Diagnostics and troubleshooting, Diagnostics and troubleshooting overview, Error messages – Liquid Controls LCR 600 Setup & Op User Manual
Page 54
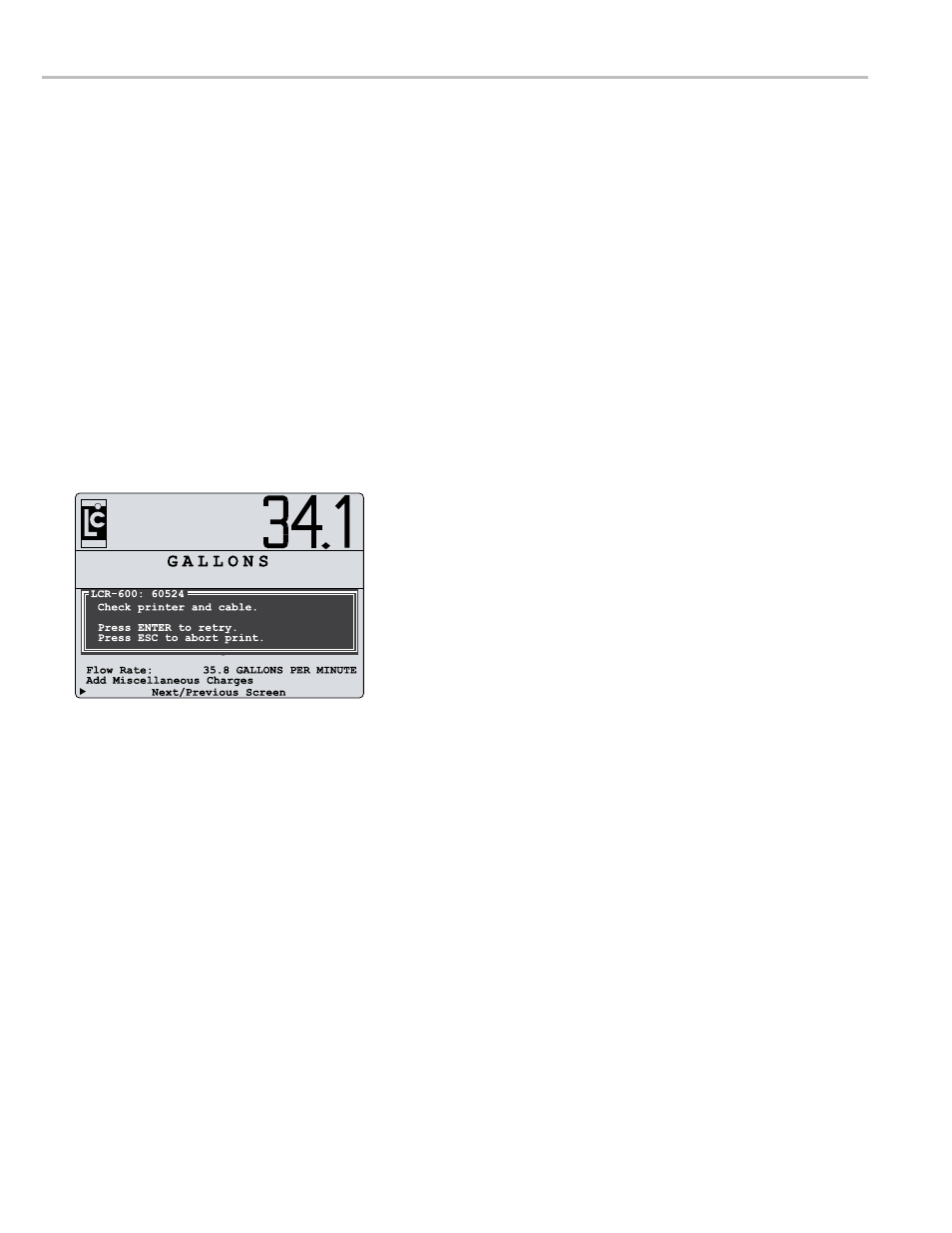
54
dIagnoStIcS and troubleShootIng
diagnostics and troubleshooting overview
The LCR 600 provides tools for diagnosing and troubleshooting itself as well as other aspects of the meter system.
The three main diagnostic tools are error messages, diagnostic and status screens, and diagnostic tickets. Error
messages will pop up on the LCR 600 when the register can not continue its current function without an adjustment
in the current settings. The diagnostic and status screens provide a detailed account of the status of the LCR 600.
Diagnostic tickets provide a rundown of calibration data, system identification information, temperature probe data,
error messages, and other useful bits of information. These three tools can help you pinpoint any issues occurring
within the system and the LCR 600 and maintain an accurate, efficient, and safe fluid measurement system.
error messages
The LCR 600 identifies entry errors and system errors as soon as they occur. When an error occurs, a shaded box
with a short description of the error will appear on the display. The error might also include additional instructions or
options. If necessary, the additional options will give you the opportunity to open the diagnostic screens. In many error
cases, you will also want to print a diagnostic ticket (see page 63). The list below explains LCR 600’s error messages
and possible corrective actions. If the suggestions listed are not successful, consult the troubleshooting section. If the
troubleshooting tips do not help, call an authorized Liquid Controls service provider.
delIvery error meSSageS
These messages may be displayed when the LCR 600 is attempting to start, in the midst, or finishing a delivery.
delivery ticket pending
A new delivery was attempted but the previous delivery ticket was not
printed in its entirety. Turn the selector switch to the PRINT position.
Once the previous delivery ticket is printed, a new delivery can begin.
Check printer and cable
The printer is not responding. The most common cause is no ticket in
the printer. Epson slip printers have a built in photo eye to detect if a
ticket is in position. Other causes include faulty data cable or power
cable and LCR 600 circuit board failure.
ROM CHeCKSUM eRROR
The program memory space of the LCR 600 has been corrupted. If
this error occurs, the unit must be reflashed with the control software
before any deliveries can be made. Flash instructions are available on
the www.lcmeter.com website.
TeMPeRATURe eRROR
The temperature circuit returned an error or the temperature calibration data is in error. Check the temperature probe
and its connections. A broken temperature probe wire is the most common cause of this error. See the troubleshooting
section for more information (see page 65).
VCF dOMAIN eRROR
The calculated temperature falls outside the allowable range for the current compensation parameter. Verify that the
product compensation type is correct on the Calibration Setup 2 screen (See page 35).
PULSeR FAILURe
The number of pulser faults exceeds the allowable amount. Pulser faults typically occur in high vibration environments
or when the flow rate is highly throttled. The LCR 600 allows a maximum of five times the number of pulses required
for the least significant displayed digit or 0.1% of the pulses generated for the current delivery. This equation can
not be altered. Liquid Controls is not responsible for pulser failures caused by excessive system vibrations. See the
troubleshooting section for more information (see page 66).
MeTeR CALIB eRROR
The product selected for delivery has not been calibrated. Select a calibrated product.