Micromod MOD: 1800P - MOD 30ML Identity Module (Version 2) PID and Ramp/Soak Functions User Manual
Page 27
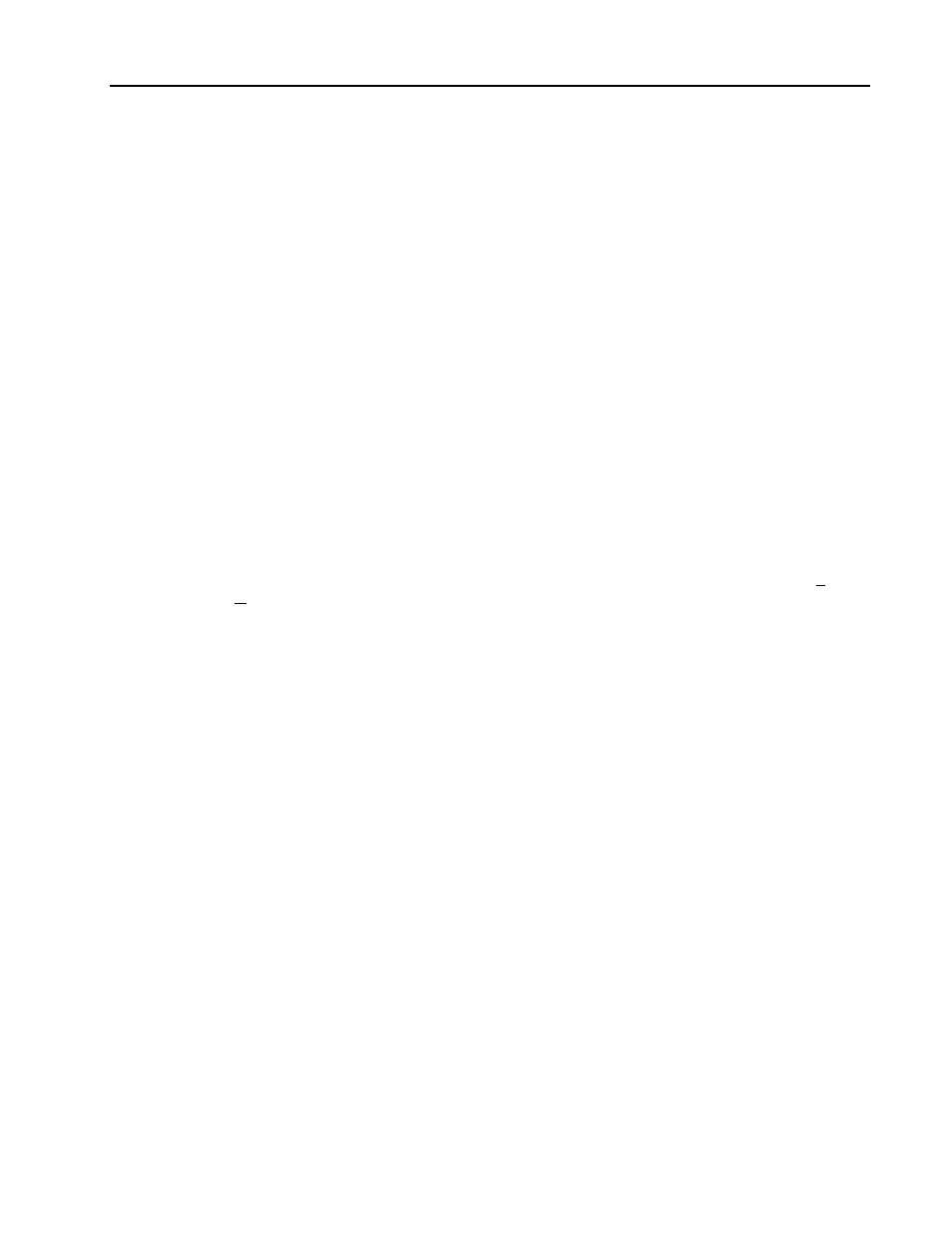
Continuous Control Functions
PID CONTROL BLOCK
2-21
38
Deviation (DEV)................................................................................................................CWR
This is the normalized deviation output (process input minus active setpoint).
39
Deviation Quality (DEVQ)................................................................................................. – WR
Deviation quality is based on the process and setpoint qualities.
GOOD
0
Quality when the process and setpoint qualities are good.
BAD
1
Quality when the process or setpoint qualities are bad.
40
Output Modes Allowed (OPMA) ...................................................................................... C – R
The output modes allowed count value determines what output modes are allowed.
M
1
Manual output only is allowed.
A
2
Auto output only is allowed.
M.A
3
Also A.M. Auto or manual output is allowed.
41
Output Mode Status, Initial Value (OPMS) ......................................................................CWR
This is the actual controller output mode. The output mode cannot be written to if the mode
model is controller mode. On a transition to mode model CTRL MODE, output mode is set to
MANUAL by the configurator. See Mode Model for a description of output mode changes due
controller mode changes. Output modes other than manual and auto are not configurable or
writeable.
Bumpless transfer is inherent in the PID control algorithm that has reset enabled (i.e. ESPO,
EMPO). To make the auto output match the manual output, the algorithm automatically
adjusts the reset register. If you are using a proportional only controller, reset will be OFF and
the manual reset type should be set to Procedureless to have the same effect.
If you are using two PID Control blocks in a cascade configuration, bumpless transfer between
the two must be configured using tracking.
MANUAL
0
Output mode is manual.
AUTO
1
Output mode is auto.
TRACK
3
Output mode is track. This read only value indicates that track
command is true.
FAULT
5
Output mode is fault. This read only value indicates that the PID
block is unable to determine what mode it should be in (because the
track command input quality is bad).
42
Output Mode Status Quality (OPMSQ) ........................................................................... – WR
The output mode status quality is good when all input qualities are good and no calculation
error occurs.
GOOD
0
Quality is good when the block is RUN or HOLD.
BAD
1
Quality when the block is OFF.
43
Output Mode Command (OPMC) .....................................................................................– – R
The output mode command is the value to which output mode will be set when TRACK clears.
If you are in Track and want to return to a control mode other than the value indicated here,
you must write to the Controller Mode (CMS) whose value will then be reflected here.
MANUAL
0
Output mode set to MANUAL when TRACK clears.
AUTO
1
Output mode set to AUTO when TRACK clears.