Load connection method i, local error sensing -5 – KEPCO ATE-DMG SERIES User Manual
Page 39
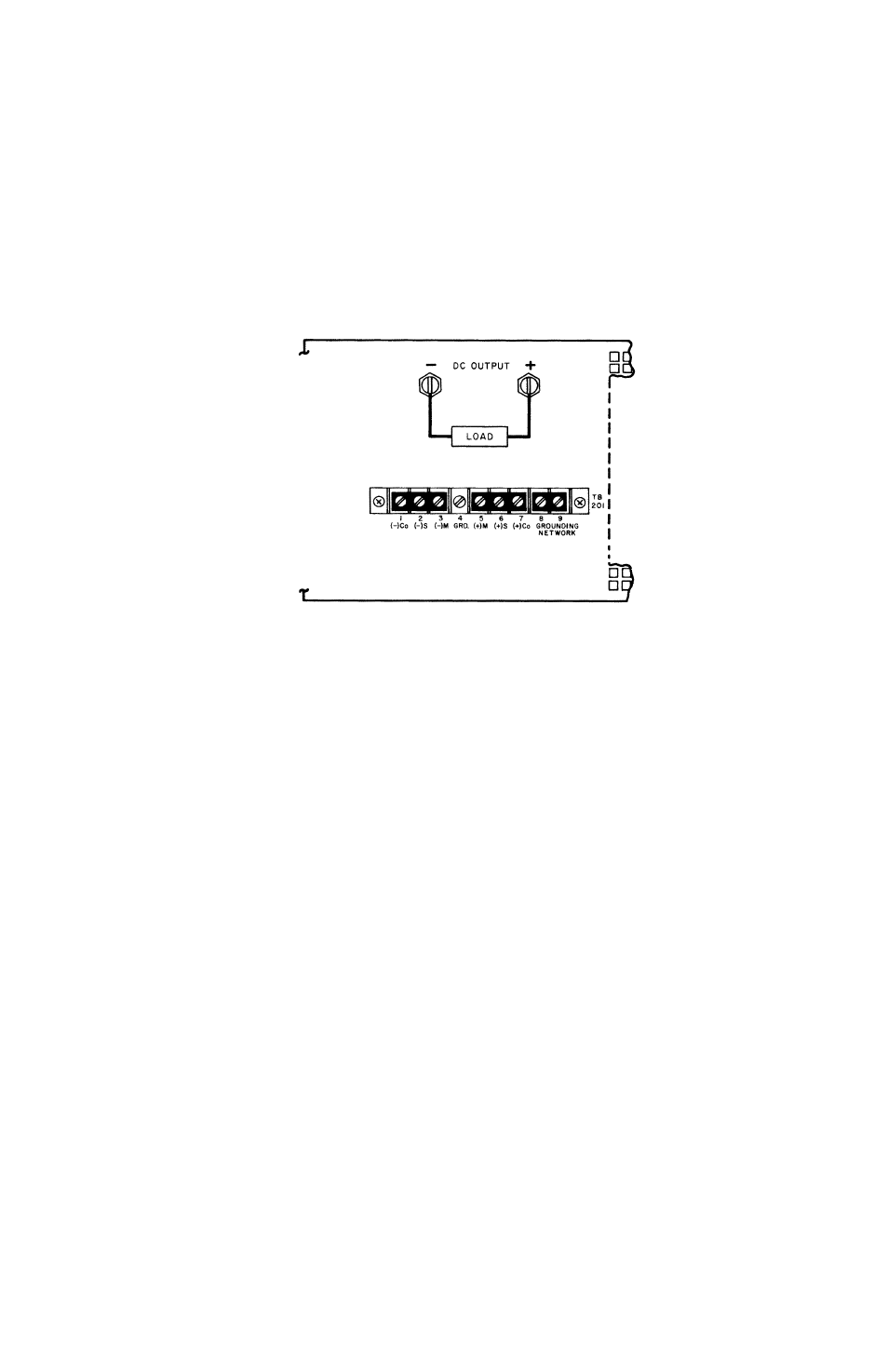
ATE-DMG 042314
3-5
FIGURE 3-3. LOAD CONNECTION METHOD I, LOCAL ERROR SENSING
3.2.3
LOAD CONNECTION, METHOD II (REMOTE ERROR SENSING)
To avoid excessive output effects at remote loads, error sensing must be used. A twisted,
shielded pair of wire from the sensing terminals directly to the load will compensate for load wire
voltage drops up to 0.5 volt per wire (refer to Figure 3-4). Observe polarities: The negative sens-
ing wire must go to the negative load wire, and the positive sensing wire goes to the positive
load wire.
NOTE: For long wire runs, twisting each sensing wire with its associated load wire may give
improved results in some cases.
ATTENTION
When using remote error sensing with large capacitive Ioads and long
Ioad and sensing wires, low frequency oscillations may be observed at
the Ioad. To eliminate the problem the FEEDBACK CAPACITOR should
be disconnected from the (–) OUTPUT SENSING terminal and recon-
nected to the (–) OUTPUT MONITOR terminal. Remove jumper (1)-(2) on
the REAR PROGRAMMING CONNECTOR. Connect a short wire from
pin 2 to the REAR BARRIER-STRIP (TR201-3).
This method of load interconnection is suitable for loads which do not require rapid changes in
voltage or current, or for programming with gradually changing waveforms (sine wave, triangular
wave shapes, etc.). See PAR. 3.2.4 for load connections suitable for rapid (step) changes in the
load or in programming.