Control technology | canopen communication manual – Lenze CANopen control technology User Manual
Page 104
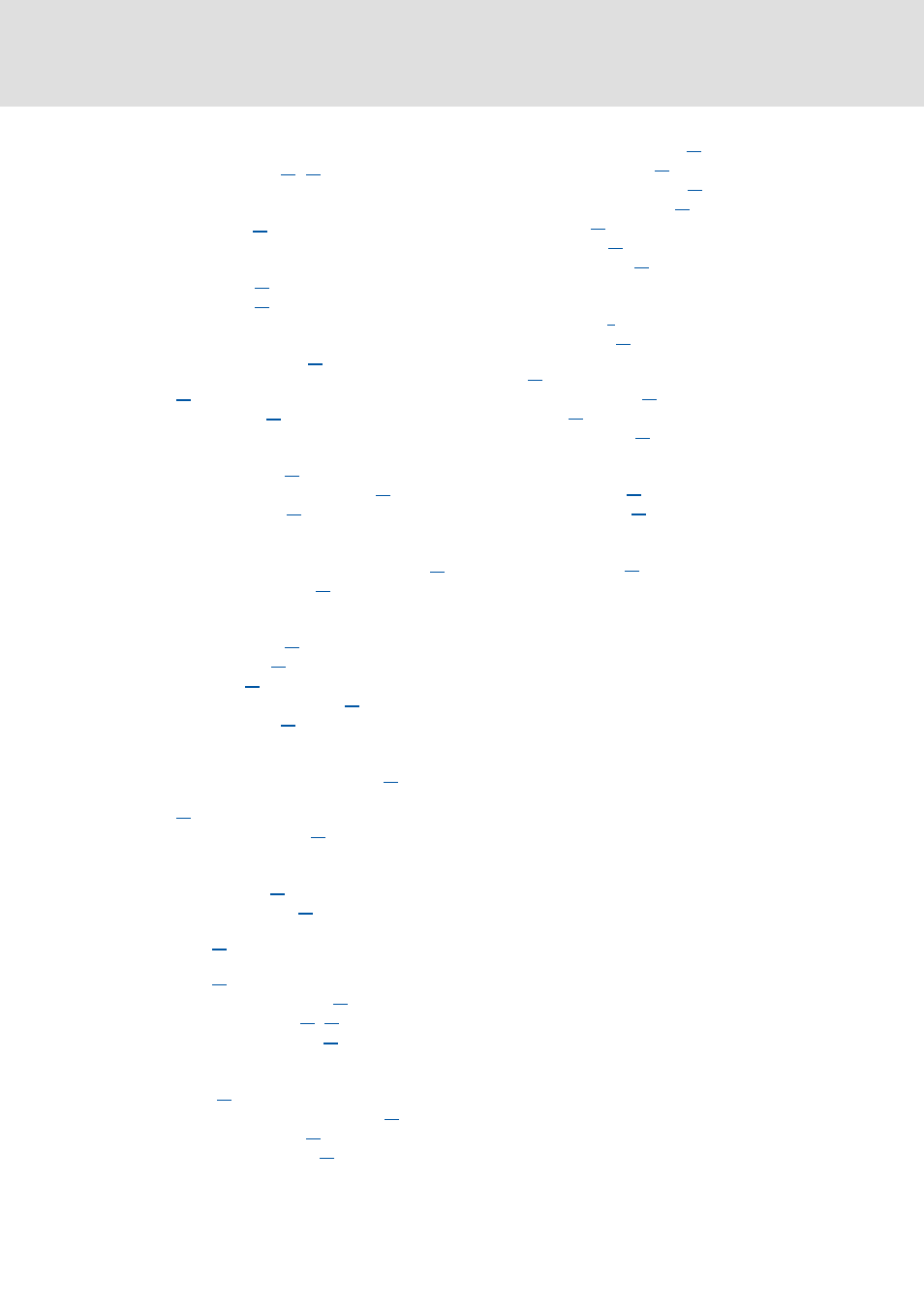
Control technology | CANopen communication manual
Index
104
L
DMS 4.2 EN 07/2011 TD17
E
Engineering tools
,
F
Field devices
G
General data
Going online
I
Installing field devices
Integrating field devices (slaves) into the PLC program
IPC as gateway
L
LenzeCANdrive.lib
LenzeCANdrive.lib function library
Logbook of the IPC
M
Mixed operation (CANopen with PROFIBUS)
Max. number of drives/
N
Network topology
Node addresses
Notes used
Number of DI + DO (bits/ms)
Number of nodes
O
Optimise signal propagation delays
Optimising the signal propagation delays (optional)
Optimising the system
P
Parameter data
Parameter reference
Parameters of the MC-CAN2 communication card in
slot 1
Parameters of the MC-CAN2 communication card in
slot 2
Planning the CAN network
Preparing the restart
PROFIBUS with CANopen
S
Safety
Safety instructions (representation)
Segment cable length
Setting of CAN mapping
Setting of CAN parameters
Setting the baud rate
Setting the node addresses
Signal propagation delay
Standards
Sync phasing
System bus (CAN)
T
Target group
Technical data
Technical data of the MC-CAN2 communication card
Telegram runtimes
Terms
Total cable length
U
Use of repeaters
Using PCAN view
V
Variable wState