Ransburg, Rma-303 dual purge/direct charge - operation – Ransburg RMA Dual Purge Direct A12300 User Manual
Page 52
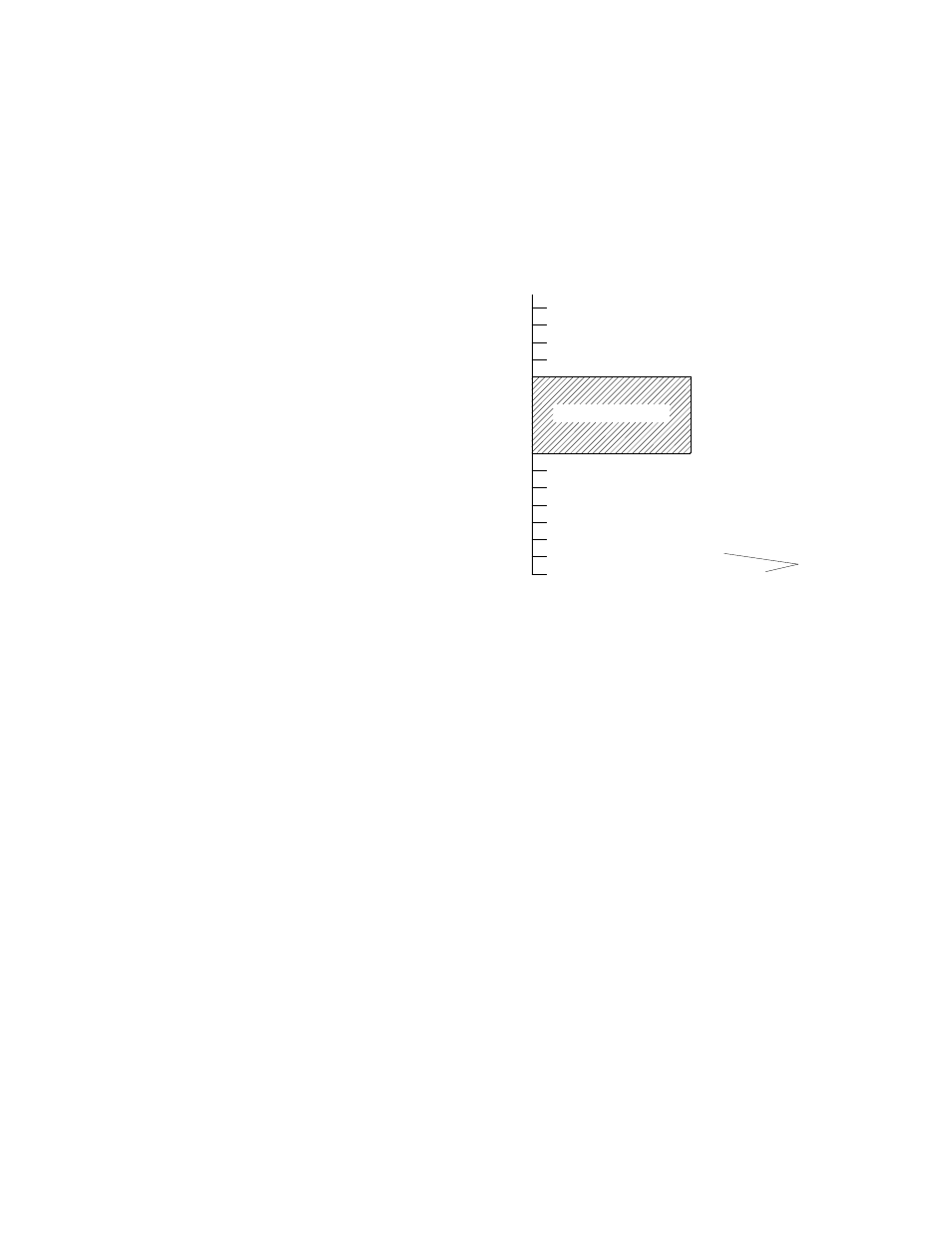
RMA-303 Dual Purge/Direct Charge - Operation
47
Ransburg
LN-9263-08.5
BELL TO SPEED
SHAPING AIR ON
VOLTAGE ON OR UP FROM SETBACK
FLUID TRIGGER ON
SPRAY TARGET
VOLTAGE OFF OR SETBACK
FLUID OFF
SHAPING AIR TO SETBACK FLOW
BELL TO SETBACK SPEED
INT/EXT CUP FLUSH
COLOR CHANGE SEQUENCE
AND/OR
SEQU
EN
CE
EV
EN
T
INTERLOCK - HV OFF
Figure 16: Typical Paint Sequence
5. Use an alternating trigger sequence of solvent/
air to create a chopping effect. Always insure that
the last step in the sequence is an air push.
6. A typical sequence is .3 seconds solvent, 1.7
seconds air push; repeat 3 times. This sequence
may be modified for other paint and applications.
Sequence Event Explanation:
1.
Bell to Speed - This is accomplished by a set
point command from either the PLC, robot, or other
input device, through the I/O module.
2.
Shaping Air - Set to 350-400 slpm while per-
forming a cup flush.
3.
Trigger Fluid - An air signal is sent through
the PT line of the tubing bundle. This should occur
when the target typically is 6-12-inches (152.4-
304.8mm) from the applicator centerline. (Not to
be confused with target distance.)
4.
Voltage On - The voltage is turned on from a
signal to the MicroPak. The lag time to full volt-
age may be reduced if a setback voltage is used.
Recommended setback voltage is between 30kV
and 50kV.
Recommended sample cup flush sequence is as
follows (voltage must be off) (internal and external
cup wash):
1. Turbine speed set to 25,000-30,000 rpm.
2. Shaping air only set to 350-450 slpm (12.4-
15.9 SCFM).
3. Point atomizer at a grounded object such as
a booth grate.
4. Maintain solvent pressure of 100-150 psi (689-
1,034 kPa). Maintain air push pressure at 80-100
psi (552-689 kPa).
5. Use an alternating trigger sequence of solvent/
air to create a chopping effect. Always insure that
the last step in the sequence is an air push.
A typical sequence is .2 seconds solvent, 1.0
second air push, 1.7 seconds solvent, and 2.0
seconds final air push. This sequence may be
modified for other paints and applications.
6. It is recommended that an in-line fluid filter be
installed to ensure that no foreign debris enters
the fluid tip or the external wash nozzle.
The RMA-303 is versatile in processing the finish
of a component. It can be setup as shown in
Figure 15 to process the typical finish of a target.
Recommended sample purge sequence is as fol-
lows (voltage must be off) (internal cup cleaning):
1. Turbine speed set to 25,000-30,000 rpm.
2. Increase inner shaping air to 350-450 slpm
(12.4-15.9 SCFM)
3. Paint atomizer at booth grate or insert into bell
cleaning station.
4. Maintain solvent pressure of 100-150 psi. (689-
1034 kPa). Maintain air push pressure at 80-100
psi (552-689 kPa).