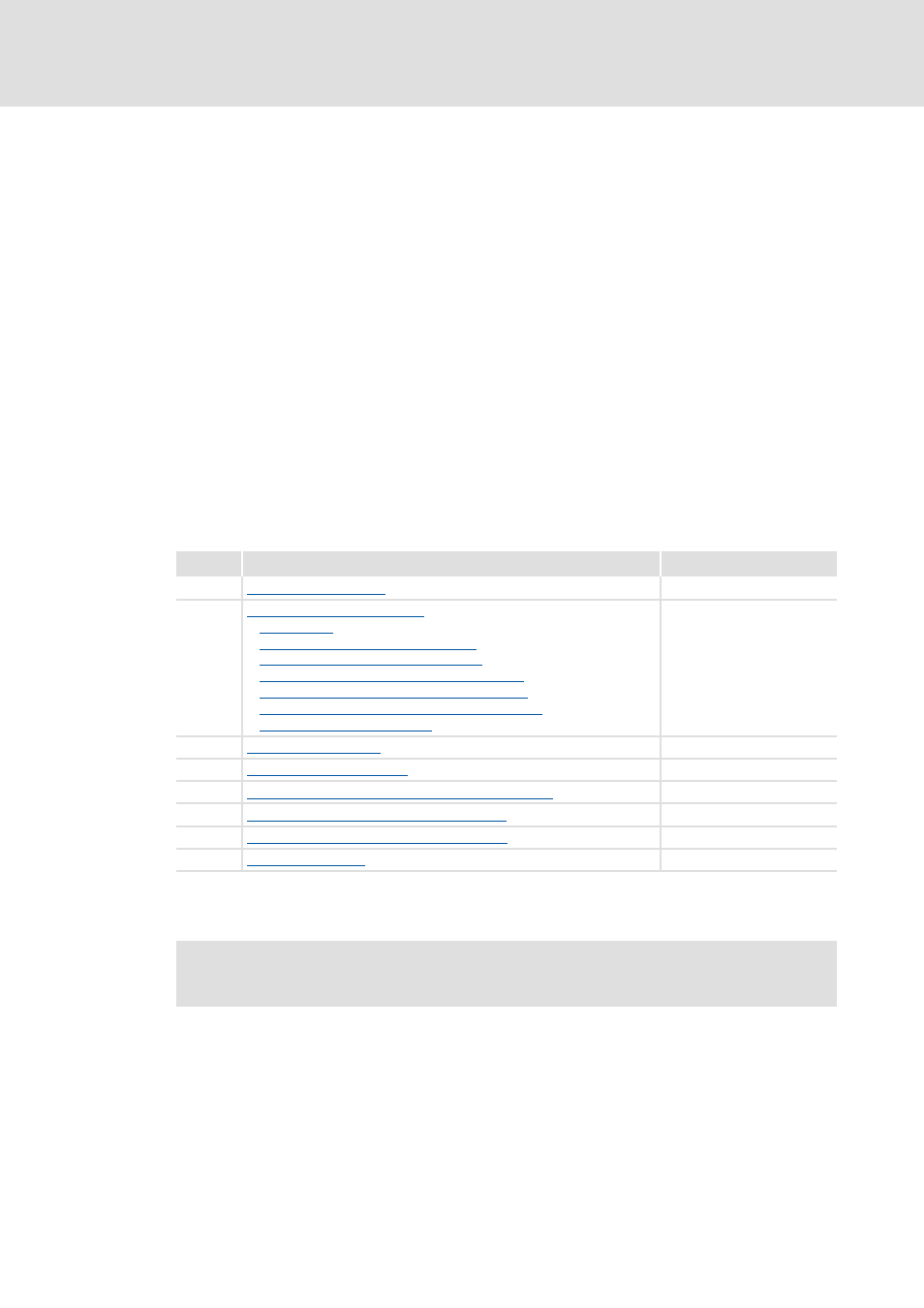
Control technology | CANopen communication manual
Commissioning the CANopen Logic bus
Overview of the commissioning steps
40
L
DMS 4.2 EN 07/2011 TD17
8
Commissioning the CANopen Logic bus
This chapter provides information on commissioning the Lenze control system using the
CANopen Logic bus.
Depending on the field devices used, the following Lenze engineering tools are required:
»PLC Designer«
»Engineer«
»Global Drive Control« (GDC)
Tip!
For using other fieldbus systems, you may require further engineering software.
More information can be found in the corresponding communication manuals.
8.1
Overview of the commissioning steps
The individual commissioning steps are described in the following. Observe the given
instructions step-by-step to commission your system.
Step
Activity
Lenze software to be used
1.
Creating a project folder ( 41)
2.
Commissioning of field devices ( 42)
Commissioning the Servo Drives 9400 ( 44)
Commissioning of 8400 Inverter Drives ( 47)
Commissioning of I/O system IP20 (EPM-Txxx) ( 50)
Commissioning of I/O system 1000 (EPM-Sxxx) ( 51)
Commissioning of 8200 vector frequency inverter ( 52)
Commissioning of ECS devices ( 53)
»Engineer« or
»Global Drive Control«
(depending on the used
device)
3.
»PLC Designer«
4.
Configuring the CAN master ( 57)
»PLC Designer«
5.
Integrating field devices (slaves) into the PLC program ( 59)
»PLC Designer«
6.
Setting of CAN parameters and CAN mapping ( 60)
»PLC Designer«
7.
Creating a program code to control the device ( 65)
»PLC Designer«
8.
»PLC Designer«
More detailed information about how to work with the Lenze engineering tools
can be found in the corresponding manuals and online helps.