Micromod MOD: 1800P - MOD 30ML Identity Module (Version 2) PID and Ramp/Soak Functions User Manual
Page 16
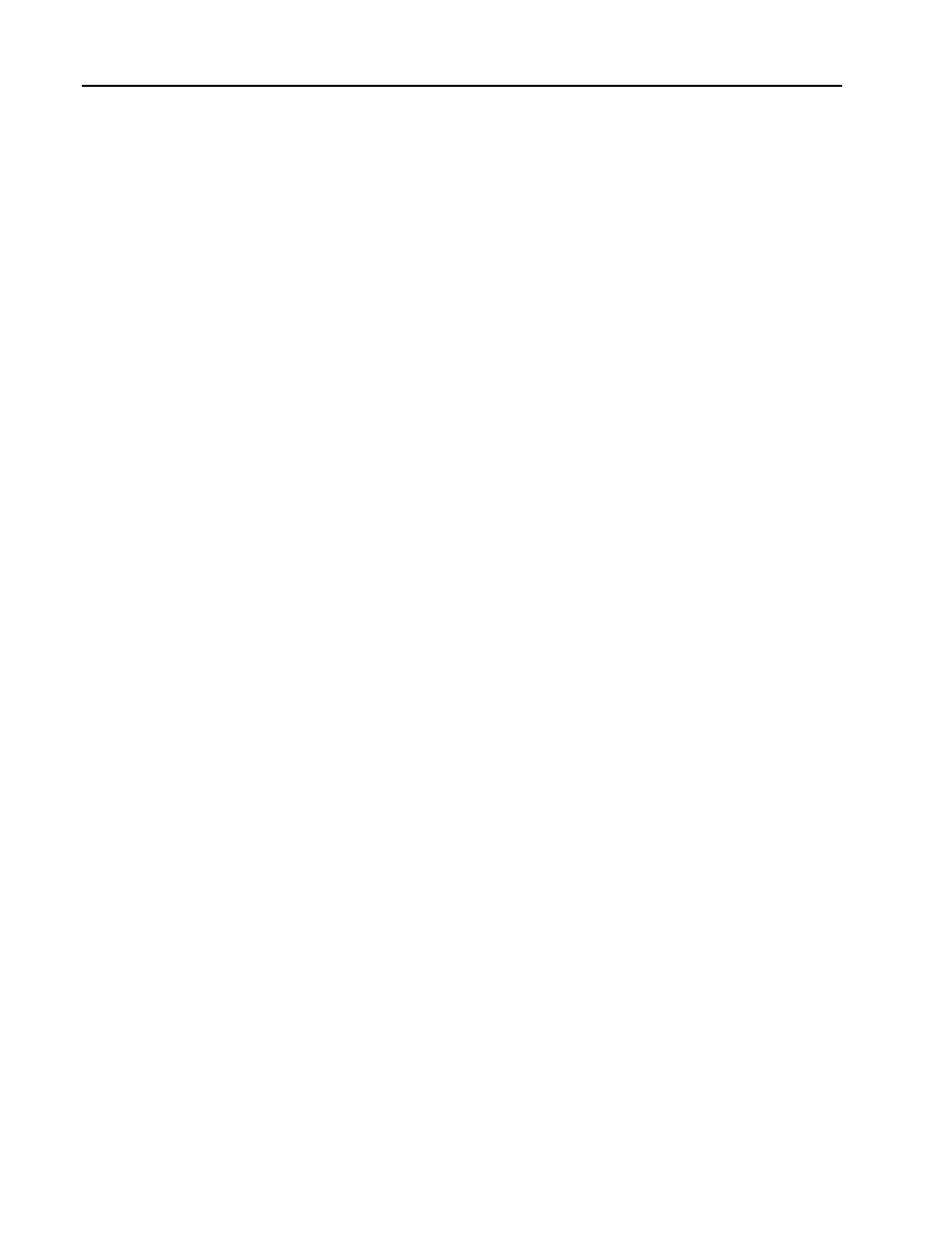
Continuous Control Functions
PID CONTROL BLOCK
2-10
Setpoint high/low limits and output high/low limits cannot be written such that the limit
values invert; that is, the high value cannot be set less than the low value.
Quality Checks
If the track command input quality is bad (Bad Inputs Accepted = NO), the PID block is unable
to determine what mode it should be in. It therefore sets the output mode (and controller
mode, if configured) to FAULT. If setpoint tracking is enabled, the setpoint mode is set to
FAULT.
For the purpose of discussing data quality exceptions and how the PID block is affected, PID
block processing can be considered as two separate parts: setpoint processing and PID
algorithm processing.
For setpoint processing, the inputs of concern are remote ratio, remote bias, and remote
setpoint. The generated outputs are the active setpoint, adjusted setpoint, bias and ratio. If
remote ratio and/or bias sources are configured, the output ratio/bias values are copies of the
input values, and the output qualities reflect the input qualities for these values. Otherwise,
the values for ratio or bias are calculated by the PID block (as a result of the configured
setpoint balancing) and the qualities reflect the success of calculating those values (i.e., if a
calculation error occurs when the auto balance values are calculated and the set qualities bad
on calculation error attribute is TRUE, then the quality of the balance value is set BAD).
If the setpoint mode is remote, and the remote setpoint, bias or ratio qualities are bad, then
the active setpoint and adjusted setpoint qualities are set bad. If the setpoint mode is FAULT,
all setpoint processing outputs are set bad.
If the setpoint mode is LOCAL, the active setpoint quality is GOOD and the adjusted setpoint
quality is set to the worst quality of the ratio and bias values. If the setpoint mode is TRACK,
the action is as described above.
For PID processing, the inputs of concern are the process value, dead time compensation
value, gain, reset and preact modifiers, manual reset value, feedforward value, external
feedback value, and the active setpoint (calculated by setpoint processing). The generated
outputs are the calculated PID output and the track status.
If the mode (controller or output) of the block is TRACK or MANUAL, the output qualities
(output and track status) are set to GOOD. If the mode is FAULT, the output qualities are set
BAD.
If the mode is AUTO or CASCADE, then the process value and active setpoint qualities must
be GOOD. If a dead time compensation input, and/or external feedback input are configured,
their qualities must be GOOD. If a feedforward input value is configured and the feedforward
type is ADD or MULT, the input quality must be GOOD. Manual reset, gain, reset and preact
input qualities must be good if these inputs are configured and the algorithm type specifies
that they are used (e.g., the preact modifier has no affect on PID calculation if the algorithm
type specifies derivative = OFF). If all of these conditions are met, the PID calculation is
performed and if no calculation error occurs, the outputs are set GOOD.