B&C Technologies DI-325 Industrial User Manual
Page 12
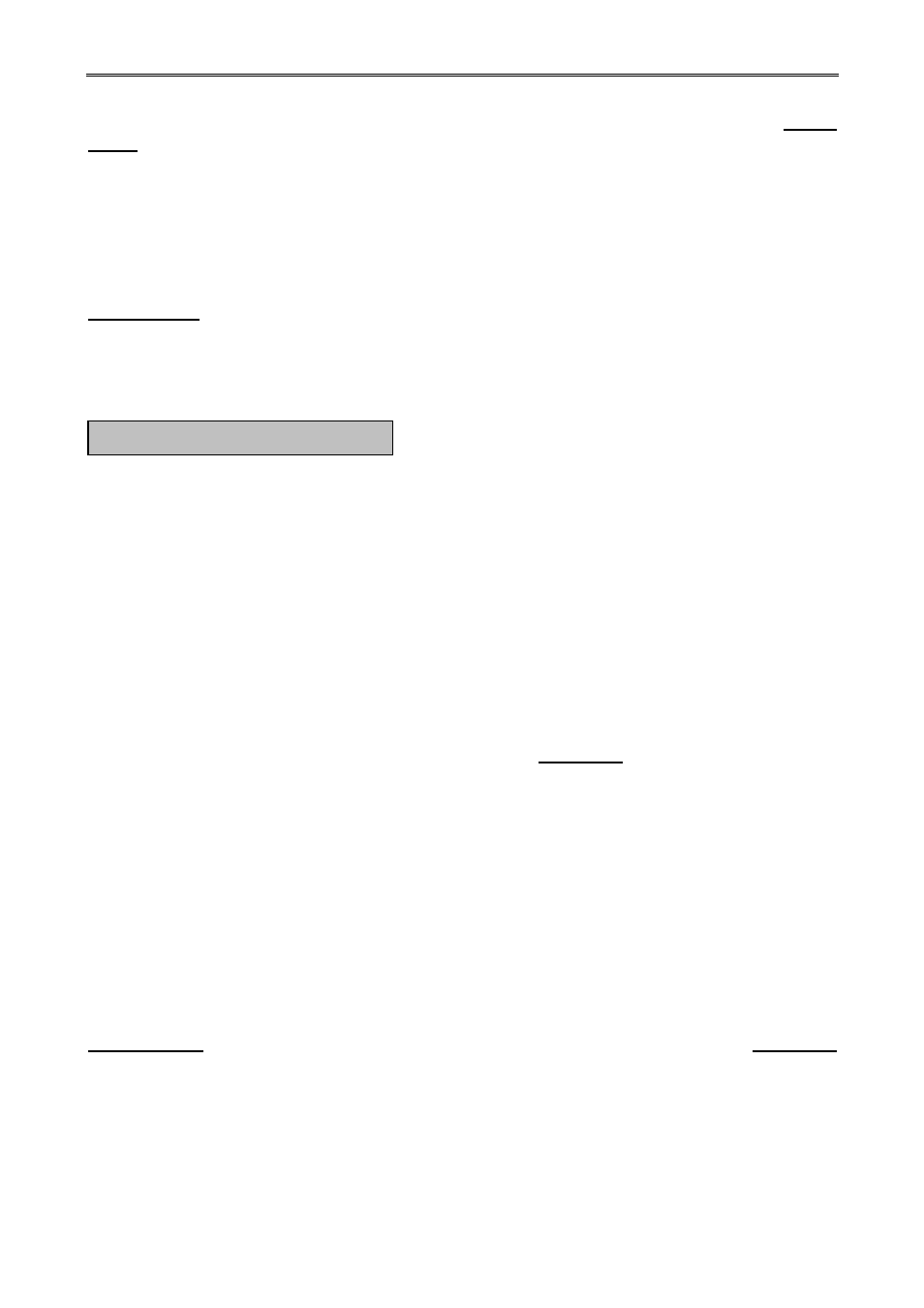
INSTALLATION PROCEDURES
3-3
To compensate for the use of registers or louver used over the opening, this make – up air
area must be increased by approximately thirty – three (33) percent. Make – up air openings should
not be located in an area directly near where exhaust vents exit the building.
It is not necessary to have a separate make – up air opening for each dryer. Common make
up air openings are acceptable. However, they must be set up in such a manner that the make – up
air is distributed equally to all the dryers.
Allowances must be made for remote or constricting passageways or where dryers are
located at excessive altitudes or predominantly low pressure areas.
IMPORTING: Make – up air must be provided from a source free of dry cleaning solvent
fumes. Make-up air that is contaminated by dry cleaning solvent fumes will result
in irreparable damage to motors and other dryer components.
NOTE:
Component failure due to dry cleaning solvent fumes VOIDS WARRANTY.
General Exhaust Duct Work Information
Exhaust duct work should be designed and installed by a qualified professional. Improperly
sized duct work will create excessive back pressure which results in slow drying, increased use of
energy, over – heating of the dryer, and shut down of the burner by the airflow (sail) switches,
burner hi – limits, or basket (tumbler) hi – heat thermostats.
The duct work should be laid out in such a way that the duct work travels as directly as
possible to the outdoors with as few turns as possible. Single or independent dryer venting is
recommended.
The internal dimensions of the dryer’s rectangular exhaust vent work are 12 inches by 20
inches (30.5 cm. × 50.8 cm.). The plant’s exhaust duct must be at least 20 inches (50.8 cm) in
diameter of for a rectangular duct has cross sectional areas of 315 square inches (1,549 sq. cm.).
The duct work from the dryer to the outside exhaust outlet should not exceed thirty (30) feet. The
shape of the duct work is not critical so long as the minimum cross sectional area is provided. It is
suggested that the use of 90
o
turns in ducting be avoided use 45º angles instead. The radius of the
elbows should preferably be 1 – 1/2 times the width or diameter of the duct. Excluding basket /
dryer elbow connections used for outside protection from the weather, no more than two (2) elbows
should be used in the exhaust duct run. If more than two (2) elbows are used, the cross section area
of the duct work must be increased.
All duct work should be smooth inside with no projections from sheet metal screws or other
obstruction which will collect lint. When adding ducts, the duct to be added should overlap the duct
to which it is to be connected. All duct work joints must be taped to prevent moisture and lint from
escaping into the building. Inspection doors should be installed at strategic points in the exhaust
duct work for periodic inspection and clean out of lint from the duct work.
IMPORTANT: Exhaust back pressure measured by a manometer in the exhaust duct should not
exceed 0.3 inches of water column.
NOTE:
Where the exhaust duct work passes through a wall, ceiling or roof made of
combustible materials, the opening must be 2 inches larger (all the way around)
than the duct. The duct must be centered within this opening.
D. EXHAUST REQUIREMENTS