Troubleshooting and maintenance, 1 troubleshooting, 2 maintenance – GE Industrial Solutions DC OEM Module For use with Gerapid DC Circuit Breaker User Manual
Page 22
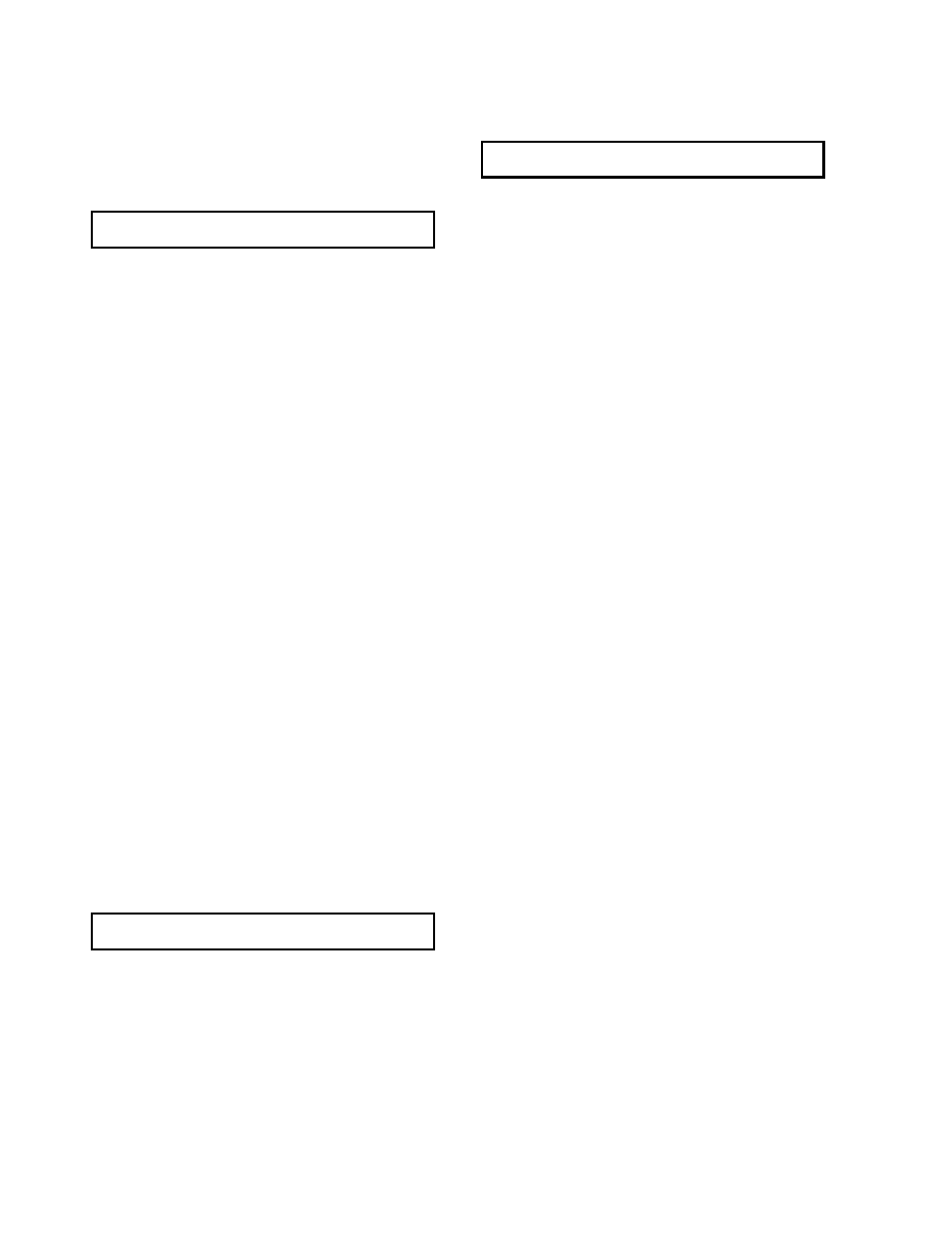
DC OEM MODULE FOR USE WITH GERAPID CIRCUIT BREAKERS
Chapter 9 Customer Support.
22
Design and specifications are subject to change without notice
S47183Ee rev.01 2011-04-26
Troubleshooting and Maintenance
8.1 Troubleshooting
Troubleshooting section describes potential issues that user
may experience during operation of the trolley. Contact GE
Energy service in case the problem is not resolved.
NOTE:
See User Manual S47183De for breaker
troubleshooting information.
Manually operated trolley
A. Cannot lift Access Lever to insert Crank Handle
Check if the breaker is OPEN. When CLOSED,
breaker’s drive rod activates interlock, which
locks the Access Lever.
Check the length of four M8 mounting screws
for the breaker. Screws may limit the movement
of the Access Lever if are longer than 25 mm
(1”).
B. Cannot trip the breaker by means of Trip Lever
Check the length of four M8 mounting screws
for the breaker. Screws may limit the movement
of the Trip Lever if are longer than 25 mm (1”).
Check the Forced Tripping Release pin under the
breaker’s base. The pin should be able to be fully
pressed against base. If this does not work, the
pin may be damaged inside the breaker.
C. Cannot move the trolley using Crank Handle
Check if Crank Handle is properly and fully
inserted into Access Slot. The crank engages
fully with the shaft only with proper orientation
of the handle.
Check if Crank’s clutch is set at minimum 50 Nm.
D. Cannot rack-in the trolley into DISCONNECT / TEST
position
Check point C.
Check if rating Rejection Interlock of the trolley
and the module match.
Check if Racking Shaft is bent.
Check if Indicator Shaft is jammed.
E. Cannot rack-in the trolley into CONNECTED
position.
Check point C.
Check if Secondary Disconnect is connected.
Check if shutters are jammed or closed.
F. Cannot rack-out the trolley from TEST position.
Check if Secondary Disconnect is disconnected.
Check if Access Lever is lifted up.
Motor driven trolley
NOTE: Check points A thru F are also valid for motor driven
trolley. Refer to them in case of related issues.
G. Cannot rack-in the trolley to CONNECTED position.
Check if Access Lever is in down position.
Check if motor thermal overload protection
GPS1B is activated.
Check if end switch S4F is activated.
Check if end switch S3F is activated.
H. Cannot rack-out the trolley from CONNECTED
position.
Make sure the breaker contacts are OPEN.
Check point G.
8.2 Maintenance
NOTE: See User Manual S47183De for complete breaker
inspection and maintenance routines.
Expected service life of the OEM module is 20 years, with MTBF
exceeds 2,000 racking operations. The module and trolley
construction is nearly maintenance free. The system is
designed to operate during specified period and in prescribed
conditions without functional part replacement. Only simple
preventive maintenance is recommended to be performed
every two years:
Check the racking shaft of the trolley and grease it with
molybdenum based grease, such as MOLYKOTE G4700
or NYE Rheolube® 373. Also grease racking socket in
the structure.
Check the Primary Disconnect clusters. Clean and
apply a light coating of red Mobile
28 grease,
manufactured by ExxonMobil.
Perform testing routine as listed in Appendix H, tables
H3 or H4.