NORD Drivesystems BU0220 User Manual
Page 90
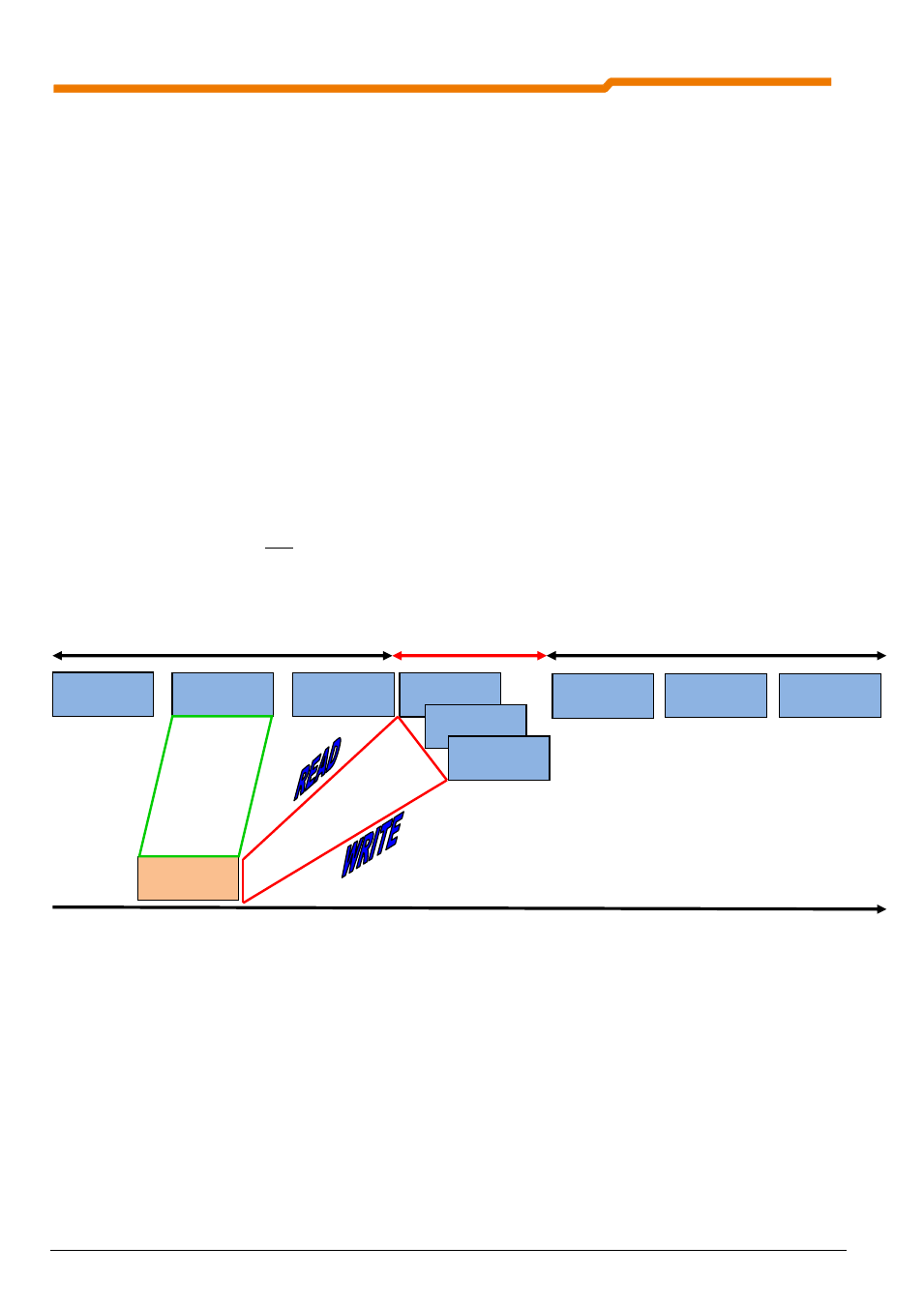
PROFIBUS DP
– Supplementary manualfor NORD Frequency Inverter SK 2xxE
90
Subject to technical amendments
BU 0220 GB-0912
8.3.4.4 Cyclic and acyclic data traffic
The PROFIBUS technology units enable field bus access to all parameters and functions of the frequency
inverter.
Cyclic reference data traffic (process data) enables rapid control of bus participants. Via the standardised
process data channel (parameter process data object (PPO)) setpoints (setpoint frequency, position setpoints,
current limits etc.) are transferred from the automation device to the frequency inverter. Via the same process
data channel, actual values (actual frequency, actual position, current values, error numbers etc.) and status
information is read back from the frequency inverter to the automation device. Selection of the PPO type is
carried out via the hardware manager (Section 4.2.2 ). The SK xU4-PBR bus module automatically detects the
PPO type which is used and sets it for communication to the frequency inverter.
However, some applications require interventions by the user (adaptation of parameters). These interventions
can be carried out
cyclically via the parameter code value channel (only PPO types 1 or 2 and only for frequency inverter
parameters) within the process data, or also
acyclically via special READ / WRITE commands according to the PROFIBUS DP-V1 specification.
Parameter adaptations of the Profibus module SK xU4-PBR (parameter (P150) ... (P154) can only be carried
out via acyclic data communication.
The acyclic data traffic is carried out parallel to the cyclic reference data traffic of the process information
during operation and can only be used for parameterisation. For the acyclic data traffic, a 4 byte data block,
which corresponds to the PKW component of PPO types 1 and 2 is transferred via the PROFIBUS DP.
The acyclic exchange of data sets can extend over several bus cycles or their "gaps".
With SIMATIC STEP 7 applications, two ready-made system modules are available for the handling of acyclic
data traffic.
parameter
PKW
Reading
and writing of
the
DP master
t
DP Slave 1
DP Slave 2
DP Slave 3
DP Slave 1
DP Slave 2
DP Slave 3
DP Slave 2
DP Slave 1
DP Slave 2
Cyclic PZD
Acyclic PKW
Cyclic PZD
Reading and
writing of the
process data
PZD
PROFIBUS DP
DP-V1