Cycle parameters – HEIDENHAIN TNC 620 (340 56x-02) Cycle programming User Manual
Page 148
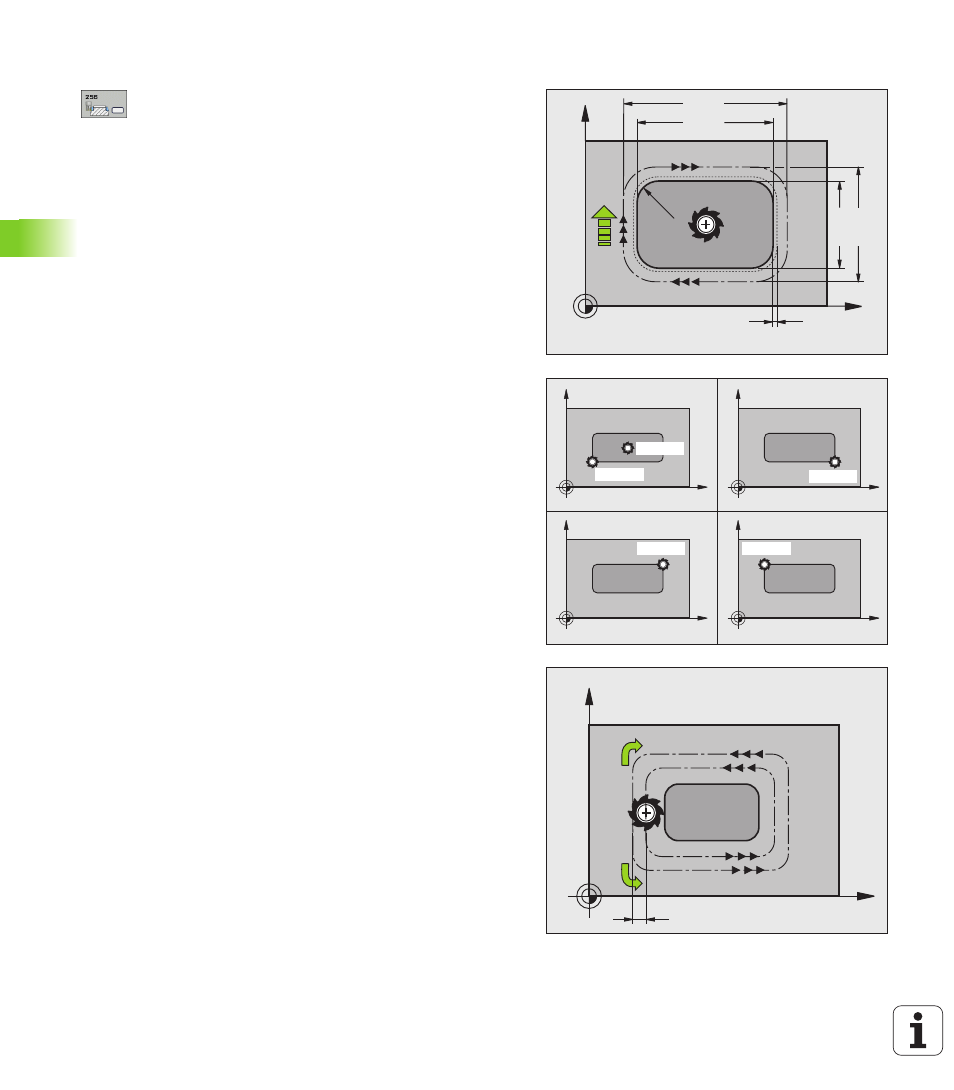
148
Fixed Cycles: Pocket Milling / Stud Milling / Slot Milling
5.6 RECT
ANGULAR S
T
UD (C
y
c
le 256, DIN/ISO: G256, A
d
v
a
nced Pr
ogr
a
mming
F
e
at
ur
es Sof
tw
a
re
Option)
Cycle parameters
U
First side length Q218: Stud length, parallel to the
reference axis of the working plane. Input range 0 to
99999.9999
U
Workpiece blank side length 1 Q424: Length of the
stud blank, parallel to the reference axis of the
working plane. Enter Workpiece blank side length 1
greater than First side length. The TNC performs
multiple stepovers if the difference between blank
dimension 1 and finished dimension 1 is greater than
the permitted stepover (tool radius multiplied by path
overlap Q370). The TNC always calculates a constant
stepover. Input range 0 to 99999.9999
U
Second side length Q219: Stud length, parallel to
the minor axis of the working plane. Enter
Workpiece blank side length 2 greater than
Second side length. The TNC performs multiple
stepovers if the difference between blank dimension
2 and finished dimension 2 is greater than the
permitted stepover (tool radius multiplied by path
overlap Q370). The TNC always calculates a constant
stepover. Input range 0 to 99999.9999
U
Workpiece blank side length 2 Q425: Length of the
stud blank, parallel to the minor axis of the working
plane. Input range 0 to 99999.9999
U
Corner radius Q220: Radius of the stud corner. Input
range 0 to 99999.9999
U
Finishing allowance for side Q368 (incremental):
Finishing allowance in the working plane, is left over
after machining. Input range 0 to 99999.9999
U
Angle of rotation Q224 (absolute): Angle by which
the entire stud is rotated. The center of rotation is the
position at which the tool is located when the cycle is
called. Input range -360.000 to 360.000
U
Stud position Q367: Position of the stud in reference
to the position of the tool when the cycle is called:
0: Tool position = Center of stud
1: Tool position = Lower left corner
2: Tool position = Lower right corner
3: Tool position = Upper right corner
4: Tool position = Upper left corner
X
Y
Q21
9
Q218
Q368
Q220
Q207
Q424
Q425
X
Y
X
Y
X
Y
X
Y
Q367=0
Q367=1
Q367=2
Q367=3
Q367=4
X
Y
k
Q351= 1
Q351= +1