3 performance levels – NORD Drivesystems BU0220 User Manual
Page 87
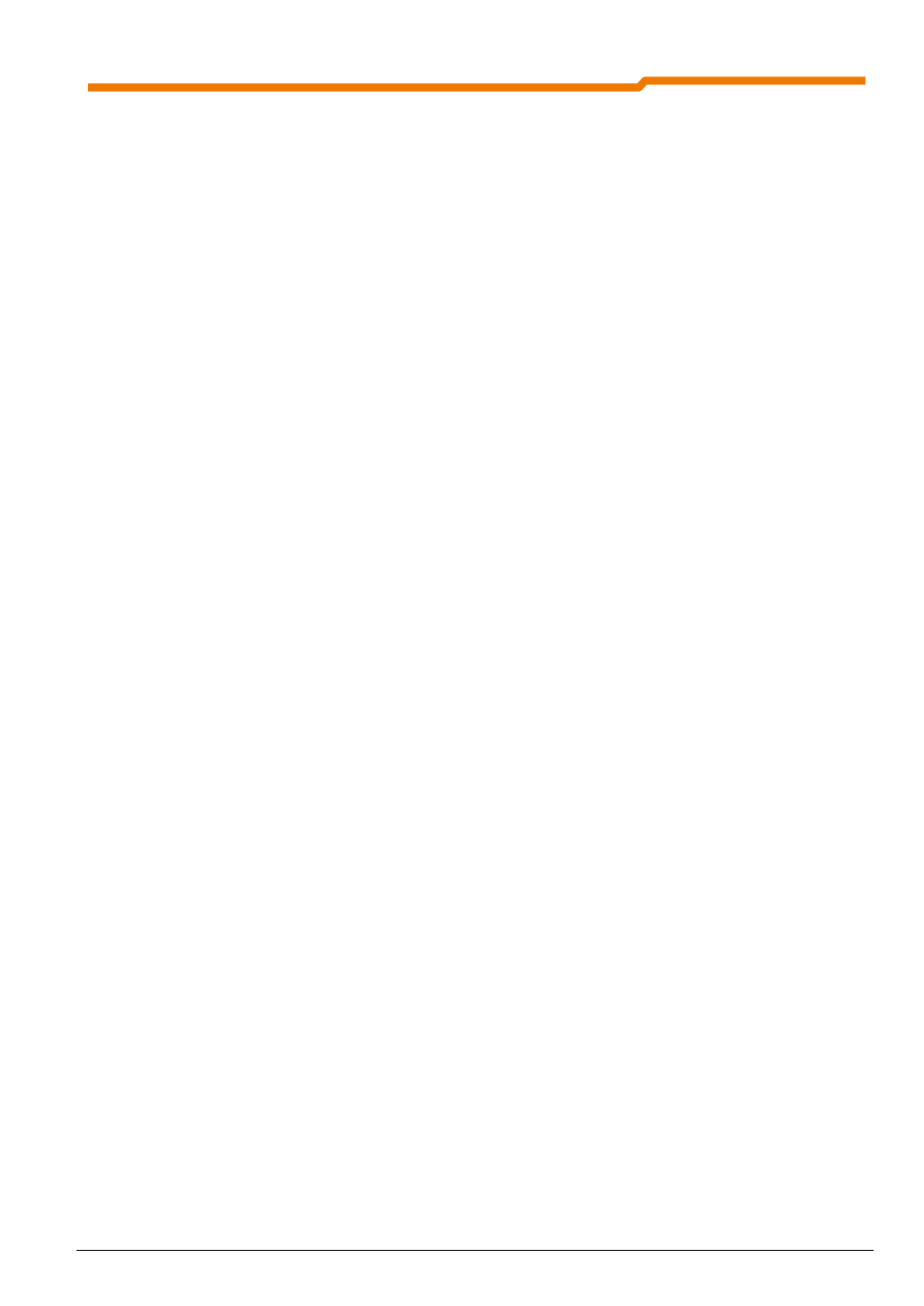
BU 0220 GB-0912
Subject to technical amendments
87
8.3.2.2 PROFIBUS slave
PROFIBUS DP slaves are peripheral devices such as I/Os, drive units, HMIs, valves, measurement
transponders, frequency inverters. The DP slaves do not receive any access rights, i.e. they can only confirm
messages from the master or send messages to the master when requested. DP slaves are designated as
passive participants. A slave reads in input information and sends out output information to the peripherals.
Because a slave only requires a small portion of the protocol, they are simple to implement in the PROFIBUS
system configuration. The amount of input and output information depends on the device and can be up to a
maximum of 246 input and 246 output bytes.
All data which a PROFIBUS master requires for the exchange of data (e.g. I/O area) with the slave and its
implementation is provided by means of a DeviceMasterFile (
GSD file) which is specific to the particular
manufacturer.
The slaves are decentrally coupled to the PLC control unit or the automation device via the transfer medium
(PROFIBUS cable and RS485) and complete the configuration of the system.
8.3.3
Performance levels
PROFIBUS DP defines 3 performance levels (basic functions).
DP-V0
Basic functionalities for cyclic data traffic
DP-V1
Extensions for acyclic data traffic
DP-V2
Special extensions and additions for data traffic between slaves
Getriebebau NORD GmbH supports the PROFIBUS DP performance levels DP-V0 and DP-V1.
8.3.3.1 PROFIBUS DP-V0
DP-V0 describes the basic functionalities of the DP communication protocol.
Cyclic exchange of process data / transfer of reference data between the DP master and slave(s)
Diagnosis specific to the station, module and channel
Telegram format:
PPO types 1 - 4
Device classes:
DPM1, DPM2 and slave
Access times*:
Reading access (parameter queries)
- approx. 30ms
Writing access (parameter changes)
- approx. 50ms
* for 1 - 4 frequency inverters for each BUS technology unit
Parameterisation is possible with the use of PPO types 1 and 2
Note:
The bus cycle time must be less than the program cycle time of the central automation device.
Data traffic between the DPM1 and the slaves is structured into the parameterisation, configuration and data
transfer phases.