2 advanced diagnostics, 1 multi-sensing process monitoring, 2 impulse line blockage detection (ilbd) – Yokogawa EJX440A User Manual
Page 42: Advanced diagnostics -2 4.2.1, Multi-sensing process monitoring -2, Impulse line blockage detection (ilbd) -2, Important
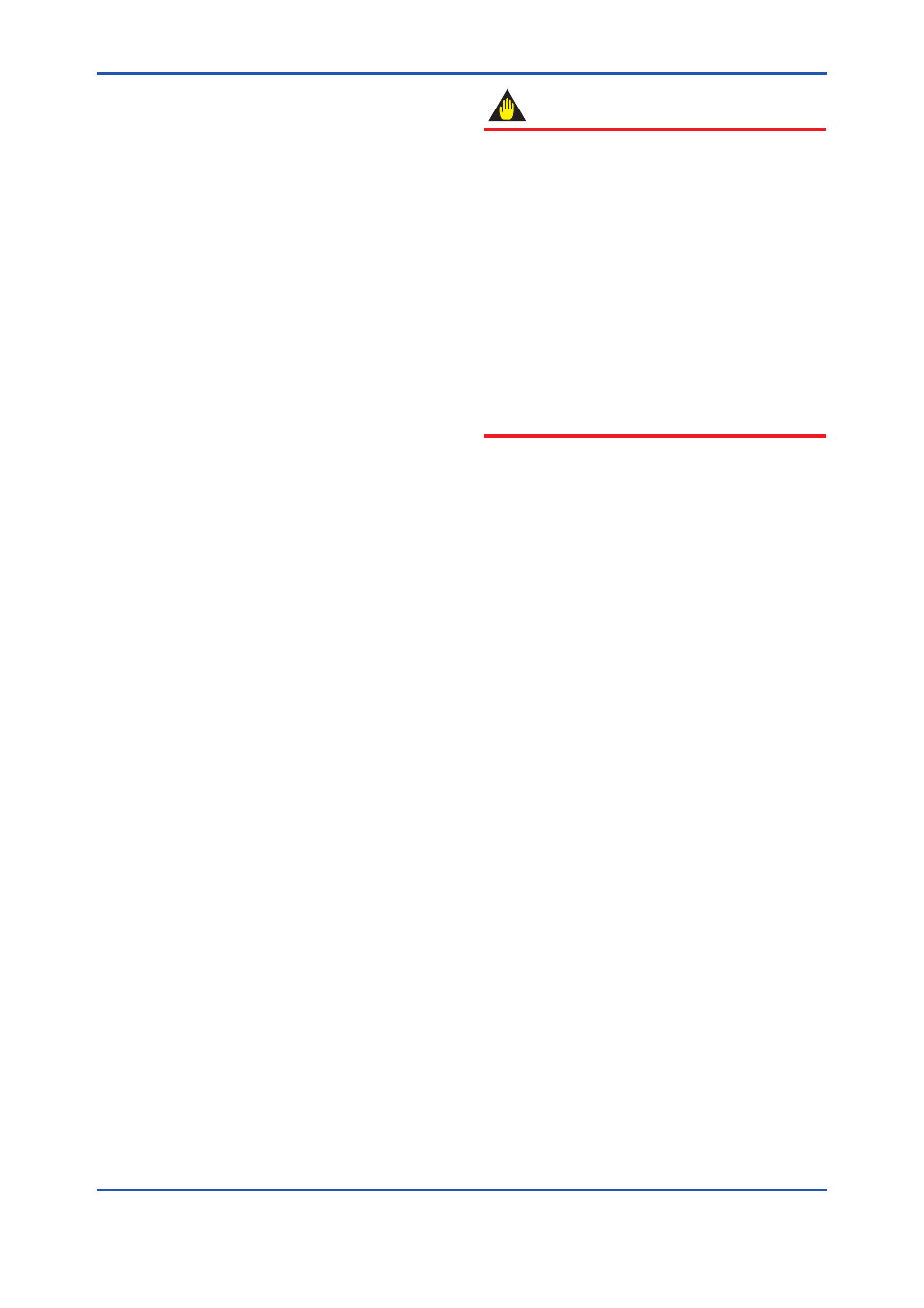
<4. Diagnostics>
4-2
IM 01C25T01-01E
4.2 Advanced Diagnostics
4.2.1 Multi-sensing Process Monitoring
Multi-sensing process monitoring function (option
code: /DG6) provides the advanced diagnostics
to detect the abnormal conditions in process
environment such as an impulse line etc. by using
the EJX multisensing technology and its unique
algorithm. There are following two functions.
Impulse Line Blockage Detection (ILBD)
The fluctuation change of differential pressure and
static pressure is monitored by a silicone resonant
sensor and detects a potential blockage condition.
The differential pressure transmitter gives also a
result of which pressure-side was plugged.
Heat Trace Monitoring
The two temperature sensors built in the EJX
calculate the flange temperature, the change of
which enables to detect the heat trace breakage or
the abnormal temperature due to the failure.
4.2.2 Impulse Line Blockage Detection
(ILBD)
ILBD is carried out by using statistical analysis
based on the measured values of process
fluctuations that exist in a fluid. An alarm on the
EJX LCD display or an analog alert is generated if
blockage reaches a certain level. EJX provides the
following results as blockage detection.
(1) A Blocking and B Blocking
These are blockage detections based on
the fluctuation value change of differential
pressure/pressure. With a differential pressure
transmitter, each result indicates that both or
single side is plugged.
(2) L Side Blocking
It is a low-pressure side blockage detection
based on the change of
BlkF or low-pressure-
side fluctuation value.
(3) H Side Blocking
It is a high-pressure side blockage detection
based on the change of
BlkF or high-pressure-
side fluctuation
*:
BlkF indicates blockage degree characterized
by a comparison of the high- and low-pressure-
side fluctuation values. For the details, refer to
Figure 4.2.2.
IMPORTANT
• The pressure fluctuation amplitude in fluids
must be sufficiently large for blockages to be
detected.
• If the pressure fluctuation amplitude is too
low for a reference value to be obtained,
blockages detection operation cannot be
performed with an alarm that the reference
value is invalid.
• The pressure fluctuation amplitude may
decrease due to other causes unrelated with
a blockage according to process condition. In
above case, a false alarm of an impulse line
blockage may be generated. Before taking
action in response to a blockage alarm,
consider the plant operating conditions.
Notes for Pressure or Level
Measurement
With pressure or level measurement, the pressure
fluctuation amplitude may reduce especially for the
following cases.
Pressure Measurement
• Operational pressure is near outside of
diagnostic range.
• Even though pressure is constant, the flow
decreases than that under normal condition.
• A source of pressure fluctuation (pump,
compressor, blower, etc.) is shut down. As
a result, the pressure fluctuation amplitude
decreases.
Level Measurement
• A transmitter is used to measure tank level and
the flow of fluid into or out of the tank comes to
a stop.
• The agitator in the tank is shut down.
• A source of pressure variation (a compressor,
etc.) that controls the internal pressure of a
sealed (closed) tank is shut down.
Before taking action in response to a blockage
alarm, consider the plant operating conditions.