Non-critical vs. critical module errors, Module error definition table – Rockwell Automation 1769-OF2 Compact I/O Analog Modules User Manual
Page 122
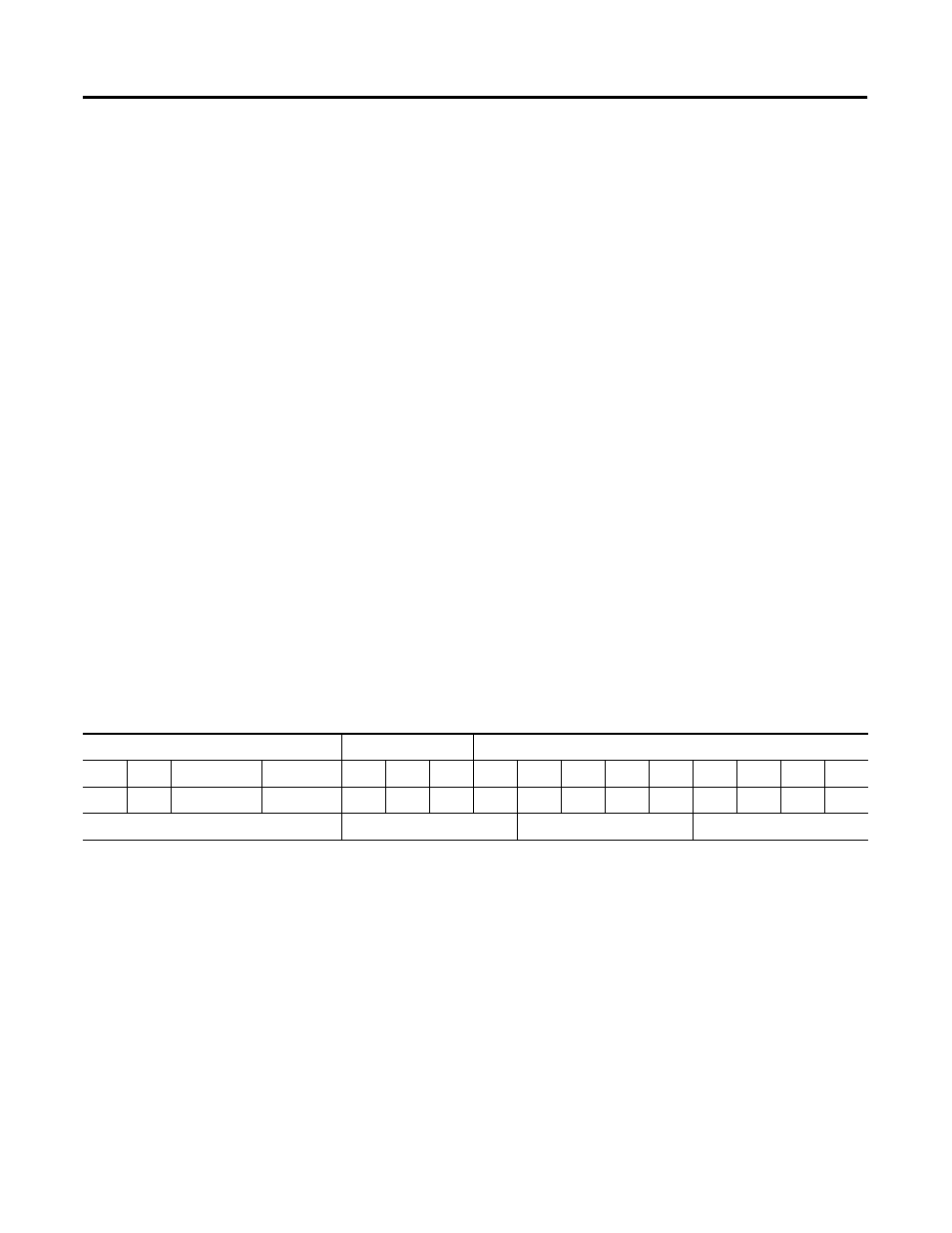
Publication 1769-UM002B-EN-P - July 2005
5-4 Module Diagnostics and Troubleshooting
Output Wire Broken/High Load Resistance (Output Modules Only)
A check is performed on all enabled channels to determine if an output wire is
broken, or if the load resistance is high, in the case of current mode outputs.
Whenever one of these conditions is present, the diagnostic bit for that
channel is set in the Input Data file.
Non-critical vs. Critical
Module Errors
Non-critical module errors are typically recoverable. Channel errors
(over-range or under-range errors) are non-critical. Non-critical error
conditions are indicated in the module input data table. Non-critical
configuration errors are indicated by the extended error code. See Table 5.4
1769-IF4 and -OF2 Extended Error Codes on page 5-6.
Critical module errors are conditions that prevent normal or recoverable
operation of the system. When these types of errors occur, the system typically
leaves the run or program mode of operation until the error can be dealt with.
Critical module errors are indicated in Table 5.4 1769-IF4 and -OF2 Extended
Error Codes on page 5-6.
Module Error Definition
Table
Analog module errors are expressed in two fields as four-digit Hex format with
the most significant digit as “don’t care” and irrelevant. The two fields are
“Module Error” and “Extended Error Information”. The structure of the
module error data is shown below.
Table 5.2 Module Error Table
“Don’t Care” Bits
Module Error
Extended Error Information
15
14
13
12
11
10
9
8
7
6
5
4
3
2
1
0
0
0
0
0
0
0
0
0
0
0
0
0
0
0
0
0
Hex Digit 4
Hex Digit 3
Hex Digit 2
Hex Digit 1