Watlow MINICHEF 2000 User Manual
Page 42
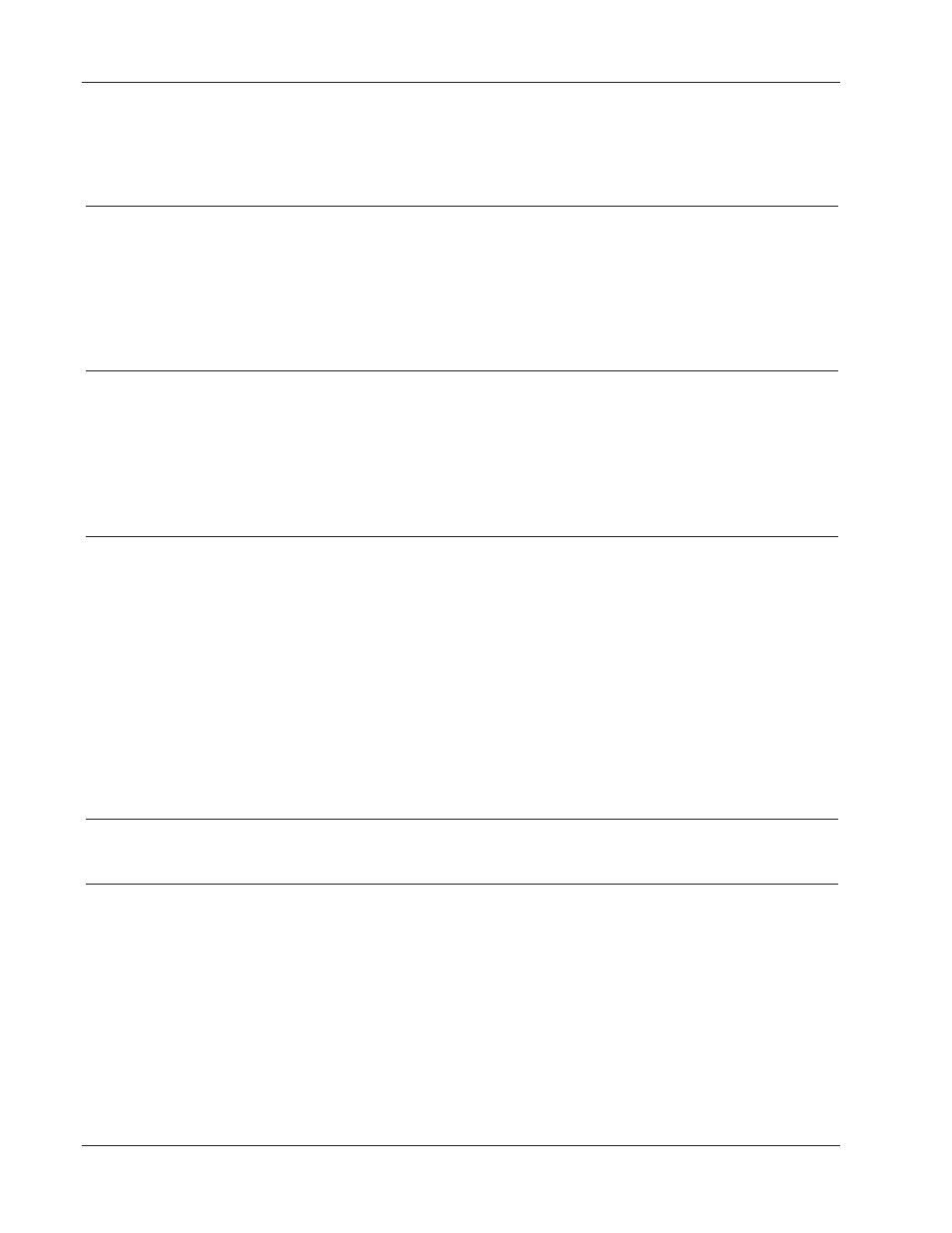
H a r d w a r e & S o f t w a r e S e t u p G u i d e
Wa t l o w M
I N I
C
H E F
2 0 0 0
■
4 1
Tr o u b l e s h o o t i n g C h a r t
• Confirm that the controller configu-
ration has the Battery/Real-time
Clock feature. Part number format
is F2HA - _ _ _ _ - 1 _ _ _ (a “1” in
the ninth character).
• Reprogram the controller, setting
the [PLOSS] parameter to [``YES].
• If problem persists, return controller
to factory.
• Controller configuration does not
have Battery/Real-time Clock fea-
ture.
• The Power Loss Menu Resume fea-
ture is not activated.
• Battery is low or needs replace-
ment.
Menus cycles don’t resume
(continue) after power
returns to the controller.
Power Loss Menu Resume
feature doesn’t seem to
work.
• Disable the Key Chirp feature by
setting the [ChirP] parameter to
[``OFF].
•The Key Chirp feature is activated.
• Controller beeps every
time a key is pressed.
If controller part number format is
F2XX-XXXX-X1XX
(a “1” in the tenth character) and if
the [ChirP] parameter is set to
[```on]:
• If keys don’t beep, return controller
to factory.
If no audible alarm occurs at the end
of a Menu cycle, and if [Sound]
parameter is set to a number other
than [````0]:
• return the controller to the factory.
If controller part number format is
F2HA - _ _ _ _ - _0 _ _
(a “0” in the tenth character), consult
factory.
• Specified system does not have an
audible alarm output or the audible
alarm is defective.
• The Key Chirp feature is not acti-
vated.
• The [Sound] parameter value is
set to [````0].
Controller does not beep:
• when keys are pressed.
• at the end of Menu cycles.
• Contact factory to replace faceplate
overlay to avoid contamination of
controller electronics. If overlay is
damaged, take extreme care when
cleaning area around controller. Do
not wash, wipe, or spray damaged
area with liquid cleansers.
• Refer to Faceplate Overlay design
guidelines.
• Faceplate overlay not designed or
installed properly.
Faceplate Overlay is dam-
aged or cracked. Edges
are lifting up.
• Ensure proper mounting of con-
troller.
• If Menu key is inoperative, verify
that a time greater than zero is pro-
grammed into the Menu program
for that key.
• Refer to the programming guide.
Consult factory.
• Return to factory.
• Misalignment of controller to metal
faceplate.
• Menu key is inactive due to pro-
grammed menu time set to zero.
• Operator error.
• Defective key switch.
Keys inoperative or hard to
press.
Possible Solutions
Possible Causes
Symptom/Indication