Dillon Precision XL 650 User Manual
Page 44
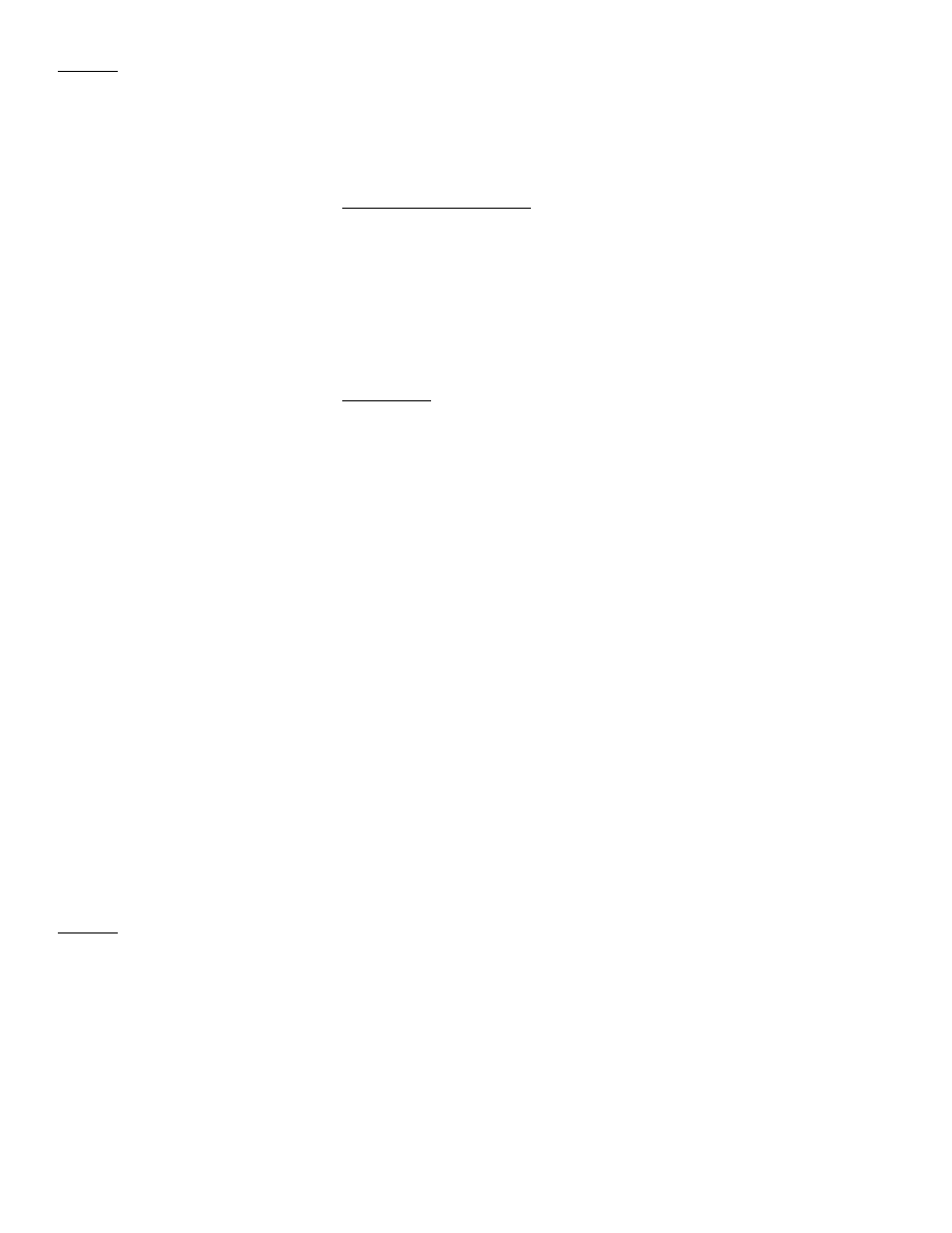
Station 4 - Bullet Seating
A. Erratic seating depth of the bullet.
1. Variations of less than 20 thou-
sandths of an inch are due to varia-
tions in cases and bullets. This is not
a problem.
2. Build up of lead shavings and/or lube
in the seater or crimp dies.
3. Bullets having erratic dimension
(length and/or the ogive).
4. Use of improper seating plug for the
type of bullet being used.
5. Variations in case types and/or lots
(sort your brass).
6. Refer to loading manual for dimen-
sions.
B. Shaving brass when bullet is seated or
crescent shaped brass falling on
shellplate.
1. New brass.
2. Too much flare.
C. Shaving lead/lube when bullet is seated.
1. Case not belled enough with funnel.
2. Case was cleaned too long. Case
mouth must be deburred.
3. Wrong bullet diameter for caliber.
D. Bullet loose in brass.
1. Bullet is under sized.
a. Measure diameter of bullets.
2. Incorrect powder funnel, i.e., if the
funnel is too big it will make the
mouth of the case oversized.
3. Too much crimp.
E. Bullet tilted after seating.
1. Case not belled enough.
2. Wrong seating stem or die for bullet
style or caliber.
3. Missing or wrong locator buttons, i.e.,
case not centered below the die.
4. Uneven casemouth opening.
5. Using a nominally incorrect bullet.
i.e., .38/357 bullet in .38 Super.
6. Die and stem not square to shellplate.
a. Snug lockring with case and bul-
let in die.
F. Seating die deforming top of bullet.
1. Seating stem not matching that style
of bullet.
2. Soft lead.
3. Lead and/or wax build-up in die.
4. Case not belled enough.
Station 5 - Crimp
A. Erratic crimping.
1. Variation in case length. Probably
due to mixed brands of brass.
2. Dirty or worn out crimp die. Use
Dillon dies where available.
B. Loose bullet.
1. Too much taper crimp. This condition
can also affect accuracy.
2. Wrong expander.
3. Thin cases. (Use Dillon dies and this
won’t be a problem.)
4. Wrong crimp die.
C. Too much or too little crimp on complet-
ed round.
1. Crimp die adjusted too low or too
high. See manual for maximum crimp
dimensions. If not available, crimp to
20 thousandths below case diameter.
2. Using wrong crimp die for that case.
3. Not using full stroke of handle.
4. Over flared case.
5. Variations in case length.
Ejecting Finished Cartridges
A. Rounds not ejecting after Station 5.
1. Ejector wire (13298) bent, broken or
missing.
2. Wrong locator buttons.
3. Shellplate damaged from decap pin.
B. Finished cartridges do not make it into
the catch bin.
1. Operating handle too fast.
2. Chute/bin mount is bent.
3. Bin is missing or improperly located.
Maintenance
Lubrication: Operating circumstances will
dictate the frequency of required lubrica-
tion. It is highly recommended that the XL
650 be cleaned and lubed after every 3000
rounds of operation. Use oil or wheel bear-
ing grease. Never use penetrating lubri-
cants, aerosol sprays, or solvent type lubes,
such as WD-40 or Break Free.
Lubrication Points:
Shellplate bolt – Grease.
Main Shaft Lubrication –
Use only 30 wt. motor oil. Once again, do
not use penetrating lubricants, aerosol
sprays, or solvent type lubricants.
45