Pid control block (pid) – Micromod MOD: 1800P - MOD 30ML Identity Module (Version 2) PID and Ramp/Soak Functions User Manual
Page 8
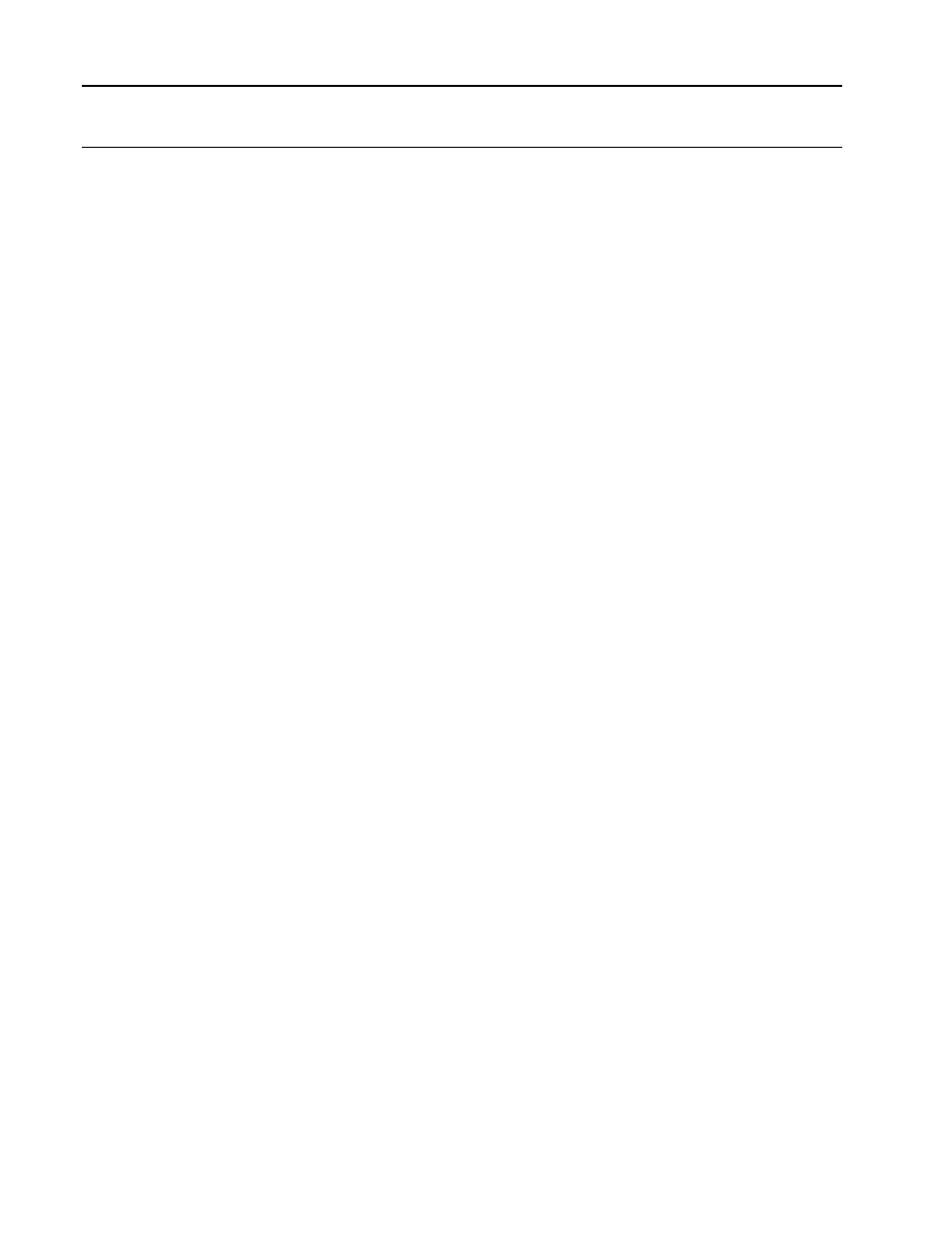
Continuous Control Functions
PID CONTROL BLOCK
2-2
2.2
PID CONTROL BLOCK (PID)
Regulatory control is supported through use of the PID Control block. The basic functions of
each PID block include:
•
Basic PID Control (Gain, Reset, Pre-Act) algorithms. Variations are:
♦
Pre-Act on Process or Error
♦
Proportional on Process or Error
♦
Standard or MICRO-SCAN Integral
•
Setpoint and Output (Controller ) Modes, including Tracking
•
Setpoint and Output Limiting
•
Local or Remote Setpoint with ratio and bias
•
Manual Reset and Procedureless Manual Reset
•
Feedforward Input (compensation model provided external to PID block)
•
Deadtime Compensation Input (algorithm may be constructed in Expression Block)
•
External
Feedback
•
Gain, Reset and Pre-Act modifier Inputs (externally generated)
•
Auto, Manual or Cascade controllers
•
Output and Remote Setpoint High, Low, Center Input Selection
•
Configurable Power Restart Values
The number of PID Control blocks capable of running in an instrument depends upon the
specific configuration. One possible configuration could include six to eight PID Control blocks
running at a rate of about 350 ms. The PID algorithm runs at a multiple of the task rate in
which it is executed. Setpoint processing is independent of the PID algorithm and occurs
every execution cycle.
The controller mode can be represented as a separate output and setpoint mode, or singly as
a controller mode model. If a controller mode is configured, the output mode and setpoint
modes are derived from the controller mode and cannot be written to specifically.
When a track input signal is asserted, the mode is set to TRACK, and the track value is copied
to the output. If setpoint track is enabled, the setpoint mode is set to TRACK and the setpoint
TRACK value is copied to the active setpoint value.
Within the PID routine, setpoint processing occurs independently from the PID calculation,
with the result being the determination of the active setpoint value that is then used in the PID
calculation. If the setpoint mode is LOCAL, the user sets the active setpoint. When the
setpoint mode is REMOTE, the active setpoint is the remote setpoint value multiplied by the
ratio and added to the bias. The adjusted setpoint is calculated by subtracting the bias from
the active setpoint and dividing the result by the ratio.
Block inputs, outputs and database items are shown in the overview diagram, Figure 2-1. A
functional block diagram of a PID Control block is shown in Figure 2-2 (3 pages). The menus
used to configure the PID Control block are shown in Figure 2-3 (page 1), Figure 2-4 (page 2),
Figure 2-5 (page 3) and Figure 2-6 (page 4).