Enerpac PL200-Series User Manual
Page 14
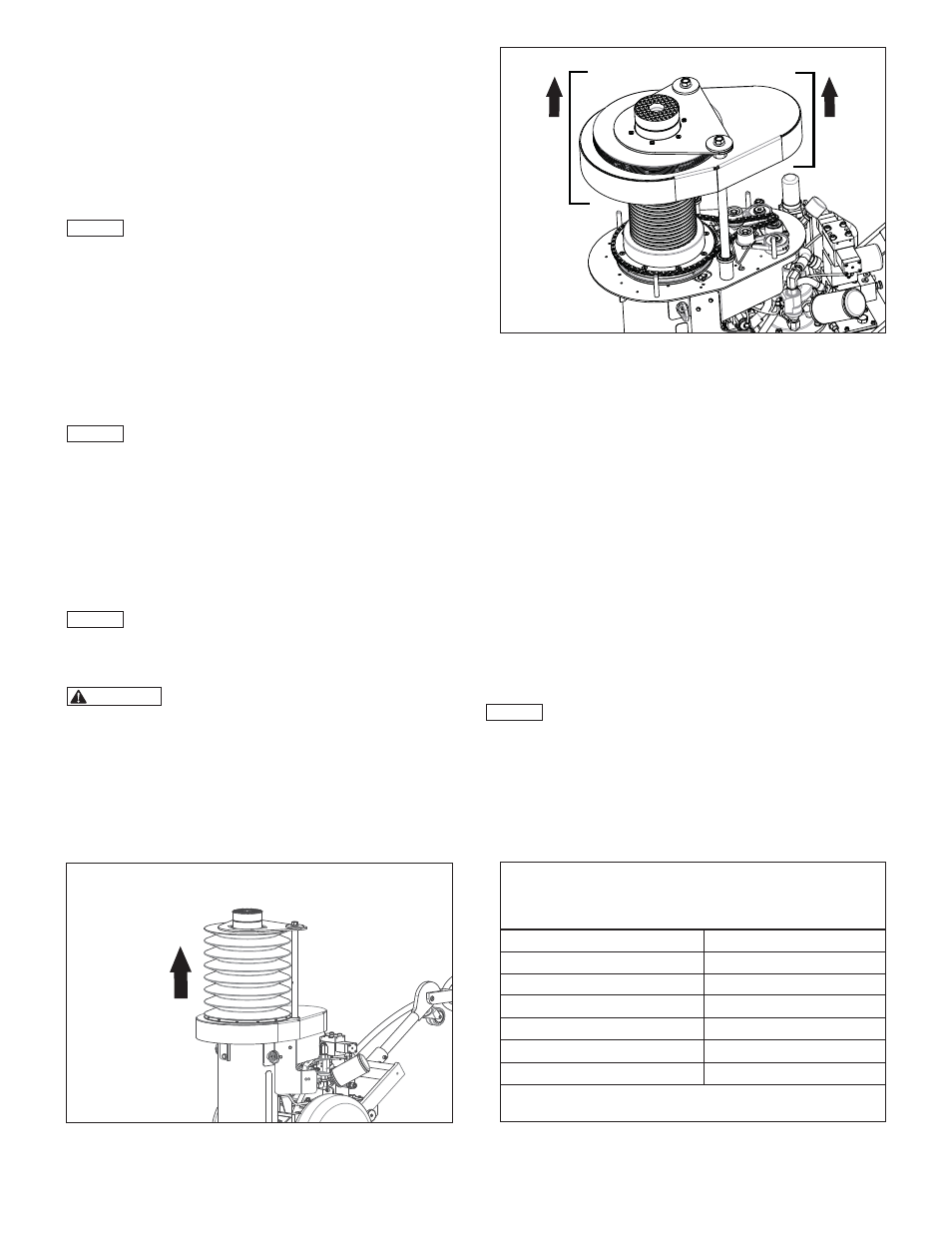
14
7.9 Lubrication of Cylinder Threads and Lock Nut
Chain Drive (See Figures 16-19)
The cylinder threads and lock nut drive chain should be lubricated
approximately every 30 hours of operation. Both lubrication
activities can be performed at the same time, as described in the
following steps:
1. Be sure there is no load on the jack.
2. Unhook the rubber latches and remove the jack rear access
cover. See Section 7.1 for procedure.
NOTICE
Before performing lubrication procedures, the cylinder
must be fully extended and the jack pneumatic system must be
depressurized. Follow instructions in steps 3a-3f.
3.
Fully extend the cylinder and depressurize the jack pneumatic
system:
a. Depress and hold the pendant UP button to raise the
cylinder. Continue holding the button until the cylinder is
fully extended and the jack air motor stops running. See
Figure 16.
b. Move the jack air-shutoff valve to the CLOSED position.
c. Disconnect air supply hose at jack air-shutoff valve.
NOTICE
Jack may start and run briefl y in the following step, as
trapped air is expelled from the jack pneumatic system.
d. Depress and hold the pendant UP or DOWN button.
Continue holding button until jack air motor stops running.
Motor will usually stop after about 2 to 6 seconds, depending
on length of air supply hose.
e. Verify that there is no audible “air hiss” sound coming
from the jack.
f. Check the air pressure gauge on the jack fi lter/lubricator.
Verify that it indicates zero (0) psi/bar.
NOTICE
If any pressure is indicated on gauge, be certain that
air-shutoff valve is in the CLOSED position and that air hose is
disconnected from air shut-off valve. Then, repeat steps 2d
through 2f.
WARNING
Be certain that air supply hose is disconnected
and that air regulator pressure gauge indicates zero (0) psi/
bar before continuing with this procedure. Jack will start
immediately if air pressure is indicated on gauge, and either
pendant button is depressed. Lock nut and chain will begin
turning. Serious personal injury could occur if jack is started
while persons are performing lubrication procedures.
4. Raise the jack front access cover so that the cylinder threads
are exposed as much as possible. See Figure 17.
Figure 16, Fully Extending the Cylinder
Figure 17, Lifting Front Access Cover to Expose Threads
5. Attach a lifting sling to the front access cover. Wrap the sling
around the anti-rotation plate and load cap, so that the cover
is held in the raised position. Be certain that the sling is strong
enough to support the weight of the cover (approximately 15
lbs [5,6 kg] ) and that it is securely fastened.
6. Perform the following inspection and lubrication tasks. See
Figure 18.
• Remove any loose dirt or debris from the chain drive
assembly.
• Check each chain tensioner to verify that it is applying
fi rm spring tension against the chain. If the tensioner does
not move freely, or if spring tension is weak, it should be
replaced. The tensioners are not adjustable or repairable.
• Check the tensioner rollers for obvious indications of wear
or damage. Replace rollers as required. The rollers are
available as a separate replacement part.
• Check all teeth on the lock nut and drive sprockets for
obvious indications of wear or damage. Replace these
parts as required.
NOTICE
Refer to Table 9 for gear oil specifi cations.
• Apply a fi lm of SAE 80w-90 gear oil [ISO 150] to the links
of the lock nut drive chain.
• At each tensioner, apply a small amount of 80w-90 gear
oil [ISO 68] to the exposed areas of the tensioner pivot
bushing, located under the tensioner retaining nut. Some
of the oil will fl ow past the bushing and onto the tensioner
pivot shaft. Removal of nut is not required.
Table 9 - Gear Oil Specifi cations - SAE 80w-90 [ISO 150]
(Use for lubricating cylinder threads, lock nut drive
chain, sprockets and tensioner pivot shaft.)
SAE Grade
80w-90
ISO Grade
150
Viscosity Index
103
Viscosity at 40
°
C, cSt
136
Viscosity at 100
°cSt
14.5
Flash Point.
°
C
202
Pour Point,
°
F
-30
NOTICE: Specifi cations shown in this table are typical. Exact
specifi cations may diff er slightly, depending on oil brand.