Ransburg, Rma-303 dual purge/direct charge - maintenance, Troubleshooting guide (cont.) – Ransburg RMA Dual Purge Direct A12300 User Manual
Page 84
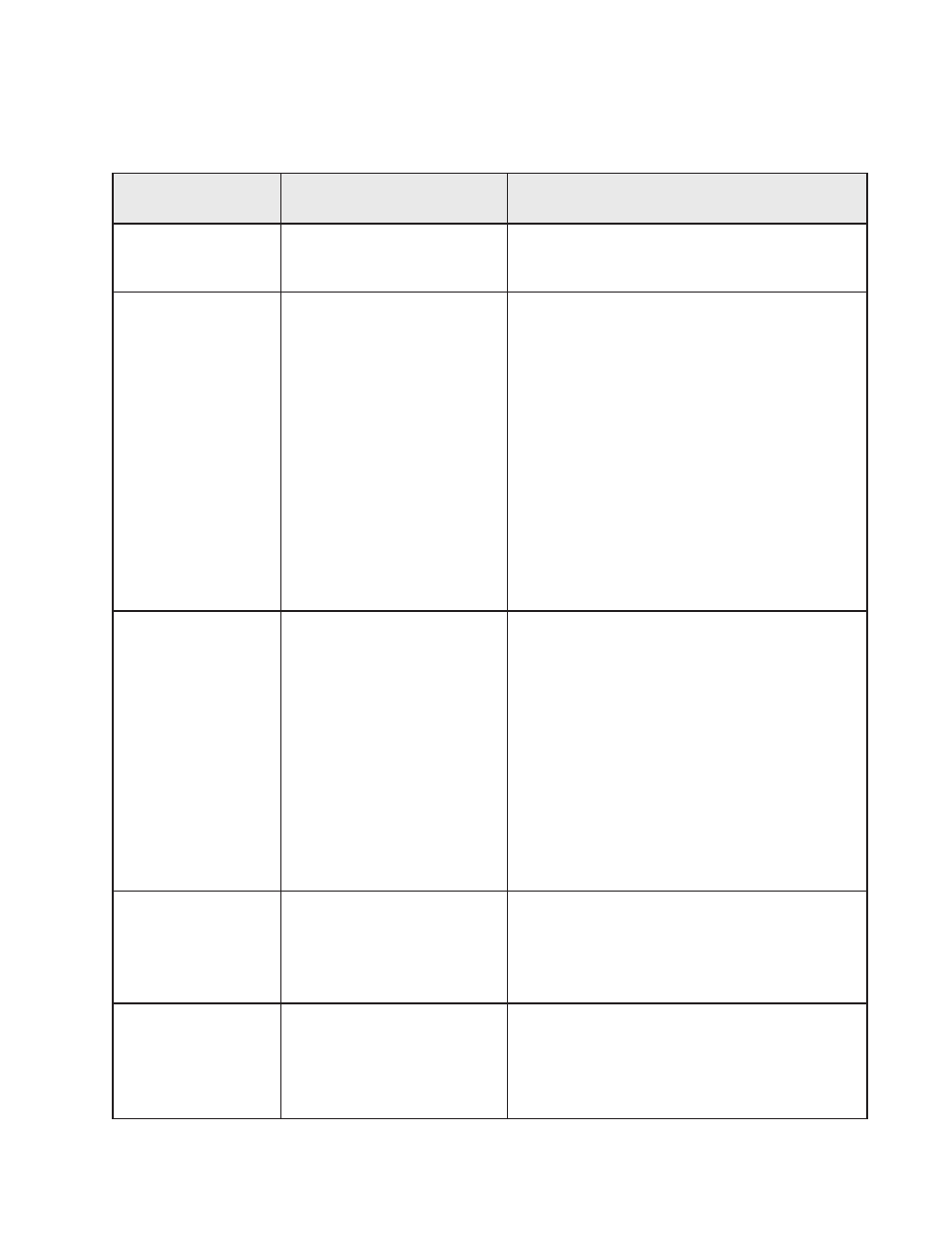
RMA-303 Dual Purge/Direct Charge - Maintenance
79
.
(Continued On Next Page)
Troubleshooting Guide (Cont.)
General Problem
Possible Causes
Corrective Action
No Turbine Air
(Cont.)
Speed Feedback
Fault
No Fluid Flow
Continuous Fluid
Flow
Uncontrollable
Fluid Flow
3. Brake air is activated
1. Damaged fiber optic ca-
ble between robot plate and
control panel
2. Connection at robot or
bell plate is loose
3. Fiber optic transmitter
failure
4. Bad transceiver module
5. Excessive vibration
1. Turbine is not rotating
2. Fluid valve does not actu-
ate
3. Clogged fluid tube
4. Bad transceiver module
1. Fluid valve open
2. Fluid valve seat dam-
aged or worn
1. Insufficient back pressure
to fluid regulator
2. Fluid regulator does not
control flow (system)
3. Remove brake air signal (turbine air and
brake air must be interlocked to prevent both
from being used simultaneously).
1. Repair or replace fiber optic cable.
2. Re-install cable and tighten locking set screw.
3. Replace fiber optic transmitter.
4. Replace transceiver module.
5. a. Check bell cup for damage.
b. Check bell cup for excessive paint buildup.
c. Insure bell cup is tightened properly.
d. Check cup and shaft tapers for cleanliness
1. Verify rotation of turbine (the paint valve air
pilot must be interlocked with the turbine
speed feed back signal to ensure that paint
does not flow into the air bearing).
2. a. Verfiy that air pilot signal is present.
b. Fluid valve air pilot pressure is too low.
Increase air pressure to 70 psig (482.6
kPa) minimum.
c. Replace fluid valve.
3. Remove and inspect fluid tube.
4. Replace transceiver module.
1. a. Remove air pilot signal.
b. If still open, replace fluid valve.
2. Replace fluid valve seat.
1. Replace fluid tube with the next smaller inner
diameter size.
2. Disassemble fluid regulator and inspect for
failed components (system).
Ransburg
LN-9263-08.5