2 design and method of operation, 1 overview, Design and method of operation – Siemens SIPART PS2 6DR52xx User Manual
Page 15
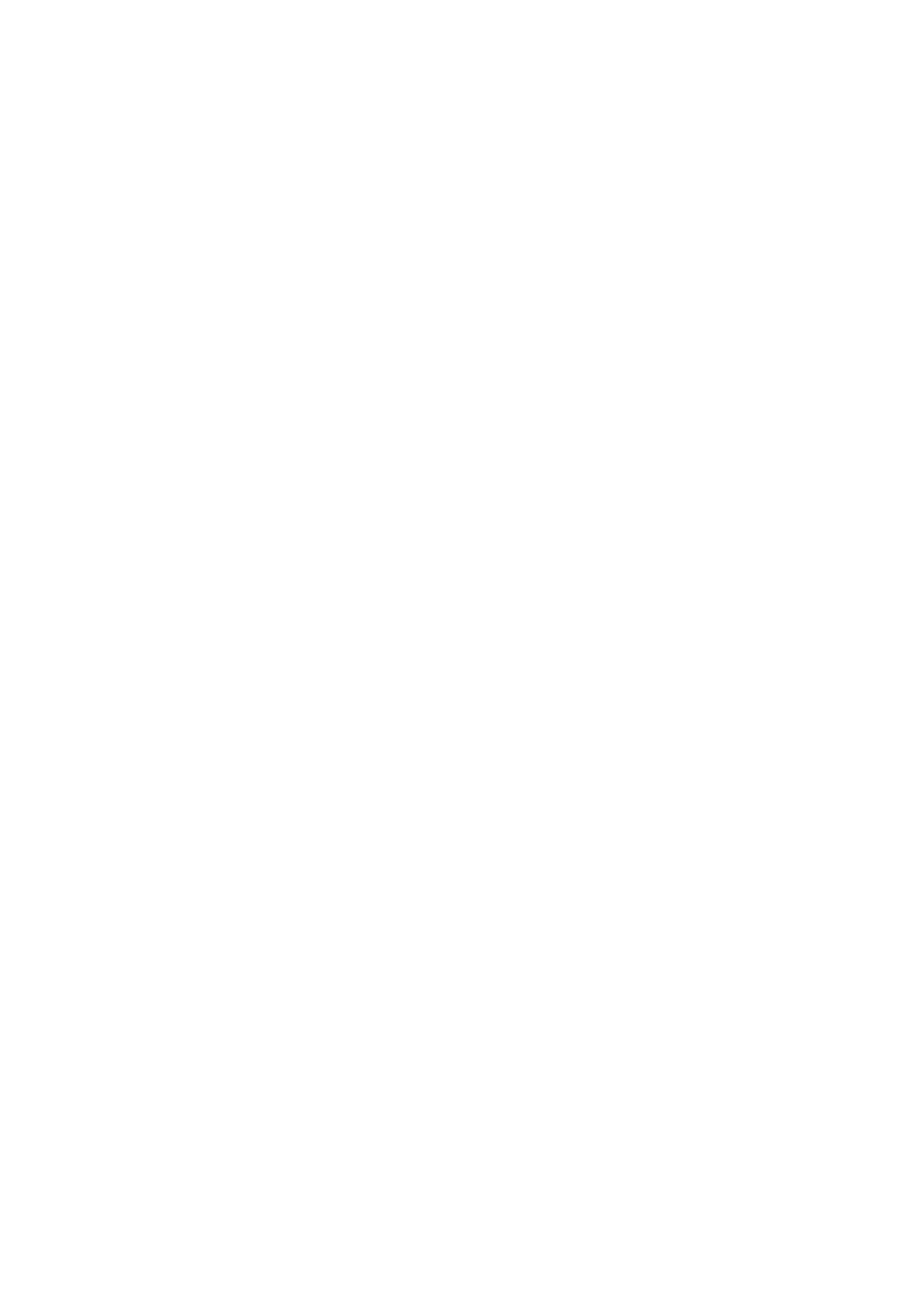
Design and Functional Principle
15
SIPART PS2 Manual
A5E00074631--06
Design and Method of Operation
The following chapter describes the mechanical and electrical design,
the instrument components and method of operation of the positioner.
2.1 Overview
The electropneumatic positioner forms a control system in connection
with an actuator. The current position of the actuator is detected by a
servo potentiometer and fed back as actual value x. The setpoint and
actual value are output simultaneously on the display.
The setpoint w is formed by a current fed to the positioner which at
the same time serves to supply the positioner in two-wire operation.
In 3/4-wire operation the supply comes from a 24 V voltage input.
The positioner operates as a predictive five-point switch by the output
variable ±∆y of which the integrated actuating valves are controlled with
pulse length modulation.
These actuating signals cause fluctuations in pressure in the actuator
chamber(s) and thus adjustment of the actuator until the control error is
zero.
Operation (manual) and configuration (structuring, initialization and
parameterization) is effected by three keys and a display with the hous-
ing cover removed.
The standard controller has one digital input (DI1). This can be config-
ured individually and can be used for blocking the operating modes for
example.
With the I
y
-option module, the current actuator position can be output
as a two wire signal I
y
= 4 to 20 mA.
In addition the actuator can be monitored for two programmable limit
values which respond on exceeding or dropping below the stroke or
angle of rotation.
The limit value alarms are output by the alarm option module which can
monitor and report the function of the positioner and the actuator addi-
tionally through a fault message output. The value of the control differ-
ence dependent on the travel time is monitored in automatic mode. The
fault signal is always set when the control error cannot be leveled after
a certain time because for example the valve is blocked or the mains
pressure is insufficient. The three digital outputs are implemented as
semiconductor outputs and are error self-reporting, i.e. the outputs re-
Introduction
2