2 device types – NORD Drivesystems BU0220 User Manual
Page 85
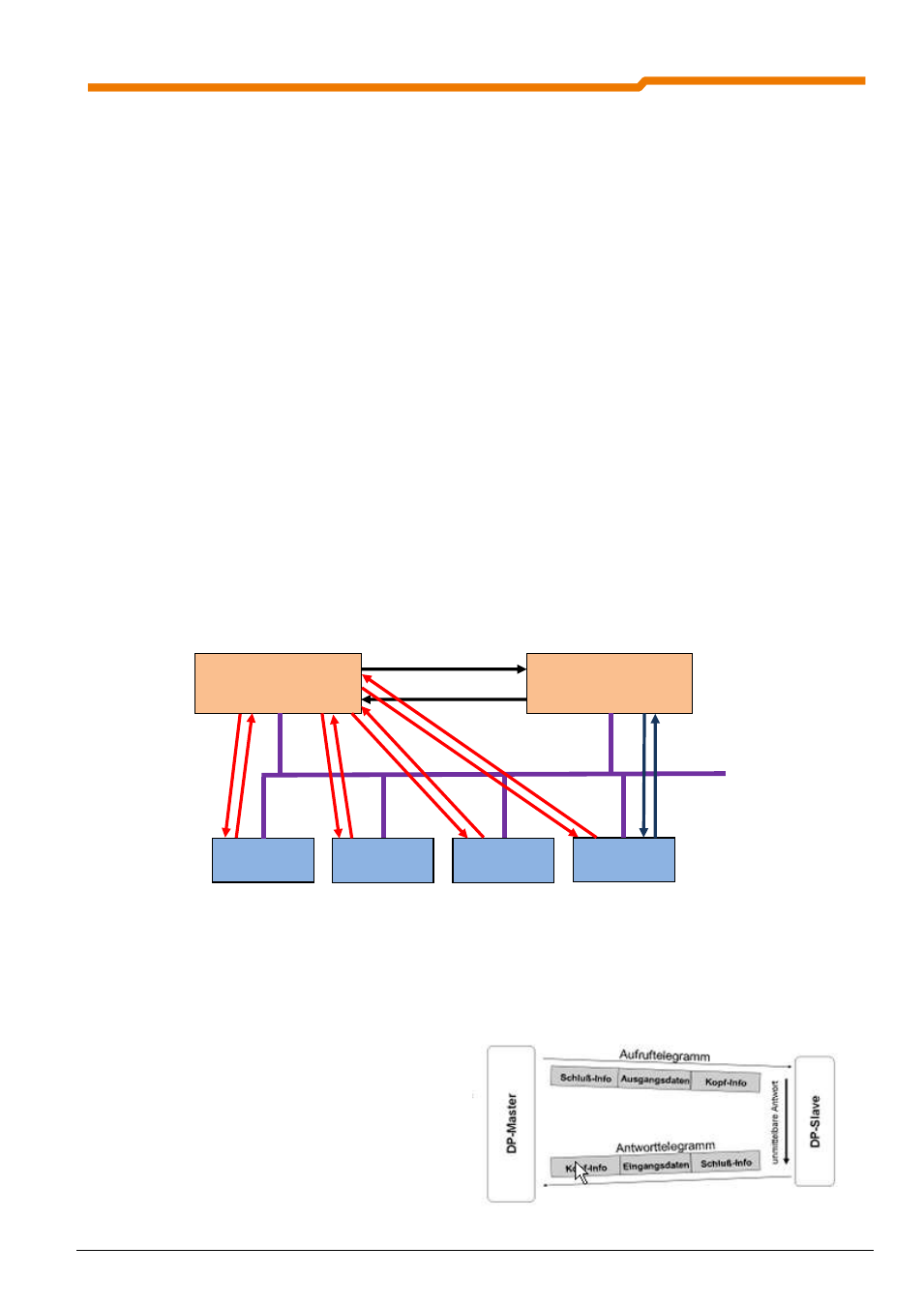
BU 0220 GB-0912
Subject to technical amendments
85
Diagram of telegram sequence
8.3.2
Device types
PROFIBUS DP is an acronym for "Process Field Bus for Decentralised Peripherals" i.e. for the simple, rapid,
cyclic and deterministic exchange of process data between a PROFIBUS DP master and the assigned
PROFIBUS DP slaves connected to the field bus. The exchange of process data takes place between central
automation devices such as PLCs, PCs or process control systems and decentralised field devices such as
drive units, valves, analysis devices and frequency inverters. Exchange of process data is mainly carried out
cyclically between the PROFIBUS DP participants (master ↔ slaves).
Each PROFIBUS DP system can consist of a wide range of different devices. These are divided into three
classes:
DP master Class 1 (DPM1)
This master controls the cyclic reference data traffic, i.e. process data is
automatically exchanged with the DP slaves (I/Os) in a repetitive
sequence. Typical devices for central control are memory-programmed
control units (PLCs) or PCs.
DP master Class 2 (DPM2)
These masters are engineering, planning or operating devices (OP,
touch-panels).
They can also access the bus acyclically and additionally enable the
configuration and parameterisation of intelligent field devices such as
frequency inverters. A DPM2 master does not need to be permanently
present on the Profibus DP.
DP Slave
Slaves are peripheral devices with a direct interface to the I/Os, such as
I/Os, drive units, valves, measurement transducers, frequency inverters
etc., which read in input information and output information to the
peripheral devices.
PROFIBUS DP is specially designed for production automation and uses the RS485 standard as the transfer
method. RS485 is the most commonly used transfer method and enables transfer rates of up to 12 MBaud. A
shielded twisted wire cable is used.
PROFIBUS DP is designed both for rapid time-critical applications as well as for complex communication
tasks.
A DP master Class 1 sends a status state (master
status) to all assigned and connected slaves in a
cyclic time interval which can be configured. If the
operating parameter "Auto Clear" is set to "TRUE",
the DPM1 master switches the outputs of all
associated slaves to the safe condition, i.e. to "0"
in case of failure of a slave.
DP Slave 1
DP Slave 2
DP Slave 3
PROFIBUS
DP master Class 1
PROFIBUS
DP master Class 2
Token
DP Slave 4